Medical devices are as varied as the applications for which they are intended. Whether permanent or temporary, internal or external to the body, for therapy or diagnosis, they continue to become more complex both in terms of performance specification and the challenges they pose to their manufacturers.
As interest grows in new approaches to medicine, such as minimally invasive or robotic surgery; tissue engineering and regenerative medicine, the demands placed on instrumentation, control systems and surgical tools become greater.
START RIGHT
Like most products, medical devices comprise more than one material or component. The method by which components are joined will impact, not only on the cost and efficiency of production, but also on their performance, reliability and ultimately, their safety. The use of adhesives for assembling or sealing components in general and implantable medical devices has increased significantly in recent years and adhesives are now a popular method of joining different materials in a wide variety of applications.
Selecting the right adhesive for the application is critical to success, as is the need to understand and comply with relevant ISO or US FDA regulations. Also important is matching the adhesive and materials to the procedure for surface preparation, the technique for adhesive application and the curing method.
TYPES OF ADHESIVE
How well do you really know your competitors?
Access the most comprehensive Company Profiles on the market, powered by GlobalData. Save hours of research. Gain competitive edge.
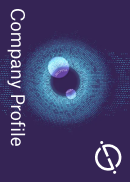
Thank you!
Your download email will arrive shortly
Not ready to buy yet? Download a free sample
We are confident about the unique quality of our Company Profiles. However, we want you to make the most beneficial decision for your business, so we offer a free sample that you can download by submitting the below form
By GlobalDataThe choice is complicated by the range of adhesives available. While many have been approved for use in medical products, either inside, or outside of the body, some adhesives have approval only for short-term use, such as 30 days. The most common types are based on acrylics, epoxies, polyurethanes and silicones.
Acrylic-based adhesives are used already to join a variety of similar and dissimilar materials. The main types include cyanoacrylates, anaerobics and modified acrylics. These may be polymerised or cured using moisture, catalysts, heat, UV, visible light or other sources of radiation. UV acrylics and cyanoacrylates are of particular interest to the medical industry, both for joining medical devices and as bonding agents for soft and hard tissues. Pressure-sensitive tapes or film adhesives are also used in medical applications, such as wound dressings and nicotine patches.
Epoxies, too, have been used successfully in medical devices for bonding and sealing applications. Assuming the adhesion to a specific substrate material is satisfactory, this type of adhesive provides better service performance than other medical grade adhesives, particularly in load-bearing applications, and where exposure to more aggressive sterilisation is required.
Silicones have found many uses within the body within implants. The most important types of silicone used in medical implants are fluids, gels and elastomers. These silicones are normally lightly cross-linked polysiloxane networks, swollen with polydimethylsiloxane (PDMS). The PDMS fluid is not chemically bound to the crosslink network but is retained only by physical means, in the same way water is held within a sponge.
There is a wide range of polymeric materials available. Many of these are in current use as adhesives, encapsulants or as substrate for construction of medical devices, encapsulation or protection of electronic components in medical devices. The reliability and protection of electronics, along with joining and micro-packaging of materials used in microsystems, is one of the active areas of R&D in the medical device arena. The result of the research and interest has led to greater use of
adhesives and encapsulants in electrical and electronic components for a number of devices.
AUTOMATION
Joining product components with acrylic adhesives, particularly pressure-sensitive ones, can be automated using an array of equipment and techniques. Approaches include robotic material handling, in-line or automated surface preparation of adherends, automated adhesive dispensing, curing and component assembly.
Whether a joint is being created manually or by an automated process, selection and application of an appropriate surface treatment is important for successful service performance. Good surface preparation enables the adhesive to wet the surfaces to be bonded and improves long-term durability of the bonded joints.
THE RIGHT TREATMENT
While surface treatment removes weak boundary layers, it can also affect physical or chemical characteristics of the joint surfaces, enabling mechanical interlocking or chemical interaction, or some combination of both. Inadequate or unsuitable surface treatment is one of the most common causes of premature degradation and failure.
In most applications simple degreasing and abrasion is usually sufficient to provide good adhesion. However, many polymers with low surface energy and weak bondability, such as polyolefins, often require a more specialised treatment in order to provide better adhesion and joint durability. Some adhesion promoters can also enhance bondability of certain polymers.
Once preparation has been carried out satisfactorily, adhesives should be applied before the adherend’s surface is contaminated and before it loses its surface reactivity. If possible, manual mixing of the two part adhesive system should be avoided as this might introduce voids and bubbles. It can also lead to an inconsistent and incomplete mix. Pre-packaged cartridges for use with hand-held dispensing guns for single or multi-part adhesives are recommended and give more reliable results.
Adhesives can be dispensed by pumping in a number of ways. The method chosen will depend on whether a one or two-part adhesive is being dispensed. One-part adhesives are dispensed using direct metering extrusion pumps. An electric motor pushes a follower plate into a drum of adhesive, which is extruded through a hose to the dispensing valve. This technique has been used for medium- to high-volume production rates. In semi-automated applications intended for medium- to high-volume assembly operations, two-part adhesives are usually dispensed by volumetric pumps.
However, one of the most attractive methods of precision dispensation of polymeric resins and particle filled fluids is microjet/printing technology. This technology is often based on piezoelectric demand-mode ink-jet printing technology. The method is finding favour as a way of dispensing adhesives for some new micro and optoelectronic component assembly applications, as well as in medical device manufacturing.
CURING TECHNIQUES
Curing of adhesives can be completed in a variety of ways. Polymeric adhesives or encapsulants can be cured using moisture or catalysts in the presence, or in the absence, of air. This can be carried out at room temperature, at an elevated temperature or photochemically using a source of radiated energy, such as UV or visible light, electron beam or lasers. In heat-activated processes the curing can be achieved using a variety of sources.
Many materials, including acrylated resins, can be cured using radiation energy. Radiation curable adhesives or encapsulants usually consist of low or medium molecular weight resins (called oligomers), mono or multifunctional monomers, additives, pigments, photoinitiators or photosensitisers. A typical UV energy of 80–120mW/cm² produced from a UV source (wavelength 300–400nm) is usually sufficient to cure an adhesive within 10–60s.
An alternative technique is to cure using visible light (wavelength 470nm). Many dentists already use this technique for curing of dental materials. Radiation curing adhesives have also been used for joining clear polymers in medical devices. Both UV and visible light curing can be achieved using light boxes or focused beams and light guides. In some cases heat is also employed to encourage the curing process, for completion of cure, or to cure areas that cannot be reached by the radiation energy.
Adhesive techniques are used in a number of applications:
- Catheters. A silver-loaded electrically conductive adhesive joins a piezo-electric transducer (PZT) ring to a tungsten carbide (WC) tube as two components of a cardiac catheter tip. The catheter tip functions as part of an ultrasound-imaging device for quantitative and diagnostic analysis of coronary arteries. UV curing acrylics adhesives are used for joining balloons onto PVC, urethane and multi-lumen polymer-based tubes for balloon catheters.
- Needles. Lancets, syringes, injectors, hypodermics, blood collection sets and introducer catheters are assembled using acrylic-based adhesives. The polypropylene mouldings of a drug administration gun are bonded together using a cyanoacrylate adhesive.
- Polycarbonate devices. Acrylic-based adhesives are used in bonding polycarbonate medical devices including filters, blood pressure transducers, arteriograph manifolds, carditomy reservoirs and blood oxygenators. Epoxies are also used for joining filter components.
- Masks. UV curing acrylic adhesives are employed for bonding cushion (flexible PVC) to nose (rigid PVC) in anaesthesia and face masks.
- Tubesets. Blood and drug delivery sets, suction tubes and IV tubes, are assembled using acrylic-based adhesives.
APPLICATIONS
Using adhesives as a joining method enables the manufacture of many products that could not be made in other ways. Advances in the adhesives and adhesion science and technology, particularly the emergence of new generation of polymeric adhesives with unique properties, means the range of medical and electronic products for which adhesives are used as bonding agents has grown significantly. Adhesives can be used successfully in joining and assembly of a new generation of medical devices, providing that proper procedures are followed in selecting the most suitable adhesives, design of the joint, mixing. dispensation and curing.
Although there are many commercially available medical grade adhesives, their use for new applications requires detailed investigation. As well as considering the initial joint strength, its durability in the operating environment is an important consideration. This involves the temperature range, stresses and exposure to fluids and sterilisation processes that the joint will be expected to undergo both in processing and service. Accelerated ageing tests provide realistic durability data on which decisions can be made. Interpretation of ageing data and lifetime prediction of bonded joints is essential in the assessment of device performance.
The emergence of new types of adhesives, as well as further development of precision dispensing and rapid curing technologies, offers exciting and commercially attractive opportunities for joining medical devices. As the demands place on medical products grow, so adhesive technology will continue to develop in performance and complexity. Keeping abreast of this technology will ensure that manufacturers, like their products, will meet the demands placed on them.