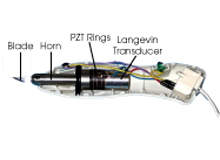
Certain materials produce electric charges on their surfaces as a consequence of applying mechanical stress. The induced charges are proportional to the mechanical stress. This is called the direct piezoelectric effect and was discovered in quartz by Piere and Jacques Curie in 1880. Conversely, materials showing this phenomenon also have a geometric strain proportional to an applied electric field – the converse piezoelectric effect.
The most popular piezoelectric materials are lead zirconate-titanate (PZT)-based ceramics and relaxor-lead titanate solid solution single crystals, in addition to quartz. Piezoelectricity is extensively utilised in the fabrication of various sensor and actuator devices.
ULTRASONIC IMAGING
Ultrasonic waves (in the human-inaudible range higher than 20kHz) made from piezoelectric ceramics are now used in various fields. A liquid medium such as water in the human body can be used for sound energy transfer. Ultrasonic scanning detectors are useful in medical electronics for clinical applications ranging from diagnosis to therapy and surgery.
One such application is based on a low-power ultrasonic echo field with a short wave. Ultrasonic transducers convert electrical energy into mechanical form when generating an acoustic pulse. The transmitted waves propagate from the skin into the body and echoes are generated which travel back to be received by the same transducer as an electrical signal. These echoes vary in intensity according to the type of tissue or body structure (due to different density and elasticity), thereby creating images.
It is possible to recognise anatomical structures in an ultrasonic image since the organ boundaries and fluid-to-tissue interfaces are easily discerned. The ultrasonic imaging process can also be done in real time. This means we can follow rapidly moving structures such as the heart without motion distortion.
How well do you really know your competitors?
Access the most comprehensive Company Profiles on the market, powered by GlobalData. Save hours of research. Gain competitive edge.
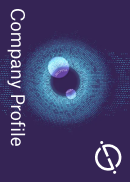
Thank you!
Your download email will arrive shortly
Not ready to buy yet? Download a free sample
We are confident about the unique quality of our Company Profiles. However, we want you to make the most beneficial decision for your business, so we offer a free sample that you can download by submitting the below form
By GlobalDataIn addition, ultrasound is one of the safest diagnostic imaging techniques. It does not use ionising radiation such as X-rays and thus is routinely used for foetal and obstetrical imaging. Useful areas for ultrasonic imaging include cardiac structures, the vascular system, foetuses and abdominal organs such as liver and kidney.
There are various types of transducers used in ultrasonic imaging. Mechanical sector transducers consist of single, relatively large resonators and can provide images by mechanical scanning such as wobbling. Multiple element array transducers permit discrete elements to be individually accessed by the imaging system and enable electronic focusing in the scanning plane to various adjustable penetration depths through the use of phase delays.
A linear array is a collection of elements arranged in one direction, producing a rectangular display (see Figure 1). The elements of these linear-type array transducers are excited sequentially group by group with the sweep of the beam in one direction. These linear array transducers are used for radiological and obstetrical examinations.
The most recent development trend is an acoustic microscope that uses a high frequency (higher than 1GHz) to observe the biological cells coupled with endoscope/catheter technologies, which helps with finding a cell disease embryo.
ULTRASONIC THERAPY
When we increase the ultrasonic power lever higher than 1W/cm², ultrasonic wave radiation can increase the tissue temperature through the elastic non-linearity of tissues. Hyperthermic therapy for prostate cancer treatment is one of the most famous applications.
Using a high-frequency wave (above 1MHz), and focusing the ultrasonic beam at a certain point in a body, only the cancer portion is increased in temperature (42ºC or higher for 30–60 minutes), which will eliminate the cancer. Bleeding inside the organ can also be stopped by using an acoustic pulse shot from the skin without significant surgery. By increasing the power intensity further, it is possible to destroy a kidney stone.
PIEZOELECTRIC ACTUATORS
Piezoelectric ultrasonic knives have already been commercialised (see Figure 2). By superposing high-frequency longitudinal vibrations on a sharp cutter blade, thin sheets of paper or even plastic can be easily cut just by touching the blade. When this is used for a surgery knife, the cutting sharpness can be maintained for a long period because of continuous removal of the fat adhesion – the major reason why surgeons need to exchange knives frequently during theatre.
In addition, the ultrasonic cutter can stop bleeding, since the ultrasonic vibration generates friction heat between the blade and the tissue, accelerating blood clot generation. Multiple PZT rings are sandwiched by metal (nickel) rods with a bolt (bolt-clamped Langevin transducer), which generates longitudinal µm-level vibration amplitude at the resonant frequency (20–50kHz). Using a horn, this displacement is amplified by 20–30 times, and finally 150µm displacement is excited at the blade tip. This large vibration amplitude is essential to dissolving tissue and generating blood clots.
Ultrasound mediated transdermal drug delivery offers promising potential for non-invasive drug administration. When an ultrasonic transducer is placed on the skin’s surface, the vibration makes the skin more permeable, enabling the drug to be delivered to the blood system. Additionally, the transdermal extraction of interstitial fluid by low-frequency ultrasound (20kHz) offers a non-invasive method of obtaining a fluid sample for at-home monitoring.
Researchers have successfully used acoustic energy for glucose monitoring and insulin delivery using predominantly commercial sonicators. Using the thin compact ‘cymbal’ piezo-transducer design (named due to its shape), researchers at Pennsylvania State University demonstrated non-invasive insulin delivery for pronounced glucose reduction in animals.
Both the interstitial fluid glucose monitoring and ultrasonic insulin delivery techniques have been proven effective by others, but the cymbal technology provides the opportunity to reduce the size of the required hardware dramatically, making possible a matchbook-sized system that can be conveniently worn by the patient continuously.
Ultrasonic motors (USMs) using a piezoelectric resonant vibration are highly focused because of their superior performance:
- One-tenth smaller in size and weight than electromagnetic (EM) motors with similar power level
- High torque and low speed drive characteristics, without using gear mechanisms
- Ten times higher efficiency than EM motors
- No electromagnetic interference
- Quiet operation due to a high-frequency (over 20kHz) operation frequency
In USMs, linear motion is obtained from the elliptical vibration through frictional force. The motor basically consists of a high-frequency power supply, a vibrator and a slider. Further, the vibrator is composed of a piezoelectric driving component and an elastic vibratory part, and the slider is composed of an elastic moving part and a friction coat.
ULTRASONIC MOTORS
Ultrasonic motors are classified into two types: a standing-wave type and a travelling-wave type. The large travelling-wave motors (60mm diameter), commercialised by the Japanese firms Shinsei and Fukoku, are used for high torque and quiet motors for magnetic resonance imaging (MRI) equipment, primarily due to the lack of generation of the magnetic field.
A micro standing-wave motor called a metal tube type with a thin and long configuration has been developed by the Penn State researchers in collaboration with Micromechatronics Inc, also in Pennsylvania. A simple metal hollow cylinder, bonded with two standard PZT rectangular plates uniformly poled, is used as a stator. When one of the PZT plates is driven, a bending vibration is excited.
However, because of an asymmetrical structure, another hybridised bending mode is excited with some phase lag, leading to an elliptical locus in a clockwise direction. The motion is analogous to a ‘dish-spinning’ performance, with two rotors made to contact the wobbling tube ends to achieve rotation.
A speed of 2000rpm and torque of 0.3mNm were obtained at 60V for both directions for a motor with a diameter of 1.5mm and a length of 4mm (see Figure 3). This extremely high torque:size ratio provides various applications in minimal invasive micro surgery areas, coupled with catheters and endoscopes.
Finally, a new micro robot or stage application to artificial fertilisation should be mentioned. The Japanese company Applied Micro Systems has developed a micro robot composed of four piezoelectric multi-layer actuators and four electromagnets. The moving principle is basically an ‘inchworm’ type on a steel bench with clamping function by the electromagnets and translation by the ML actuators. This inchworm micro robot can make rotation, translation to any direction and circular orbit motion with 30nm position resolution.
The company has demonstrated a micro-manipulation capability by coupling a piezoelectric ball rotor and the micro robot unit. A fish egg (100µm in diameter) was handled by a thin glass tube nozzle, and another needle tube for sperm insertion was inserted smoothly without deforming the egg shape, mainly due to the high-frequency (1kHz) vibration superposition to the needle motion. This high-frequency vibration cannot be realised using a conventional oil-hydraulic actuator, which increases the number of eggs damaged during the operation.