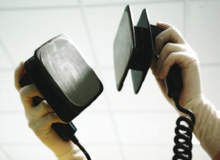
Before the 20th century, standards for electricity simply did not exist. However, in the 1900s, engineers began to see the need for terminology, testing and safety procedures and specifications that could be agreed on at international level. As a result, the International Electrotechnical Commission (IEC) was officially founded in London in June 1906. Lord Kelvin, who had achieved fame by laying the first commercial telegraph cable across the Atlantic Ocean, was named president.
Within a few years, the IEC had issued a first list of terms and definitions covering electrical machinery and apparatus, including letter symbols for quantities and signs for the names of units, and a standard for the resistance of copper. Definitions of hydraulic turbines and definitions and recommendations for rotating machines and transformers were also issued.
By the 1910s, access to electrical power had become more generally available and the world of radio, or ‘wireless telegraphy’ as it was known, had taken on new dimensions. New concerns about radiation led to a move to standardise the measuring of hazards.
The first efforts of engineers to standardise electrical equipment have paved the way for generations. Manufacturers still recognise that standardised production and a simplified design not only reduce costs for the consumer, but improve competition and provide recognised guarantees which remove the need for repeated and costly national testing.
Today, the measurement of hazards through standardised risk management is very much at the forefront of any competitive approach to the manufacturing and marketing of medical devices, particularly in the light of product liability protection.
NEW REPORTING STANDARDS
How well do you really know your competitors?
Access the most comprehensive Company Profiles on the market, powered by GlobalData. Save hours of research. Gain competitive edge.
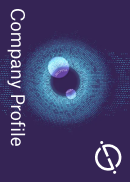
Thank you!
Your download email will arrive shortly
Not ready to buy yet? Download a free sample
We are confident about the unique quality of our Company Profiles. However, we want you to make the most beneficial decision for your business, so we offer a free sample that you can download by submitting the below form
By GlobalDataThe 1960s brought forth a new era of standardisation. Technical Committee 62 (TC 62) was launched in the mid ’60s to prepare international standards and technical reports. These reports are focused on the manufacture, installation and application of electrical equipment used in medical practice and their effects on patients, operators and its environment.
TC 62 also looks at surgery, dentistry and other specialities of the healing arts. This committee touches on systems, equipment and accessories, specifically those requirements specially reserved for medical use, focusing on safety.
TC 62 consists of an international panel of experts from 39 countries made up of leading industries, test laboratories, national governments and consumer associations. It liaises closely with other bodies such as the IEC TC 8 (voltages) and ISO TC 215 (health informatics). It also operates with a number of IEC subcommittees set up to work more closely on particular aspects relating to TC 62, such as diagnostic imaging equipment or equipment for radiotherapy.
Further standardisation followed on from this committee. Established in the 1970s, the major goal of IEC Subcommittee 62A is to prepare international standards relating to the manufacturing, installation and application of electrical equipment used in medical practice. This includes systems, equipment and accessories, plus related terminology, concepts, terms, definitions and symbols.
The third edition of IEC 60601-1, the parent publication first produced in 1977 on electromedical equipment safety standards, was issued in December of 2005. It represents a major revision of this family of standards. With an extended range of applications, it contains important guidelines on using collateral standards and, in addition, the major change of requiring manufacturers to implement a formal risk management system.
The extent of the third edition has been significantly expanded by two changes to the definition of medical electrical equipment:
- The document no longer refers to ‘under medical supervision’, which implies that a much wider range of equipment now falls within the scope of the standard. With the advent of paramedical institutions, it is possible that non-medical personnel will also use the equipment.
- The description of equipment was previously described as ‘to be used in diagnosis, treatment or monitoring’ and now has the addition ‘for compensation or alleviation of disease, injury or disability’. This also broadens the range of rehabilitation equipment not covered by other ISO or IEC technical committees.
RETHINKING OF COLLATERAL STANDARDS
There are now almost 75 collateral and specific standards related to TC 62, covering equipment ranging from diagnostic electrocardiographs to electron accelerators. Collateral is the term used to refer to those specific standards that deal with complementary subjects, such as, for example, an alarm linked to a medical device.
Since the publication of additional general requirements in 1993, there has been confusion about whether equipment has to comply with relevant collateral standards in order to meet the terms of IEC 60601-1. The third edition resolves this, as each new collateral standard, when published, now becomes a normative part of IEC 60601-1.
The term normative implies that the document has been developed according to procedure, based on the consensus of IEC members. It therefore represents the international viewpoint of producers, users, consumers and general interest groups on how best to do things.
Taken from an international standpoint, it opens up cross-border business possibilities for products that are immediately marketable in a global trading system. At the same time, it provides scientists and engineers with a framework, in which they can elaborate on international standards that apply directly to their own national requirements.
The third edition includes important guidance on using collateral standards. Manufacturers can assess their own compliance independently, often using different test houses to evaluate the requirements of IEC 60601-1 and the electromagnetic compatibility requirements of IEC 60601-1-2. A manufacturer claiming compliance with the parent standard now also implies that the equipment is in line with applicable collateral standards.
THE IMPACT OF RISK MANAGEMENT
Perhaps the most far-reaching change in the third edition of IEC 60601-1 is the standardisation that requires the implementation of a formal risk management system. There are several reasons for this:
- A standard only represents the state of technology at one point in time. Applying a risk-based approach enables manufacturers to take advantage of evolving technology while continuing to improve safety.
- Various requirements in IEC 60601-1 are intended to reduce risks to the point where residual risk is considered acceptable, regardless of the type of equipment or its application. However, not all types of equipment require risk reduction to the same level. Risk management provides manufacturers with a tool for tailoring the standard to their own particular equipment.
- The introduction of risk management recognises that compliance with IEC 60601-1 is not always sufficient to ensure that a device is safe, especially where there is no particularly relevant standard in the IEC 60601 family.
- Manufacturers have always carried out risk management when applying these product safety standards, reducing the risks associated with particular hazards to acceptable levels. In the first and second editions, standards writers determined the risk management for the user. Hazards were identified, risk control measures specified and the authors established risk acceptability criteria as prescribed pass/fail values.
The third edition of IEC 60601-1 requires manufacturers to have a formal, documented risk management process that conforms to ISO 14971. This latter standard does not so much specify acceptable risk as provide an auditable process for managing risks. IEC 60601-1 makes use of the ISO 14971 risk management process to:
- Identify and manage risks that are not covered by the standard
- Determine when specific requirements are to be applied
- Identify appropriate test parameters
- Deal with specific, identified risks where it is impractical to develop general requirements
- Establish pass/fail criteria for tests, which is impractical in a general standard
There is now a reciprocal relationship between IEC 60601-1 and ISO 14971. While IEC 60601-1 requires the application of ISO 14971, the latter recognises that when equipment complies with relevant safety standards, the risk addressed by those standards is considered acceptable.
Applying ISO 14971 also ensures that the risk management process required for IEC 60601-1 will be fully aligned with the process being used by other product and process standards. It will also be recognised by regulatory authorities around the world.
ESSENTIAL PERFORMANCE
Another change that has significant repercussions is the introduction of the notion of essential performance, defined as performance necessary to achieve freedom from unacceptable risk. Manufacturers are required to identify the essential performance of their product and verify that it is not affected adversely by various tests.
Essential performance can be identified by considering where degradation of performance renders the equipment unfit for use. Where degradation of performance results in unacceptable risk, it is considered to be essential performance. Manufacturers must use risk management to determine where degradation of performance constitutes unacceptable risk, taking into account the state of technology at the time of design.
Although much has changed in the third edition, the standard remains focused on patient safety. Many of the second edition requirements have been retained with little alteration, while new requirements have been added in order to address changes in technology and expectations regarding safe medical equipment.
The most significant modifications are the requirement for formal risk management and the recognition that overall safety derives fundamentally from basic safety and essential performance. Standardisation is now a major focus in the medical device world.