
Device packaging is crucial to ensuring the safety and integrity of a product when delivered to the end user. It is also an art in itself, and can be the cause of a product’s success or failure.
Packaging design takes many shapes and forms, but medical packaging is often considered its own niche within healthcare packaging.
A common perspective among designers and engineers in the medical device industry is that if you are doing your job well you are invisible and unnoticed by the customer.
Unlike consumer packaging – often designed to attract customer attention or trigger a purchase – medical device packaging is intended to promptly and efficiently facilitate a medical procedure. Whereas the end user of the medical device is the patient, doctors and nurses are the end users of its packaging. They work at a swift pace and the stakes are often high. So, when the packaging is noticed, it is normally because of a problem rather than admiration.
In 2009, 86.8% of medical device packaging recalls in the US were related to a sterility issue. In some cases this was because the packaging was damaged; in another, the pouch containing the device had not been properly sealed at one end. In one instance, the device – a catheter – had been caught in the seal as it was packed.
Many packaging-related issues can be traced back to part of the design process or not properly evaluating the use of the design by end users.
How well do you really know your competitors?
Access the most comprehensive Company Profiles on the market, powered by GlobalData. Save hours of research. Gain competitive edge.
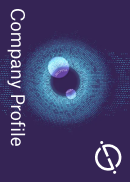
Thank you!
Your download email will arrive shortly
Not ready to buy yet? Download a free sample
We are confident about the unique quality of our Company Profiles. However, we want you to make the most beneficial decision for your business, so we offer a free sample that you can download by submitting the below form
By GlobalDataSo, to design an adequate package that meets the needs of the medical device marketplace, ISO 11607 – the international standard covering packaging for terminally sterilised medical devices – is an excellent place to start (figure 1).
The document, developed by the American National Standards Institute, the Association for the Advancement of Medical Instrumentation and the International Organization for Standardization, harmonises the global regulatory requirements for design, development and validation. The ISO 11607 guidance document states that the goal of a package design intended for use with a sterile product is to:
- allow for sterilisation of the product
- maintain sterility of the product
- allow for aseptic presentation of the product
- provide physical protection of the product.
Product and package analysis
The medical device needs the package, but in some cases the package may need the device, therefore the end product should be considered as a combination of the two. A failure in the performance of either will affect the customer and your organisation. As a result, it is suggested that device and packaging are designed in conjunction wherever possible.
Package design should include input from representatives from several business functions, including marketing, product development, quality, manufacturing, and regulatory. Obtaining as much product information as possible early on will reduce the need for redesigns later, and will protect the product launch date.
Marketing and product development should provide information about user needs and be the voice of customer feedback. Knowing the intended use of the device provides an opportunity to design packaging that does not interfere with a procedure, and could even assist it. The characteristics of the device – such as weight, surface roughness, fragility, shelf life or required sterilisation method – should be understood so the right packaging materials are chosen.
Manufacturing process inputs such as production volumes and location should be obtained to determine if packaging needs to be done manually or if it could be automated. Knowledge of the company distribution channel is also important in terms of understanding the transportation, handling, and storage conditions of the product. Sale price and markets should also be evaluated as these may limit how much can be spent on packaging.
A risk assessment may be appropriate to evaluate the potential failure modes of the product and determine how the packaging design can mitigate any risks that are identified. In some cases, an existing package design may already be available and applicable for use. In this situation, it is recommended to generate a rationale for the compatibility of the existing package design with the new product.
Material and equipment evaluation
After conducting an initial product analysis the appropriate packaging materials and equipment can be evaluated and selected. When it comes to packaging materials, consideration should be given to whether the material of interest is historically accepted within the medical device industry.
Thought should also be given to application of the materials, such as contact with implantable devices, contact with human tissue and compatibility with the preferred sterilisation method.
Materials with current acceptance and historical use often have test data that can be provided by the material suppliers, which can be helpful for ensuring the correct application, reducing the amount of internal testing needed and assisting in regulatory requirements.
All packaging materials should also have a material specification that contains details of its attributes and requirements. The specification will help ensure a consistent product from the material supplier, and ensure compliance with any testing or documentation that may have been conducted to validate the material for use, such as a sealing validation, stability study, or transportation simulation.
Work with your quality department to educate them about the application of your packaging materials and categorise packaging suppliers as appropriate. Consideration should be given to choosing suppliers with a quality system, and your company should think about performing on-site audits of your material suppliers.
Incorrectly manufactured packaging material could result in contamination or a sterility issue, and in a high-volume packaging system that could affect a large amount of product and a large number of customers.
Protective packaging materials such as foams, poly bags or cartons should not be undervalued. Even though they are not as critical as sterile barrier materials, making poor choices about their design, material, or supplier can be just as detrimental.
Many of the same considerations for evaluating and selecting materials apply to the evaluation and selection of packaging equipment. The ability to control your process is important, and you should consider selecting equipment from suppliers that already have knowledge of the needs and requirements of this highly regulated industry.
Sealing equipment should be validated to show that the sealing process is controlled and the selected settings can produce acceptable seals. Equipment attributes such as alarms and lockouts – to prevent sealing outside of a validated process setting – will assist in documenting process control.
Package testing
Testing is a critical part of the design process that makes sure that the packaging system is capable of achieving the aforementioned goals.
Where applicable, evaluations should use standardised test methods – procedures applicable to the medical device industry can be found in Annex B of ISO 11607, part 1 – and sample sizes should be supported by a risk-based rationale. Professional package testing services should be used if your company does not have an internal package testing capability.
Consideration should be given to performing testing under worst-case conditions, such as low seal settings or high sterilisation exposure. Ensure testing is documented in order to provide evidence that packaging systems meet design criteria and support regulatory filings.
An evaluation of production conditions may be appropriate to determine the practicality of the design. In a manual production line, a design that is too intricate may be assembled incorrectly, resulting in shipping damage, or may be simply too time consuming, causing production inefficiencies.
In an automated production line a poor design could jam up a machine, causing downtime and ruining large quantities of material.
Performance in the distribution environment should also be evaluated to ensure the product is delivered to the customer in a sterile state and without damage to the device. Understanding your company’s distribution channel is important when choosing appropriate test conditions and methods. An accurate distribution simulation will help produce an optimal design, and avoid the use of unnecessary packaging material.
The final test
The packaging should be evaluated from the perspective of the end user – most likely doctors and nurses. Have co-workers wear surgical gloves to gauge how easy the packaging is to open. Customer feedback can also be obtained by conducting a focus group using nurses or meeting with a company sales representative – both are good sources for evaluating aseptic presentation and functionality. If meeting with a nurse or sales representative, it is also helpful to get feedback on how well the package design will meet hospital inventory and storage conditions.
Each new medical device comes with its own set of challenges. Most packaging designers recognise that designing a package is typically a process and not a one-day event. To increase your chances for design success, get to know your product, know your company processes and know your end users.