
Over the last 20 years, the drive for miniaturisation of devices in a range of markets has pushed the demand for processes that can produce high-precision, intricate components in a cost-effective manner for volume production. For medical, mechanical and optical components, an obvious candidate to satisfy the need is injection moulding, where advances in processing hardware have improved machine accuracy and control to allow production of components with high-precision geometric features.
These advances are helping manufacturers to produce dedicated micromoulding platforms which incorporate material plasticising, metering and injection systems specifically designed to meet the demanding requirements for a successful micromoulding process.
Micromoulded products can be defined as components with a total mass of less than 0.1g (MEMS components, medical implant devices) or components with larger overall dimensions, but containing features in the micro-nano scale range (DVD, lab-on-a-chip, microlens arrays).
The technology is rapidly maturing and a range of devices exist which have successfully harnessed these new processes to produce components from a range of materials, including engineering thermoplastics, biosorbable polymers, optical polymers and metal and ceramic products (using powder injection moulding techniques).
Significant challenges still exist to further refine the technologies as demands from end users require ever-decreasing feature sizes, use of exotic materials, increased functionality and tighter quality assurance. These challenges can be categorised into three key areas: tooling, processing and metrology.
Tooling
How well do you really know your competitors?
Access the most comprehensive Company Profiles on the market, powered by GlobalData. Save hours of research. Gain competitive edge.
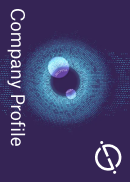
Thank you!
Your download email will arrive shortly
Not ready to buy yet? Download a free sample
We are confident about the unique quality of our Company Profiles. However, we want you to make the most beneficial decision for your business, so we offer a free sample that you can download by submitting the below form
By GlobalDataTo achieve cavity forms that have features and tolerances to meet the specifications of the end product, toolmakers are required to adopt new technologies. Many advances have been made in this area over recent years and, in order of characteristic feature sizes, include:
Micromachining. Micromachining is an evolution of conventional machining technology. By refining the process through manufacture of smaller, harder cutters and drills (down to 50μm in some cases), operating at extremely high speeds and held within a vibration-free apparatus, it is possible to machine materials to extremely high tolerances. The process requires tight control of the surrounding environment, because even a slight rise in ambient temperature can cause a loss of dimensional control due to material expansion. Feature sizes are limited by the physical size of the tool and the metallurgical properties of the steel workpiece should be well controlled.
Micro-electro discharge machining. The scaled-down cousin of EDM uses a high-voltage electrode in a dielectric medium to cause arcing and consequent vaporisation and removal of surface material. μEDM typically offers similar sized features as micromachining processes, but usually results in better surface finishes due to the lack of machining marks. This technique is also ideal for machining hard materials which would pose problems using micromachining methods. It does require a conductive workpiece to operate, so although useful for tool steels, insulators such as ceramics and engineering polymers pose problems.
Laser machining. Laser ablation occurs when a high-power pulsed laser is focused through a lens at a single point on the surface of a target material, raising the material's temperature to 2,000–3,000°C and causing it to vaporise. Areas are machined by moving the laser in a raster fashion across the target using an optical system, or by moving the material on an x-y-z stage. Almost any material can be machined with high precision. However, thermal shocks within the workpiece and recasting of the vaporised material can produce an undesirable surface finish for some applications.
Lithography. Photolithography techniques use structured radiation of photons (UV or X-ray) to produce a detailed mask used to obscure regions of a material then eroded using ion etching. Fine features (<1μm) can be patterned over large areas. Structures are usually soft (polymers) or brittle (silicon). A common route for production of cavities involves creating an inverse form, then electroplating with nickel. Although nickel does not possess the mechanical properties of tool steels, it has been shown to be robust enough for small to medium-scale micromoulding production runs.
'Direct write' techniques. Electron beam and focused ion beams can be manipulated to directly machine sub-micro features into a metal surface. These techniques offer unrivalled accuracy, with features in the sub-50nm range possible. But writing times can be prohibitive (FIB systems can take up to a year to remove 1mm³ of material) and have an associated high cost. Typically, a tooling solution for a micromoulded device will use a combination of these techniques to create the required cavity form.
Processing
It would be easy to assume that once the cavity form has been produced, moulding the device would be fairly straightforward. Unfortunately, there is still much to understand about the behaviour of the feedstock materials in the process.
Polymers are complex materials composed of long, entangled molecules, giving them viscoelastic properties and timescales which define how they behave when subjected to temperature and pressure. Stresses take time to relax and the environment upstream of the mould cavity can influence material behaviour. Semi-crystalline polymers can form complex morphological structures of crystalline and amorphous regions during cooling, which are dependent on the stress within the material and thermal history, and will influence the properties of the final product.
Research activity worldwide is aiming to push forward understanding of the relationship between molecular architecture, processing and product properties in polymer processes, but the challenge for understanding this is further compounded in micromoulding by the process environment.
High injection velocities combined with small cavity sizes ensure that wall shear rates are orders of magnitude higher than those encountered in conventional moulding processes. The higher surface area to volume ratio of the components also causes the products to cool in a few milliseconds, resulting in high temperature gradients. This makes it difficult to determine the limits of the process.
A key goal in this area of micromoulding is to develop robust mathematical models which describe how a comprehensive range of polymers behave when subjected to these environments. These models will allow development of simulation software to ensure that a component is viable without expensive experimental trials. The know-how can also be used by product designers and machine builders to optimise a new generation of micromoulding processes.
Metrology
The typical feature size of micromouldings poses problems when considering the use of conventional testing methods and alternatives must be sought. Moulders will typically visualise products using microscopes when setting up processes, but accurate quantification of product quality is performed using white light interferometry (WLI), coordinate measuring machines (CMM) or atomic force microscopy (AFM). While these techniques provide high-quality data, they can take hours to perform measurements, so only a small sample set from a production run can be assessed.
Many commercial injection moulding processes already employ machine vision systems for in-process quality assessment. A number of cameras linked to pattern recognition software allow evaluation of critical dimensions and feature sizes. However, true micromoulded features with dimensions smaller than 1mm require evaluation using microscope lenses posing problems when attempting to employ them in machine vision applications. The height of upstanding features from a moulding surface cannot be verified using a single two-dimensional image.
Future advances in this area are investigating ways to integrate new measurement systems. One such technology being investigated is an in-process, high-speed three-dimensional measurement system for evaluation of each component manufactured during the process.
This system uses a combination of computer-controlled microscope objectives and WLI to provide accurate characterisation of features with rough or smooth surfaces. A high-speed camera combined with quad-core Intel PC is used with custom software to provide quantified quality assessment within three seconds, short enough to have no impact on the process cycle time.
Micromoulding investigated
Work to develop process understanding has been performed at the University of Bradford since 2001, on an academic research and industrial contract R&D basis. The Centre of Micro and Nano Moulding provides tools to assess material behaviour, accurately characterise the moulding environment and measure the final product properties. Active research areas include:
High strain rate rheology. The flow behaviour of a range of polymer materials is assessed using a modified high speed injection moulding machine. This can provide shear and extensional viscosities plus adiabatic and frictional heating measurements which helps us to understand material behaviour in micromoulding processes.
Novel sensor design and integration. A range of commercial sensors (pressure, displacement, flow) have been installed on micromoulding hardware which, when combined with in-house developed software, allows capture of changes within each process measurement on a per cycle basis, or for stability monitoring of a commercial production run. Novel sensor designs have also been manufactured and tested to allow ultrasonic characterisation of products during cooling and rapid response temperature measurements.
Flow visualisation. One of the most powerful techniques available for studying a moulding process is to image the cavity filling directly. This is not as easy as it sounds for a micromoulding process for a couple or reasons. Firstly, the short filling times <10ms requires the use of high-speed video cameras with short exposure times. Secondly, the physical size of the moulds and the nature of the environment (high pressures, temperatures) cause difficulties when mounting transparent windows, as they can have a tendency to shatter. These problems have been overcome through the use of a high speed camera based system with high intensity illumination and the use of sapphire windows in the fixed mould half. Data generated with this system include:
- flow front tracking
- shrinkage measurements
- stress-induced birefringence.
Thermal measurements. The rapid temperature gradients inherent in micromoulding negate the use of thermocouple measurements due to their relatively slow response times. A fully calibrated system has been developed which captures data along a line across the moulding at a rate of 2,500 lines per second, which is adequate for study of the cooling behaviour of micromouldings.
Successful micromoulding
The complementary technologies required for a successful micromoulding process are advancing rapidly, which is benefiting end users in the medical device market sector through the realisation of ever more complex micro devices using a range of materials. There is still much work to be done to further understand the physical limits of what is achievable, but a combination of high-quality academic research combined with effective knowledge transfer will ensure that this technology will
continue to advance, providing cost-effective solutions for devices that offer a better quality of life.