
Traditional packaging safeguards for sterilisation and physical protection of electrostatic discharge (ESD) sensitive medical devices must be supplemented with ESD control measures for internal, in-process and external packaging. In comparison to the defence and semiconductor sectors, medical device and pharmaceutical organisations are relative newcomers for implementing safeguards in the prevention of associated hazards due to electrostatic fields and discharges.
The risk to microprocessor-driven devices is well known as ESD issues that have not only been documented within ESD-protected environments, but also in retail or hospital environments. At this time, it appears that medical oriented ISO, ASTM and the FDA packaging protocols have not kept pace with ESD safeguard requirements for addressing microprocessor densification advancements. Thus, device manufacturers sacrifice ‘real estate’ for speed by driving down additional ESD protection responsibilities from R&D to manufacturing.
Microscopic ESD-sensitive circuit lines have replaced larger robust circuits to improve performance (speed). ESD-related issues have grown from approximately $500m in 1984 to over $40,000m annually. Adherence to ISO, ISTA and ASTM International Committee F02 Flexible Barrier Packaging requirements is critical for medical device packaging integrity.
Packaging engineers must, however, look outside the box in the establishment of ESD protective measures and standards for ESD protection.
To compound the problem, some medical device OEMs are outsourcing manufacturing to subcontractors or contract manufacturers (CMs), empowering CMs to monitor, assess and validate processes for ESD compliance. A laissez-faire management style does not work; if a company does not audit, then the organisation does not have much of an ESD programme.
Suspect counterfeiting awareness
How well do you really know your competitors?
Access the most comprehensive Company Profiles on the market, powered by GlobalData. Save hours of research. Gain competitive edge.
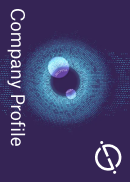
Thank you!
Your download email will arrive shortly
Not ready to buy yet? Download a free sample
We are confident about the unique quality of our Company Profiles. However, we want you to make the most beneficial decision for your business, so we offer a free sample that you can download by submitting the below form
By GlobalDataA FDA ISO 134585:2003 audit may uncover mislabelling issues with ESD-sensitive devices (components). From a sample lot of 100 ESD-sensitive components, 65 are labelled correctly while 35 are mislabelled. For instance, unknown to the component distributor, the 35 mislabelled devices are suspect counterfeit and incorporate a different identification process that is identified by a microscope. The critical action indicated (CAI) is now elevated to executive review (CAI-ER), for various reasons:
- Counterfeiting costs US businesses $200bn to $250bn annually
- Counterfeit merchandise is directly responsible for the loss of more than 750,000 American jobs
- Since 1982, the global trade in illegitimate goods has increased from $5.5bn to approximately $600bn annually
- US companies suffer $9bn in trade losses due to international copyright piracy
- Counterfeiting poses a threat to global health and safety
- Approximately 5–7% of the world trade is in counterfeit goods.
Packaging engineers must implement design measures and validation checks for protection against suspect counterfeiting. Even long-standing electronic distributors can have difficulty in distinguishing real from suspect counterfeited devices. In addition, the medical device packaging engineer must establish a formalised materials qualification process as traditional ESD protective materials are ‘knocked off’ most often without the end users or their supplier’s knowledge.
Obsolete parts are pulled from old board stock and scrapped ESD damaged parts. Inferior or defective components are relabelled and sold as new. These actions can pose real threats to human life for medical device, defence, automotive and space agencies. Even realistic fraudulent ESD & Chemical Test Reports are issued with full acceptance by the user.
Counterfeiting can lead to additional susceptibility for ESD events, contamination, corrosion and non-compliance with RoHS and recycling requirements. Counterfeit parts rarely include any ESD protection for superficial repair and poor ESD handling in the branding process with bogus information.
Testing for safety
It is essential to set up an incoming validation process that facilitates inspection of supplier shipments for ESD-sensitive devices. In addition, microscope inspection techniques are utilised for acceptance or for future quarantine. Static dissipative moisture barrier bag outer packaging protection to shield ESD-sensitive devices such as pacemakers from outside influences must be implemented after validation by in-house or third-party testing per ANSI/ESD STM11.31-2006. Reliance on supplier specification sheets can prove costly.
Circuit card removal from an insulative vacuum-formed tray during manufacturing can be compromised by an field-induced model ESD event. Often, an ‘out of spec’ tray that was claimed by the supplier to be ‘static safe’ or antistatic was not tested for ESD integrity. A pacemaker circuit card when placed inside a static dissipative vacuum-formed tray must employ a static shielding moisture barrier bag for transport outside an ESD safe area.
If an insulative tray is used and a pacemaker circuit card is removed by grounded person using stainless steel tweezers, a discharge can take place. The author has recorded 1,250 volt discharges when in proximity to an ESD event antenna. This is representative of what could happen during the automated pick and place process or when a grounded individual touches the circuit card with stainless steel tweezers. ESD packaging must be tested by the use of sound qualification procedures. It must be considered that topically treated antistatic vacuum formed trays have a limited shelf-life. Likewise, IPA or deionised water rinsing can remove topical surfactants or diminish performance. In addition, amine transfer has accounted for soldering issues, polycarbonate incompatibility and other contamination issues in ISO Class 7 and below environments.
Surface resistance data from Dr Marv Havens’ ‘The Chemistry of Dissipative Plastics’ established that topical antistats can become insulative on the fourteenth day. This calculates to a life expectancy or shelf life of about 238 days (approximately seven months).
Surface resistance vs relative humidity
Often the surface resistance of antistatic materials rises and falls when relative humidity fluctuates. Per ANSI/ESD S541-2008, 1.0 x 1011 ohms is the standard cutoff for retention of static dissipative properties. In practice, however, a lower cut-off is often desired for packaging materials because dry air may be encountered in shipping and handling.
In cold and dry climactic conditions, relative humidity can reach 4–5% or below. The ESDA standard for surface resistance (ANSI/ESD STM11.11-2006) requires the evaluation of planar static dissipative materials at 12% +/-3% RH @23°C +/-3°C after 48–72 hours of preconditioning.
Resistance testing constitutes one phase of required testing. Electrostatic decay measurements represent another validation process. Often, a vacuum-formed tray is used, so it is important that during in-process travel, ESD packaging will dissipate and prevent charge build-up. Mil-STD-3010A-2005 requires decay of +/-5,000v to +/-50v or +/-1,000v to +/-100v in < 2.0 seconds.
Hospital personnel walking on charge-generating floors can create electrostatic fields that could compromise ESD-sensitive devices from discharges. Precautions in handling ESD-sensitive microprocessors in a non-ESD protective environment must be facilitated with packaging that affords attenuation (shielding) from field-induced model discharges.
Following in the footsteps of a Norwegian facility, a Swedish hospital may ban the popular Crocs clogs because of concern that the plastic shoes generate static electricity that interferes with medical equipment. Officials at Blekinge Hospital suspect that the slip-on shoes, which are known as Foppatoffels in Sweden, may have been responsible for at least three device malfunctions this year, including one instance in which respiratory equipment ‘shut off and on for no apparent reason’.
Hospital officials believe that Crocs’ plastic material acts as an insulator for static electricity, resulting in the shoes’ becoming charged with as much as 25,000v. While the incidents have not resulted in any adverse events, hospital officials say that the shoes’ static cling is likely to have been “a problem for many years”. (Source: Nordstrom, AP/Newark Star-Ledger, 20/04; The Local, 18/04.)
Static shielding
The American Heart Association (AHA) lists pacemaker pulse generator issues found with home appliances, cell phones, heavy equipment motors and much more. A medical device packaging engineering must validate shielding performance in the packaging of pacemakers for transportation and use in a hospital environment. As with medical devices, return material authorisations (RMAs) cannot be issued for space bound satellites.
ANSI/ESD STM11.31-2006 evaluates the shielding performance of static shielding bags. A 1KV discharge to the outer package is conducted; the fixture then measures the current across a resistor connected to the fixture’s upper and lower sensing plates to determine the energy (nJ) inside the bag.
Despite a moisture barrier bag’s favourable shielding performance, if the metallised bag fails the overall ESD evaluation due to unfavourable surface resistance, it constitutes a failure. An insulative bag may provide adequate attenuation from an ESD event, but could be responsible for inducing a charge on to an electronic-sensitive device upon removal from the package.
It is well documented that relative humidity during air flights can drop below 10% RH. Packaging must not only protect the medical device from physical damage, but also provide protection against high-voltage discharges which can arise from metal-to-metal contact, transport and mishandling in a hospital environment by ungrounded medical personnel.
Research material has been referenced in this text. For full details please contact the editor, andrewtunnicliffe@spgmedia.com.