
Coatings are used in the medical device industry to modify surfaces for many reasons, not least of which is to provide or enhance the biocompatibility of the device being coated. Surfaces are also modified to enhance electrical and frictional properties, to provide chemical and moisture barrier properties, to improve the hygienic properties of the surface, and sometimes simply to improve the cosmetic perception of the product.
Coatings may also be used to facilitate the application of other coatings, for instance as a tie layer or primer, and to control the extraction or release rates of compounds from within substrate materials.
While there is no lack of materials from which to fabricate today’s medical device marvels, it is not always the case that the material of choice, from a bulk or structural properties perspective, meets the biological or toxicological requirements. Even when all the material criteria are fulfilled, it is still possible that a related adjacent component or system may not be compatible as it is, necessitating a surface modification to one or both of the contacting surfaces. Therefore, it is that surface modification – in other words, the coating – that enables the use of an otherwise unacceptable substrate material.
The issues that surface coatings can resolve range from simple dielectric protection to enabling the application of a subsequent coating onto a non-receptive material. The challenge might, for example, be one of modifying the surface energy of a material so that a droplet of blood or other fluid will move through a capillary tube more homogenously, more quickly or more slowly.
A catheter might be coated to enhance its lubricity or to reduce encrustation (in urinary catheters). The purpose of the coating might be to suppress tin whisker growth on a printed circuit board or simply to protect the device from tissue or body fluids. For a medical device, the coating might provide an additional assurance of biocompatibility.
Various roles in coating methods are played by the unique polymer family, poly(para-xylylene), more commonly known as Parylene. Parylenes are solvent, catalyst and plasticiser-free organic coatings that have an impressive array of attributes, including: excellent chemical inertness and resistance; superior chemical, fluid, gas, moisture and electrical barrier properties; coefficients of friction in the PTFE range; and temperature performance to 450°C. Parylenes are biostable and biocompatible, having passed an impressive array of ISO 10993 and USP biological evaluations.
How well do you really know your competitors?
Access the most comprehensive Company Profiles on the market, powered by GlobalData. Save hours of research. Gain competitive edge.
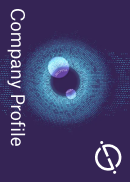
Thank you!
Your download email will arrive shortly
Not ready to buy yet? Download a free sample
We are confident about the unique quality of our Company Profiles. However, we want you to make the most beneficial decision for your business, so we offer a free sample that you can download by submitting the below form
By GlobalDataTHE DEVELOPMENT OF PARYLENE
In a classic case of serendipitous discovery, poly(para-xylylene) was found by Dr Michael Szwarc, a Second World War refugee from Eastern Europe. In 1947, Szwarc had embarked upon an academic career in physical chemistry at the University of Manchester, UK. Experimentally, he heated a number of gaseous compounds, including toluene and the xylylene, to extremely high temperatures. He then observed the degradation products and the rates at which they decomposed as a function of temperature.
In the case of xylylene, a film formed downstream from the high temperature zone in the cooler extremities of Szwarc’s glassware. This thin film could be removed from the glassware as a tube-shaped skin, described as ‘the skin of a small snake’. Szwarc correctly deduced that this film had been formed by the polymerisation of a specific reaction product of p-xylylene. This ‘snake skin’ was the world’s first vapour-deposited poly(para-xylylene), Parylene, which in its pure and colourless form is known today as Parylene N.
THE PARYLENES AND COMMERCIALISATION
Szwarc’s work inspired vigorous research in a number of industrial laboratories, not least of which were ICI in the UK and DuPont, Kellogg, Polaroid and Union Carbide in the US. This preliminary work culminated in the issuance of a patent to Dr. Gorham and UCC in 19675, heralding the availability of a new polymeric coating system, the Parylenes, consisting of both a new family of polymers and a unique vacuum method for applying them. Today, the vapour deposition polymerisation process, casually known as the Gorham Process, is the commercial Parylene coating process used throughout the world.
Gorham and his colleagues at Union Carbide created more than 20 Parylene variants, but only three were considered worthy of commercialisation. A fourth, Parylene HT®, has been recently introduced, with a similar structure to the currently available Parylenes.
BIOCOMPATIBILITY OF PARYLENE
In addition to its various physical properties, Parylene is also known for its inherent biocompatibility. Certification for ISO 10993 and USP Class VI biological studies can be referenced via the FDA Master File mechanism. Notified Bodies and accredited third parties can also reference such data from those Parylene coating service providers who maintain such files. Various biological evaluations have been performed on Parylene HT, C and N by third-party laboratories. Parylene D is not used in the medical device and drug industries and its toxicological properties are largely unknown.
PROPERTIES AND APPLICATION
Parylene’s ability to meet a multiplicity of needs has resulted in its use in many settings. Its ability to be applied to such diverse substrates as glass and ceramics, paper and fabrics, metals and plastics/elastomers, and even to powders, has aided its use in diverse industries, including the electronics, automotive, aerospace and military industries. But it is in the medical device industry where Parylene has truly found its calling. It is in medical devices where Parylene’s array of properties seems to be most fully appreciated
Parylene is a polymer of many roles. It is a barrier to electricity, chemicals, moisture and fluids. It is lubricious and hydrophobic and often used as a primer, such as for drug-eluting stents. It is transparent to visible light and tolerant of high temperatures and sterilising agents. Most important to the medical device industry, it provides all these properties while being chemically inert, free of plasticisers, solvents and catalysts, and therefore inherently biocompatible.
Parylene’s science is relatively easy to understand, but the artistry of its application can be complicated. It demands great attention to cleanliness for its application, but is itself immune to most environmental contamination.
It finds application in down-hole drilling devices and on coronary and cerebral stents. It has travelled to Mars and through the human digestive tract. It saves lives in pacemakers and ICDs, enhances lives in cochlear and ocular implants.
Parylene has been providing its unique properties to medical devices for over 35 years, yet it finds new applications every day.
The role that initiated Parylene into commercial use continues undiminished today. As a reliable, high-performance printed circuit board conformal coating, Parylene has few equals. Its ability to completely encapsulate a PCB, all its components and whole devices is unmatched. For implanted and/or mere tissue-contact devices, its biocompatibility, biostability and barrier performance assure that Parylene will play an important role in the micro and nano medical devices of the future.