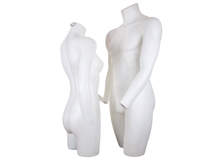
The growing demands of the medical and dental sectors for complex parts and high-performance materials are driving forces for the development of new fabrication techniques. High mechanical strength, tailored surface roughness, controlled porosity, resistance to strong sterilisation procedures, biocompatibility and durability are among the exigent requirements for a wide range of applications.
Powder injection moulding (PIM) is a well-established technology that has shown an exceptional growth in many fields including the automotive, watch, casting, aerospace, electronics, electric components and defence industries. In the dental and medical sectors, since the first success in the late 1980s with orthodontics brackets and surgical tools in the mid-1990s, the number of applications in devices and implants grew to reach $100m in annual sales by 2005. This success is based on the capability of PIM to produce large series of net-shape complex parts, with high repeatability and tight tolerances.
However, the full potential of PIM for medical applications is far from being exploited. This is related to the limited availability of powders of the required composition and purity, the confidential character of early proprietary technologies, the need of developing appropriate equipment, the lack of understanding the basic principles of the process, and the natural incubation time needed for a new technology to become known and accepted by producers and end users.
The situation is rapidly changing, not only because of the progress accomplished in research, base materials and process equipment, but also because the downturn in economy puts pressure on producers to reduce costs and encourage the development of innovative solutions.
Diverse properties
Injection moulding of plastics has been used for decades to produce a high diversity of everyday-life or high-tech products. Great freedom in shape, cost-effective processing and high-volume production are some of the characteristics of this technology. However, some inherent properties of plastics such as low mechanical strength, low temperature resistance and poor wear resistance are limiting drawbacks. Metals and ceramics exhibit higher mechanical performance, higher thermal resistance, electric and magnetic properties and other improved characteristics compared with polymers, but can they be processed in a similar way? It is a dream that has now become an industrial reality.
How well do you really know your competitors?
Access the most comprehensive Company Profiles on the market, powered by GlobalData. Save hours of research. Gain competitive edge.
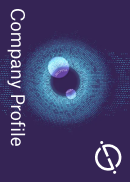
Thank you!
Your download email will arrive shortly
Not ready to buy yet? Download a free sample
We are confident about the unique quality of our Company Profiles. However, we want you to make the most beneficial decision for your business, so we offer a free sample that you can download by submitting the below form
By GlobalDataPIM combines the flexibility and design of plastic injection moulding with the excellent properties of metals and ceramics produced from powders, which are shaped and subsequently heated to create a coherent object. This technology, which includes metal injection moulding (MIM) and ceramic injection moulding (CIM), is essentially suited for producing medium to high volumes of complex parts (5,000–2,000,000 units annually). Net-shape manufacturing by PIM of difficult-to-machine components can result in cost savings ranging from 30 to 90%.
There seems to be some ‘magic’ in PIM: how do the parts still remain intact after binder removal without collapsing? How can the shape be preserved after high temperature sintering and shrinkage? Among the keys to succeed in producing a complex part are the use of fine spherical powders for good flowability and packing into the mould, an overlap between the end of debinding and the beginning of sintering steps, and the close control of temperature and atmosphere during thermal processing. The respect of PIM design rules, similar to those of plastic injection moulding, is also essential.
In this way as-sintered dimension tolerances of ±0.3% and average surface roughness of 0.8µm for parts with typical maximum dimensions of 25–35mm can be obtained. The final properties of PIM are excellent and generally match those attained with alternative shaping routes. Post-sintering thermal and surface treatments can even improve properties, which can exceed in some cases those of castings, wrought alloys or conventional ceramics.
The manufacturing of a part by PIM usually consists of four steps: feedstock preparation, injection moulding, debinding and sintering:
Feedstock preparation is made in appropriate mixers, with typical volume fractions of about 60% powder and 40% polymer binder, the goal being to create a homogeneous mass where each grain of powder is fully surrounded by polymer.
Injection moulding is accomplished with the same kind of machines used in the plastic industry. First, feedstock pellets are heated and plasticised into a cylinder chamber using a reciprocating screw. Then, the same screw is used as a piston to inject the feedstock into a split mould. After cooling and solidification, the mould is opened and a ‘green part’ ejected.
Debinding is the operation by which the majority of the polymeric binder is removed. It can be accomplished in several ways: thermal debinding, solvent debinding or catalytic debinding. This is a critical step which needs careful control to avoid breakage of the resulting ‘brown part’, the constituent particles of which are weakly joined by a thin film of polymer, Van der Waals forces and early local welding between particles.
Sintering is the final step in which the powder grains are joined by a diffusion process, which creates sinter bonds between particles. The porosity progressively reduces and densities of more than 95% of the theoretical density are generally achieved. The ‘sintered part’ exhibits a shrinkage of about 10–15% compared with the green part.
Working with metals and ceramics
Most PIM medical and dental applications are based on 17-4PH and 316L stainless steels. 17-4PH is a martensitic stainless steel of medium corrosion resistance used when high strength and hardness are required. This steel is precipitation hardenable and a range of properties can be achieved with different heat treatments. 316L is an austenitic stainless steel, nonmagnetic, with excellent corrosion resistance and good combination of strength and ductility. Both steels are used in a number of products such as orthodontic brackets, surgical instruments and endoscopy and biopsy devices. Other stainless steels including 304L, 420 and 440C are also used. Nickel-free stainless steel powder grades have been developed to avoid sensitisation, but their application is still limited.
Technical ceramics such as alumina, zirconia, zirconia toughened alumina and yttria-stabilised zirconia can be processed by CIM and are used in some emerging dental applications (translucent orthodontic brackets, crowns, dental inlays) and medical devices (components for pacemakers, implantable heart pumps). Biocompatibility, compression strength and wear resistance are among the outstanding properties of these materials, which are also entering the market of implants.
Magnets are another interesting potential market. Examples of PIM applications are soft magnetic materials based on iron-silicon or iron-nickel alloys, and permanent magnets of the neodymium-iron-boron type. Among the possible applications are NMR/MRI scanners, extending prosthesis, wound closures, stomach seals, ferromagnetic probes, cell separators, magneto-motive artificial hearts, magnetic removers in ophthalmology or gastroenterology, microactuators and orthodontics.
Powder injection moulding is particularly suitable for producing medical implants. However, these components are subjected to more rigorous standards than medical instruments. This is because of a more severe in vivo environment, higher mechanical exigencies and the need to preserve patient safety by limiting replacement operations. Implants can be dense or porous, and can be designed for high or medium-strength applications, for permanent or temporary use.
Cobalt-chromium-molybdenum alloys are used in orthopaedic implants because of their high strength, fatigue and corrosion resistance, non-magnetic behaviour and biocompatibility. Applications include prosthetic replacements of hips, knees, elbows, shoulders, ankles and fingers; bone plates; and screws and support structures for heart valves. MIM alloys have shown mechanical properties higher than the requirements for the equivalent cast and wrought alloys, and can become a valuable option for the production of implants.
Titanium and titanium alloys are excellent materials for biomedical applications because of their high strength, lightweight, good corrosion resistance, biocompatible character and good results with magnetic resonance imaging. Fabrication of titanium implants is a costly multi-step process, which includes vacuum arc melting, hot rolling, scale removal, vacuum annealing, machining and surface treatment, and has therefore attracted great attention to MIM.
However, titanium-based materials are quite sensitive to oxygen, nitrogen and carbon interstitial impurities, which are detrimental for final properties. These impurities can be present in the base powders, or result from improper process control during debinding and sintering. Only in recent years has the availability of high-quality base powders allowed substantial progress in the production of titanium-based materials and prototypes for different applications.
Shape memory materials have commercial applications based on either shape memory behaviour (blood filters, cardiac stents, staples for osteosynthesis) or on superelasticity (catheters, vascular stents, chirurgical instruments, spectacle frames, rotary files for dentistry, orthodontic archwires). Nickel-titanium shape memory parts are produced by casting, hot rolling, hot extrusion, drawing, hot forming of wires on a shaping fixture, spark machining or laser cutting. Wide applications of these materials need efficient manufacturing techniques, such as PIM net-shape solutions.
At the University of Applied Sciences Western Switzerland, titanium-aluminium-vanadium alloys have been injection moulded using feedstock prepared from prealloyed powders and a multi-component binder composed of polyethylene, paraffin wax and stearic acid. A two-step debinding method has been used, in which firstly the paraffin and stearic acid are dissolved in a heptane bath, and secondly the polyethylene is removed by thermal treatment. Special care in powder selection, handling, feedstock preparation and heat treatment atmospheres have allowed low interstitial contents below the acceptable limits for the material standard grade to be obtained.
Ti6Al4V injection-moulded parts show good mechanical properties, good shape preservation and reproducibility. For example, parts with porosity of about 8% exhibit tensile strength of up to 780MPa and 9% plastic strain. The same binder system has been used to produce nickel-titanium materials from elemental nickel and titanium hydride powders, which are an interesting option because they are finer and less reactive than pure titanium powders. After solvent debinding, thermal debinding, dehydrogenation and sintering were performed in a single-step heat treatment. Shape memory recoverable strain of about 4% under 100MPa applied stress has been obtained.
Further challenges
Despite many MIM materials satisfying the requirements for strength level and plastic deformation, fatigue and corrosion resistance remain challenges to overcome for some specific applications. This has been attributed to the presence of pores, which are usually present after sintering. Appropriate heat treatments and reduction of porosity by hot isostatic pressing are among the secondary operations that can improve the performance of a MIM implant. Surface finishing is also essential.
Depending on application, smooth or rough surfaces can be required either for ease of removal and least traumatic explantation, or to encourage osseointegration and better anchoring of long-term implants. Modifications of the base powder compositions also need to be considered, because in many cases they are just copies of standard material formulations, without considering the specificity of the sintering process.
According to recent surveys, 38% of North American MIM sales are for medical applications, with 2% for dental applications. Ceramic injection moulding is not yet practiced as broadly as MIM. In Japan, about 12% of MIM sales are in the medical sector. In Europe, where the MIM market has been traditionally dominated by the automotive sector, the sales values are less in proportion, but the economic conjuncture and the technology progress suggest that important changes could occur.
Among the recent advances, the production of small implant prototypes and microactuators by micro-PIM of fine powders deserves particular attention. Dental and medical applications of powder injection moulding will certainly see strong growth in the coming years.