
Quality is the key to ensuring that the products and services a company provides are reliable and effective. But what exactly is quality? There are many definitions for it, each of them emphasising a specific aspect. But in the end, quality is whatever the customer thinks it is.
This is why GE Healthcare puts the customer first and the company’s ‘quality journey’ (see Figure 1) evolves across three layers, with customer experience at the top, over product quality (the heart of the matter) and quality management system (the foundation). Clear and simple metrics have been established to track, in each layer, the progress of GE Healthcare’s journey towards excellence:
Customer experience.GE Healthcare measures customer loyalty through a Net Promoter Score (NPS). On a scale of zero to ten, GE Healthcare asks customers how likely they are to recommend the company to their friends and colleagues. An NPS score measures the difference between the percentage of promoters (those giving high scores) and detractors (those giving low scores).
Product quality. The company measures perceived product reliability through Infantile Failure Rate (IFR) and Mean Failure Rate (MFR) scores, available by segments and products.
Quality management system. GE Healthcare measures compliance to quality policy, quality manual and functional procedures through Global Audit Council (GAC) audit scores. The company monitors the score of each site using its internal audit checklist. The vision of GE Healthcare’s quality journey drives it to improve customer perceptions and product quality, and enhance the quality of its management system. The metrics are used to monitor the progress the company makes. This framework is supported by three continuous improvement methodologies that complement each other:
- Quality Management System
- Six Sigma
- Lean Six Sigma
QUALITY MANAGEMENT SYSTEM
How well do you really know your competitors?
Access the most comprehensive Company Profiles on the market, powered by GlobalData. Save hours of research. Gain competitive edge.
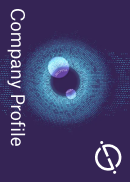
Thank you!
Your download email will arrive shortly
Not ready to buy yet? Download a free sample
We are confident about the unique quality of our Company Profiles. However, we want you to make the most beneficial decision for your business, so we offer a free sample that you can download by submitting the below form
By GlobalDataThe first approach to quality management, used from the 1960s to the 1980s, was to have the product you designed, manufactured and wanted to market quality-certified by a third party. Although this was convenient at the time, it meant that companies had to re-qualify whenever there was a slight modification to an existing product or a new product was introduced.
Today, this approach would not be feasible, due to the high volume of new products being introduced in the marketplace. As a result, in Europe the CE marking has much more to do with certifying the organisation designing, manufacturing and marketing the product than the product itself. In the USA, Good Manufacturing Practice (GMP) has been established, now known as current Good Manufacturing Practice (CGMP).
Although each GMP code worldwide has similar concepts, there are key differences. In the GMPs of the EU, responsibility for ensuring that medical products are manufactured in accordance with the manufacturing and testing methods registered with the authorities rests with the ‘qualified person’ or the ‘responsible person’. These individuals take personal and legal responsibility, certifying that each batch of products has been produced in accordance with the marketing authorisation and the GMPs. In the USA, the responsibilities of the qualified person are vested with the company’s quality assurance group. Ultimate responsibility rests with the CEO of the company, who would pay any fines and serve any jail sentences that might be imposed.
The latest quality system regulation will make standards for US medical devices consistent with quality system requirements worldwide, thereby meeting the important goal of global harmonisation. The new standards closely follow the international ISO 9001 standard and fulfil a mandate of the Safe Medical Devices Act of 1990 to harmonise requirements.
NEW STANDARDS
In 1987, the International Standard Organization launched a new quality system management standard known as ISO 9000. This standard measures companies to a predefined quality standard (the reference). If the standard is met, the organisation is certified, which means that it:
- Fulfils customers’ quality requirements
- Is compliant with applicable regulatory requirements
- Enhances customer satisfaction
- Continually improves performance
‘Management system’ refers to the organisation’s structure for managing processes – or activities – that transform inputs of resources into a product or service that meets the organisation’s objectives, such as satisfying the customer’s quality requirements, complying to regulations or meeting environmental objectives. ISO 9001:2000 specifies requirements for a quality management system where an organisation needs to demonstrate its ability to meet both customer and regulatory requirements. ISO 13485:2003 specifies requirements for a quality management system where an organisation needs to demonstrate its ability to provide medical devices and related services that consistently meet customer and regulatory requirements.
The use of CGMP and ISO standards are complementary, with the former focusing on effectiveness and the latter more on the process itself and how to ensure it continues to evolve. Both CGMP and ISO are fundamental for organisations wanting to deliver quality products and services.
GE Healthcare has worked on applying these standards and has been measured by internal and external bodies for compliance and adherence to these values. This has been a real challenge, especially making sure that GE Healthcare’s 25-plus design and / or manufacturing working sites in 19 countries are at the same level in terms of organisation, framework and discipline to guarantee equal and unquestionable product quality.
Although important, a quality management system is not sufficient in itself for reaching a high level of quality. This is why, in recent years, Six Sigma has been the major initiative driving GE Healthcare to the next level.
SIX SIGMA
GE Healthcare began focusing on quality in the late 1980s. Work-Out®, the start of the journey, opened the company’s culture to ideas from everyone, eliminated the bureaucracy and made open-minded thinking a reflexive, natural part of the culture, thereby creating the learning environment that led to Six Sigma (see Figure 2). Bob Galvin and Bill Smith developed Six Sigma at Motorola in 1986. Two big early adopters helped popularise the term as well as the method: AlliedSignal (now known as Honeywell) and General Electric in 1995. Today, Six Sigma embeds quality thinking – process thinking – across every level and every operation of GE Healthcare around the globe.
In the 1980s, Work-Out defined how the medical device industry behaved. Today Six Sigma is at the forefront in defining how it works. Globalisation and instant access to information, products and services have changed the way the industry’s customers conduct business – old business models no longer work. Today’s competitive environment leaves no room for error. We must meet customers’ needs while also looking for new ways of exceeding their expectations. This is why Six Sigma quality has become a part of our culture.
So what is Six Sigma? First, let me explain what it is not. It is not a secret society, a slogan or a cliche. Six Sigma is a highly disciplined process that helps us focus on developing and delivering near-perfect products and services. Why Sigma? The word is a statistical term that measures how far a given process deviates from perfection. The central idea behind Six Sigma is that, if you can measure how many ‘defects’ you have in a process, you can systematically figure out how to eliminate them and get as close to zero defects as possible. Six Sigma has radically changed GE Healthcare in everything the company does and every product it designs.
There are three key elements to quality: customer, process and employee. Everything the company does to sustain world-class quality focuses on these three essential elements:
The customer – delighting customers. Customers are the center of GE Healthcare’s universe. Customers define quality, and they expect performance, reliability, competitive prices, on-time delivery, service, clear and correct transaction processing, and more. With every attribute that influences customer perception, GE Healthcare knows that just being good is not enough. For GE Healthcare, delighting its customers is a necessity, because if it doesn’t, someone else will.
The process – outside-in thinking. To provide quality, GE Healthcare looks at its business from the customer’s perspective; it looks at its processes from the outside-in. By understanding the transaction life cycle and the customer’s needs and processes, it is possible to discover what the customer is seeing and feeling. With this knowledge, areas can be identified where significant value can be added or improvements made.
The employee – leadership commitment. People create results. Involving all employees is essential to GE Healthcare’s quality approach. The company is committed to providing opportunities and incentives for employees to focus their talents and energies on satisfying customers.
All GE Healthcare employees are trained on the strategy, statistical tools and techniques of Six Sigma. Training courses are offered at various levels:
- Quality overview seminars for basic Six Sigma awareness
- In-depth quality training that includes teaching on high-level statistical tools, basic quality control tools, change acceleration process and flow technology tools For
- Design Six Sigma (DFSS) training, which teaches teams to use statistical tools to get their designs right first time
Quality is the responsibility of every employee. Each employee must be involved, motivated and knowledgeable if the quest for quality is to succeed. To achieve Six Sigma quality, a process must produce no more than 3.4 defects per million ‘opportunities’. Opportunities are defined as a chance for non-conformance or for not meeting the required specifications. This means that companies need to be nearly flawless in executing their key processes. Six Sigma is a vision GE Healthcare strives towards and a philosophy that is part of its business culture.
At its core, Six Sigma revolves around a few key concepts:
- Critical to quality: attributes most important to the customer
- Defect: failing to deliver what the customer wants
- Process capability: what your process can deliver
- Variation: what the customer sees and feels
- Stable operations: ensuring consistent, predictable processes to improve what the customer sees and feels
- Design for Six Sigma: designing to meet customer needs and process capability
Often, an inside-out view of a business is based on average- or mean-based measures of the recent past. But customers don’t judge performance on averages, they feel the ‘variance’ in each transaction and each product shipped. Six Sigma focuses on reducing process variation and then on improving the process capability.
LEAN METHODOLOGY
In 1956, Taiichi Ohno, who began in the Toyota machine shop in 1940, discovered the US automotive industry in 1956 while visiting the country. He brought these new ideas from his visit back to Japan, where he developed what is known as lean manufacturing. Lean manufacturing is a best practice that identifies sources of waste in a company: over-production, waiting time, transportation, over-processing, inventory, motion and scrap. The lean machine philosophy aimed to:
- Specify value in the eyes of the customer
- Identify the value stream and eliminate waste
- Make value flow in response to the customer
- Involve stakeholders and empower employees
- Continuously improve in the pursuit of perfection
In combination with Six Sigma, lean practices improve processes to decrease costs, reduce lead times and enable companies to better meet the needs of their customers. This is the ultimate development stage that GE Healthcare is currently implementing internally to meet its customer needs.
Today, GE Healthcare is using these tools and methodologies to help it improve processes (clinical, operational and management) in many hospital departments – in the diagnostic imaging department, the emergency room and the operating theatre, for example. With its Performance Solutions product line, GE Healthcare can either help its customers apply GE Healthcare tools in specific projects or transfer its expertise directly to hospital staff through extensive hands-on training and changes to management techniques.
In this way, GE Healthcare has obtained the following results:
- Patient flow improvements in a diagnostic imaging department, resulting in a 55% reduction in patient waiting time in the first three months
- Exam process and planning for Artoscan in a private hospital, resulting in a reduction in the average cycle time to 31 minutes, increasing by five the number of patients treated per day
- Implementation of a dashboard for an MRI department, leading to improved visibility for staff, better monitoring of defects and improvement in the overall throughput
- Bringing business processes to a public hospital with over 800 beds through methodology training for 45 top staff members, resulting in a 24%throughput improvement in CT and a reduction in length of stay for 33% of patients
THE QUALITY JOURNEY
General Electric’s 1996 annual report stated: “It has been estimated that less than Six Sigma quality, that is the three-to-four Sigma levels that are average for most US companies, can cost a company as much as 10% to 15% of its revenues. For General Electric, that would mean $8bn to $12bn. General Electric has estimated the benefits of Six Sigma to be in the order of $10bn during the first five years of implementation. This effort will complement the quality management system framework discussed earlier.”
Today’s healthcare organisations face tough challenges, including concerns over medical errors, malpractice, workforce shortages, ineffective operations and rising costs. As well as new technologies, meeting these challenges and improving service quality will require a new knowledge base and access to relevant resources. GE Healthcare is assisting healthcare professionals in finding and using these resources to create sustainable change while embracing tools and methodologies relating to quality.