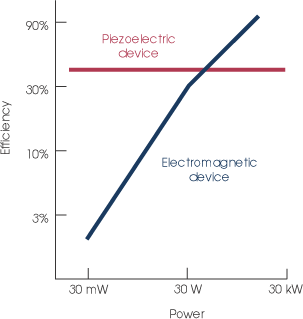
Piezoelectric actuators are now becoming widely used in the medical applications as an alternative to electromagnetic motors, as they offer a number of clear benefits compared with their electromagnetic motor equivalents. Piezoelectric actuators are
better suited to miniaturisation than EM motors.
Market research results from 80 Japanese component manufacturers showed that tiny motors in the range of 5mm to 8mm are highly sought after for use in automated office and factory equipment. However, conventional EM motors are rather difficult to
produce with sufficient energy efficiency. Since the stored energy density of a piezo-device 10 times larger than that of an EM type, they can be 1/10 in volume and weight.
Another advantage of piezo-motors is that they do not generate electromagnetic noise. Since magnetic shielding is not necessary, the design can be kept compact. This unique characteristic is particularly desirable for motors used in strong magnetic
fields, such as in MRI equipment, where large piezo-motors are used for rotating a patient or equipment and small piezo-motors for MRI monitored microsurgery.
HIGH EFFICIENCY
Piezo-motors are also preferable to EM motors because of their higher efficiency. Figure 1 shows the efficiency versus power relation for electromagnetic and piezoelectric devices. The significant decrease in the efficiency of the EM motor is mainly
due to the Joule heat increase in reducing the coil wire thickness – more than 95% of the input electrical energy in a wristwatch motor is spent generating heat. Since the efficiency of the piezo-device is not determined by its size, it is
effective in the power range lower than 30W. This characteristic makes piezo-devices attractive for use in battery-operated portable and wearable medical devices, as they can extend the life of a given battery by more than ten times.
Another advantage of piezo-devices is that they are inflammable and safer in the event of an overload or short-circuit at the output terminal. Again, this is a big advantage on portable and wearable devices.
How well do you really know your competitors?
Access the most comprehensive Company Profiles on the market, powered by GlobalData. Save hours of research. Gain competitive edge.
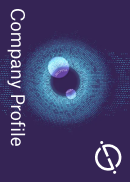
Thank you!
Your download email will arrive shortly
Not ready to buy yet? Download a free sample
We are confident about the unique quality of our Company Profiles. However, we want you to make the most beneficial decision for your business, so we offer a free sample that you can download by submitting the below form
By GlobalDataMEDICAL APPLICATIONS
Piezoelectric devices have recently been used successfully in a range of medical applications, including an artificial fertilization system, a medical micro-pump, micro-monitoring and surgery devices and drug delivery devices.
Applied Micro Systems (in Japan) and Micromechatronics, Inc (in the USA) have commercialised an artificial fertilization system micro-robot, which consists of four electromagnets (for clamping) and four multilayer actuators (for translation). The
robot works on an ‘inchworm’ motion principle on a steel surface with 30nm movement resolution. Micro-tools such as tweezers, scissors and drillers are available in conjunction with the robot base, for manipulating nano-particles and fibres.
Because of the high responsiveness of the piezo-actuator in comparison with a normal hydraulic oil pressure system, sophisticated artificial fertilisation systems have been developed. Figure 3 shows the egg deformation difference during the needle
insertion process for the micro-robot and Figure 4 for that of a conventional oil-pressure system. The deformation can be minimised by using a piezo-actuator because a 100Hz high-frequency motion can be superposed on the needle.
PZT thin films can be deposited on a silicon wafer, which is then micro-machined to leave a membrane for fabricating micro actuators and sensors, such as micro-electromechanical systems.
A blood tester developed by Pennsylvania State University in collaboration with Omron Corporation, Japan, applies a voltage to two surface interdigital electrodes, the surface PZT film then generates surface membrane waves, which soak up blood and the
test chemical from the two inlets, mix them in the centre part and send the mixture to the monitor through the outlet.
A finite element analysis calculation was conducted to evaluate the flow rate of the liquid by changing the thickness of the PZT or the silicon membrane, inlet and outlet nozzle size and cavity thickness, and the performance was verified
experimentally.
Pennsylvania State University is developing various microrotary motors (1mm to 5mm in size) for applications in micromonitoring and surgery. A micro-motor, called a metal tubetype motor, consisting of a metal hollow cylinder and two PZT rectangular
plates was used as basic micro actuators (see Figure 2). When we drive one of the PZT plates, plate x, a bending vibration is excited along the x axis. However, because of the asymmetrical mass (plate y), another hybridised bending mode is excited with
some phase lag along the y axis, leading to an elliptical locus in a clockwise direction.
The rotor of this motor is a cylindrical rod with a pair of stainless ferrule pressed with a spring. The metal cylinder motor, 2.4mm in diameter and 12mm in length, was driven at 62.1kHz in both rotation directions. A no-load speed of 1,800rpm and an
output torque of up to 1.8mN/m were obtained for rotation in both directions under an applied root mean squared voltage of 80V. A rather high maximum efficiency of about 28% is a noteworthy feature of this small motor.
In collaboration with Samsung Electromechanics, the Pennsylvania State University developed the world’s smallest camera with an optical zooming and auto-focusing mechanism for a cellular phone application. Two micro-ultrasonic motors with a 2.4mm
diameter and 14mm length were installed to control the zooming and focusing lenses independently in conjunction with screw mechanisms. Further downsizing to 3mm is possible for endoscope monitoring devices. Micro-motors less than 3mm in size (commercially available from Micromechatronics Inc.) are very useful for microsurgery or minimal invasive surgery.
The University of Washington, in collaboration with Pennsylvania State University, is developing a side view monitoring endoscope / gastroscope using micro motors. High-power ultrasonic technology is highly applicable to transdermal drug delivery.
Pennsylvania State University researchers are currently working on the commercialisation of a needle-free insulin injection system by using compact but powerful ‘cymbal’ piezo-actuators.