
Hospital beds – manual, hydraulic and electric – have evolved over the years all over the globe. Several latest devices are available for a patient situated on a hospital bed to activate several functions such as adjust bed/mattress, call nurse and turn lights/TV. A number of manufacturers are competing to produce the most effective solution to bed motion control.
Galaxy Medical is a China-based company that produces electric hospital beds using three motors for the whole bed surface to rise up and down, back surface to rise 80° and foot surface to rise 40°. A Swedish company, Proton Caretec, boasts its EVAB hospital bed that has three-parted bed base with cardiac position, and is hydraulically height adjustable with back/leg rests operated by gas springs.
There are several hospital beds in the US market, such as a fully electric adjustable bed by Invacare, with a hand pendent controller that uses a series of open-loop switches; an air-powered adjustable bed employing inflatable pillows by ProBed; and the Flex-A-Bed Base frame which supports any type of mattress and adjusts the bed electronically.
Chongqing MKY Trading Co. in China manufactures medical beds that have longitudinal tilt, lateral tilt, accurate avoirdupois measure, dual-regress function during back rest and thigh rest and such comprehensive functions to resolve the problem of bedsore in the intensive care units. Merivaara Corp. in Finland has a line of light and handy hospital beds, enhancing ease of patient rehabilitation.
There are over 320 products in hospital beds from more than 160 companies situated all over the globe.
REVOLUTIONARY RESEARCH
How well do you really know your competitors?
Access the most comprehensive Company Profiles on the market, powered by GlobalData. Save hours of research. Gain competitive edge.
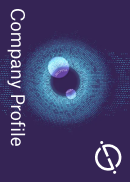
Thank you!
Your download email will arrive shortly
Not ready to buy yet? Download a free sample
We are confident about the unique quality of our Company Profiles. However, we want you to make the most beneficial decision for your business, so we offer a free sample that you can download by submitting the below form
By GlobalDataIn spite of the latest technological advances, in terms of motion control, there are still some challenges. Currently available hospital beds have problems associated with the rate at which motorised sections move and the methods required to remove patients from the beds. They use open-loop control to set the back angle and have a slow constant velocity; hence, they do not allow for easy adjustment by patients with limited mobility and dexterity.
The Rehabilitation Engineering Research Center on Accessible Medical Instrumentation in the US conducted a national student design competition during the 2006–07 academic year. The aim of one of the projects in the competition was to design a reliable, easy-to-use, extended physiologic proprioception-based power-assist hospital bed angle controller. Eight undergraduate senior design teams from eight universities took up the challenge. Each team was provided with up to $2,000 in design
costs.
The winner of the competition was a team from the University of Connecticut who came up with a portable, easily installed or removed, cost-effective, automatic lift mechanism, as a universal fit to basic hospital bed models, with or without side railing. With smooth operation, infinitely adjustable speed, and ergonomic and intuitive control, functionality is achieved at a minimum cost. The bed is lifted by an electric motor driving a scissor jack.
A simple potentiometer and a circuit with a safety switch are used to vary the speed and direction of the electric motor. Because of the ease of operation, and minimal required force to operate, patients and caregivers of all ability levels and strength will benefit a great deal from using an adjustable back angle controlled bed.
A FLEXIBLE DESIGN
The Milwaukee School of Engineering team, which won second place in the competition, proposed that a variable force-activated switch be incorporated into the current hospital bed design to allow the adjustment of the rate of angular movement of the back section by the caregiver and patient alike. Another degree of rotation was also added to the bed to allow it to assist the patient in standing up.
For motor control, the DC design was chosen due to DC motors being able to have their speed controlled more easily, not losing power quality with speed reduction and due to the DC design’s lower power consumption. This lower power consumption characteristic allowed the motor to be controlled by the speed varying circuit without the presence of an external amplifier. The proper motor was chosen based on the torque requirement estimated for the hospital bed back linkage in its full reclined position.
The design chosen for the standing assist was a lengthwise folding mechanism to essentially lift three fifths of the bed, moving the patient into a position where their feet are below them, to assist them in standing up. This also required the design of a linkage and selection of a linear actuator to move the bed components into the described position.
An actuator that worked on 90v DC was needed in order to be controlled on the same circuit as the motor that changes the back angle of the hospital bed.
The design to lift the standing assist platform has the actuator pulling a link that is slightly longer than the side of the bed it is lifting. This link connects to the actuator and a small fixed link that connects to the side being lifted.
The actuator pulls the long link which erects to increase the angle of the standing assist platform. The stand assist can only work while the bed is flat so that it does not interfere with the other ranges of motion that the hospital bed currently has.
The controller handle design chosen is a joystick lever with a torsion spring that runs a potentiometer. This design was found to be very simple and cost effective, but its most advantageous feature is that the force needed for operation can easily be translated from mechanical energy to the electrical energy needed to drive to motor or actuator.
To have the controller work with the motor and electronic parts of the system, a few parts were found to complete the required jobs. A joystick served the purpose of housing the potentiometer and the torsion spring while linking these two components with a handle. Four torsion springs were mounted with the joystick aligned to the rotation axis with the potentiometer, one for each direction of movement.
While in operation, 1–20lbs of force is needed to move the handle. When the handle is pushed harder, it moves further and will change the rotation of the potentiometer more. When the potentiometer is rotated more, a larger voltage is sent to the motor or actuator and they will move faster.
The controller joystick and springs are housed in a box and this box is mounted onto the side rail of the bed with the option of being moved since it is only mounted by a clip. This makes the controller capable of being moved to the most comfortable position for the patient and it can be operated without having been mounted on the side rails if so desired.
CENTRAL CONTROL SIMPLIFIES SYSTEM
In order for this project to come together, one central electrical control system needed to be developed to provide the variable speed requirement, as well as control for the motor and the linear actuator. The pulse width modulator (PWM) controller accepts a potentiometer input to vary the speed of its output with a potentiometer controller. Since there are two devices to be controlled, the solution to the required potentiometer input on the PWM was to incorporate a duel-axis joystick controller. This allowed one axis to control both directions of the motor and the other to control both directions of the linear actuator.
Due to the hospital bed having two differing degrees of freedom (back and foot angle versus side angle) three contact switches were installed to prevent conflicting geometry. The contact switches were placed to prevent current flow from the opposing potentiometer axis if the bed is not in its full reclined position and side angle down. In order to have four potentiometer outputs going to the one input on the PWM, a series of diodes were incorporated to cancel out voltage from the other three degrees of freedom once the desired direction is chosen.
Relays were used to switch the polarity of the motor and linear actuator to provide both directions of movement from each. A third relay was used to switch the negative terminal on the PWM between the motor and linear actuator so that only one will run at once. In order to power the relays and the joystick, a small 12V power supply was incorporated into the circuit. Two more diodes were used near the negative switching relay to prevent current flow issues.
The control circuit allows the bed back angle to be raised and lowered with the up/down movement on the joystick while the left/right movement of the joystick will allow the side angle of the bed to be raised and lowered. Opposing movements cannot be activated at the same time, nor until the other is in its fully retracted position (bed completely reclined and flat).
POSSIBILITIES FOR PATIENT INTERACTION
The MSOE student design offered a safe, clean and reliable system to provide a variable speed and intuitive operation of an adjustable bed. Six other teams also participated and provided their solutions for this project idea. This competition was a reminder that there are always further opportunities to be explored that are sensitive to patient care.
An amazing medical technology breakthrough in recent months is a system based on brain-computer interface technology. Paralysed patients can express their intentions through eyesight to manage tasks such as adjusting a comfortable angle for their motor-driven hospital beds.
This system, being developed at the National Central University, Taiwan, currently allows for 12 commands per minute with 92% accuracy in distinguishing these commands. It undeniably provides hope for patients whose eyeballs are the only part of their bodies they can move, offering them management of some parts of their life with the help of an instrument, and resulting in greater confidence to help them face their disability. (Taiwan Journal, Vol. 24, No. 48, December 7, 2007).