
The scale and fragility of many medical devices, particularly those that are implanted within the body, require manufacturing processes that are capable of achieving high precision, with minimum application of force and impact on the final component, and yet are fast and cost effective.
The laser has long been recognised as a crucial technology in device manufacturing. Classic applications such as pacemaker welding demonstrated the benefits of laser processing, and lasers have found many more applications involving welding, cutting and drilling. New laser sources and processes are being developed every year.
Cutting and drilling
Laser cutting and drilling have long been used in the manufacturing of tubular devices, metallic (hypodermic needles, and cannulae) and polymer tubing and lumen. Pulsed and Q-switched solid state lasers (YAG lasers) have been the common source for fine metallic applications, while CO2 lasers have been the preferred source for heavier metal tubes and polymer products.
In the last decade the rise of the fibre laser has begun to displace the solid state lasers. These lasers are compact, efficient and readily scale up in power. They work by using a doped optical fibre as the active medium, effectively an extremely long, narrow cylinder when compared to a typical solid state rod of 100–150mm × 10mm.
The diameter of these fibres can be less than 50um and this forces the laser beam to have the highest quality “single mode” quality with the ultimate focusability. They can readily be focused to less than 20um, allowing the cutting of fine features. This quality is not at the sacrifice of power. Hundreds of watts of continuous laser power are available with this beam quality. In fact, process speeds are more likely to be held back by component manipulation rather than laser power.
How well do you really know your competitors?
Access the most comprehensive Company Profiles on the market, powered by GlobalData. Save hours of research. Gain competitive edge.
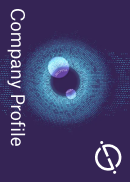
Thank you!
Your download email will arrive shortly
Not ready to buy yet? Download a free sample
We are confident about the unique quality of our Company Profiles. However, we want you to make the most beneficial decision for your business, so we offer a free sample that you can download by submitting the below form
By GlobalDataThe classic application for this cutting is in the manufacture of stents. These devices are manufactured from fine tubes from 1mm outer diameter up to 10mm+ and wall thicknesses down to less than 50um. Precise and detailed cuts are required so that when the stent is expanded the resulting struts can keep the arterial vessel into which it is inserted open.
The cut quality is vital in terms of cut surface quality and reduced heat effect on the remaining material. Fibre lasers are arguably the best source for these, though this will be strongly contested by pulsed laser source manufacturers.
However, all these sources are under threat from the emergence of high average power (10W+) “ultrafast” laser sources. These lasers produce very short pulses, in the range of 100fS (femto (10-15) seconds) to 10pS (pico (10-12) seconds).
These pulses are of relatively low energy, but when delivered in such short pulses they generate very high intensities capable of ablating any material. More importantly, this ablation occurs so quickly that there is simply no time to heat the remaining material. The material exposed to the laser beam is ripped out of the surface without time for the energy to be turned in to heat and conducted into the surrounding materials.
In essence these lasers can machine by “cold ablation” leaving no or, at worst, an insignificant heat effect on the surrounding material. Each pulse removes a small amount of material and by controlling how these pulses are applied it is also possible to achieve very smooth cuts; in some cases the cut surface is smooth enough to begin to act as a mirror.
These ultrafast lasers are now on the market offering an average power of 50W. At these powers the overall machining speeds are comparable with other laser cutting processes and with the greatly improved surface finish they represent a viable advance in cutting processes.
Coding and marking
Laser marking is often overlooked as a laser process. Laser markers are more of a commodity item with a user conducting trials with a supplier and if the quality and price is right then the laser is installed. Laser source developments have again impinged on this process. The fibre laser is becoming the main laser source for marking metals and many plastics. The smaller spot sizes that can be achieved produce superior results in, for example, the marking of stainless steels.
It is not just the laser sources that are important. The substrate has to be receptive to the laser and the marking process often relies on ablation, engraving or other similar material removal processes, the generation of thin oxide layers, or the changing of states of pigment particles in plastics. All these are relatively high energy processes. A lot of work has been conducted on producing suitable photoreceptive inks that require much less energy to change colour. These inks can be printed under an OPP or PE flexible packaging film surface. A CO2 laser can be focused through this film to create an encapsulated image that is very secure.
What is really impressive is the speed achievable due to the lower light energy requirements. Using super high-speed scanners allows the printing of over 2,000 1.2mm-high characters a second. That is around half a page of this magazine’s text per second.
Pharmaceutical and medical device manufacturers are under increasing pressure to print more information, more safety data, ingredient information and so on, and to do this in all the languages of the destination market. Such information can easily take well over 50% of the packaging surface.
This marking technology allows the packaging information to be printed, at the time of production in one language matching the products destination. This can greatly reduce the requirements of the manufacturer to buy in bulk supplies of packaging covering different geographical issues and respond quickly to variations in demand and changes in legislation.
Cleaning
Laser cleaning is most commonly found in the museum conservation industry where it provides a powerful tool in removing from delicate objects the dust and grime of the 21st century.
Various processes have been identified for laser processing and most of these rely on significant difference in properties between the substrate to be cleaned and the contamination on that surface.
The differences could be in thermal properties; for example, organic contaminants may boil off way below the melting point of a metal substrate. They can depend on differential absorption of the laser beam, with the contaminant absorbing the laser beam and being ablated while the metal substrate reflects the beam and is unaffected.
Engineering applications of laser cleaning have been identified but have been slower to develop. Many applications considered have been on a macroscale and have proven slow and hence not viable. Once again, the scale of medical devices are far more suited to the use of laser technology and this is where laser cleaning is more likely to find its mainstream activity in manufacturing.
One key application of laser cleaning is in the cleaning of mould tools. Mould tools represent a significant investment and must be kept in use at the highest uptime to obtain useful payback. Time taken out for cleaning and repair needs to be minimised.
Contamination of the mould tool is commonplace and arises from the polymer being moulded and other chemicals like release agents. They can create thin transparent films that affect mould quality and dimensions. This is particularly true for components in which the moulded form is an optical surface.
Such contaminants can also prove hard to remove. Any mechanical means, such as brushing or polishing, can introduce damaging scratches. Cleaning cycles also have to be run on a conservative basis, so that cleaning may be undertaken more frequently than is actually needed. It has been demonstrated that certain laser types can reliably remove the contaminant without affecting the mould tool. The process is relatively quick.
There are no solvents required and the minute amounts of fume from the ablated debris are readily dealt with.
In a manufacturing process where multiple mould tools are operated in a continuous cycle, it is technically possible to clean the moulds after each moulding shot and thus eliminate the removal of a tool from the production process.
Careful selection of the laser source is required for successful cleaning. There are only a couple of companies offering laser cleaning systems at the moment and these are often based on a laser source that the company manufactures. It is essential to test many different laser sources to identify the most suitable for a given process, so it is essential to “shop around” or conduct process trials in independent laboratories.
Surface modification
The human body is an immensely complicated system, with every change in internal and external environments triggering a response. When medical devices are introduced, whether it is a catheter, stent or artificial hip joint, the physical surface interfaces with the body and the body responds. Hopefully this response is at worst benign. Increasing attention is being paid to surface interactions and once again the laser can provide a tool.
One of the most important properties to consider is the degree of hydrophilicity/hydrophobicity that a surface has. A hydrophobic surface repels water and similar liquids, while a hydrophilic surface encourages wetting and may be useful to improve adhesion. It has been demonstrated that laser treatment of the surface can modify the contact angle, a measure of the wettability.
Various laser treatments have been found. Q-switched YAG lasers and ultrafast lasers have been used to create hydrophobic surfaces on materials such as stainless steels. It has also been demonstrated that using a laser to treat the surface of mould tools has allowed the surfaces of subsequently moulded plastic items to possess a hydrophobic surface.
It is not just about the hydrophobicity of a surface. It has been demonstrated many times that cells behave differently depending on the surfaces on which they sit. The reasons for this are currently subject to much investigation, but it is quite easy to demonstrate the effect.
AILU Medical Special Interest Group
Four areas where advances in laser technology and processes can impact on medical device manufacturing have been reviewed, but there are many more applications. One aim of the Medical Special Interest Group (SIG) of the Association of Laser Users (AILU) is to gather the information on these advances and disseminate them through the medical device and other industries.
This it does through the AILU website, through workshops and in the AILU journal The Laser User delivered quarterly to AILU members. There is also the medical forum on the AILU website where questions can be posed and, hopefully, help received.