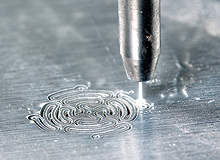
The fine abrasive waterjet (FAW) is a new option that has been developed for precision machining small parts in difficult materials. This non-thermal micro machining method is capable of cutting small precision parts in virtually any material.
The cutting beam operates omni-directionally, with a tool radius as low as 0.1mm. Depending on material type, size and thickness, it can cut intricately shaped parts to a precision in the range of + / -0.01mm.
From macro to micro
The versatility of the abrasive waterjet has, from its introduction in the mid-1980s, led to a wide range of applications ranging from stone, glass and heavy plate – at thicknesses of over 300mm – to precise shaping of aerospace super alloys, engineering ceramics as well as advanced composite and compound materials. The traditional abrasive waterjets used for shape cutting have typically produced a cut width in the range of 0.8-1mm.
The cutting beam that operates with particle erosion is produced in a nozzle assembly known as a cutting head (Figure 1). A simplified description of the operating principles usually starts with the ‘heart’ of the system. An intensifier pump delivers water compressed by 12 at 400MPa via hard tubing to the cutting head.
When the pressurised water emerges from a jewel orifice it forms a hair-thin high velocity jet, with a speed approaching 1,000m per second. The supersonic water jet travels across a mixing chamber to enter a nozzle-shaped focusing tube, where it collimates into a narrow energetic cutting beam. While passing the mixing chamber the jet entrains air. The air flow assists in conveying precision fed abrasive grit (generally garnet) into the mixing chamber. In this way an energetic three-phase cutting beam consisting of air/liquid drops/abrasive particles is formed.
As the beam impinges on the target, material is removed by a combination of erosion mechanisms. Different erosion phenomena prevail depending on what type of material is being targeted.
This material removal mechanism has the benefit of making this machining method effective in cutting a wide variety of materials, virtually of any type, for example, metals, ceramics and polymers. Compared with other typical contour cutting methods, such as the laser or the wire-EDM (spark erosion) the erosion process does not affect the material thermally.
This means that the produced surface is almost free from surface flaws caused by recast layers, thermal cracking or changes in material structure from annealing or other heat-affected zone (HAZ) effects. The absence of HAZ is often a benefit for the abrasive waterjet, making it the choice for parts subjected to fatigue stresses.
Precision waterjet systems
Lately, abrasive waterjet cutting is being increasingly perceived as a precise cutting method, and as such it finds new application areas. With the introduction of FAW, having the same operating principles, cutting beams have narrowed down to the range of 0.3mm and even 0.2mm in diameter. Smaller beam sizes open opportunities for cutting smaller and more intricate geometries requested from precision parts typical of the micro-machining markets.
In transfer of the technology from traditional waterjet machine systems it is vital to recognise that precision parts can only be obtained if the FAW is manipulated at adequate precision.
Placing an FAW cutting head in a regular waterjet machine will only manage to make narrow cuts, but it will not be enough to produce high precision parts. Accurate precision waterjet machine systems available today are built to different standards compared with standard waterjet machines. The precision waterjet machine is calibrated to obtain a positioning accuracy in the range of + / -3 microns. What part tolerances that can be obtained depend largely on the material characteristics (for example, homogeneity, hardness and friability) and part geometry (size and thickness) as well.
Typically, part accuracies down to + / -0.01mm can be obtained. Surface roughness also depends on the material being cut. The fine abrasive grit used has shown to produce surface roughness values down to 1 micron when cutting 15mm-thick hardened tool steel.
Effective cutting materials
Medical device manufacturing has the potential to become one of the most important emerging markets for FAW. As well as the benefits regarding surface integrity and cut quality, the fine abrasive waterjet is a fairly easy process to operate. The universal cutting capability combined with user-friendly CAD/CAM software and intuitive machine HMIs make the FAW machine systems a versatile entry process for those wishing to enter the miniature cutting market.
In existing cutting services, FAW cutting typically serves medical applications for cutting magnesium, titanium, stainless steel and other alloys including memory-shape alloy. Materials with a spring-back function are not negatively affected by the cutting process because material properties remain unaffected. Polymers such as PEEK and rubber are cut. Further, engineering ceramics like alumina or silicon are cut to precision. The non-thermal process also provides possibilities for cutting heat-sensitive bio-materials.
Permeable/porous materials can also be cut with advantage because the abrasive waterjet does not congest the surface as can be the case with traditional machining.
FAW machines are used for shape cutting flat parts, but with a rotary axis the process may also be used for machining more complex designs. Further, material can be removed on surfaces obtaining an abrasive waterjet milling process that may be used to generate trenches and patterns. More advanced machining of this kind require an encapsulated machine design with a highly dynamic motion system.
Cardiovascular implants
Applications using precision abrasive waterjet technology are already being developed in research projects at the University of Hannover. Structures for cardiovascular implants made of bioresorbable magnesium alloys are being developed at the Institute of Materials Science in cooperation of the Leibniz Research Laboratories for Biotechnology and Artificial Organs for the cardiovascular surgery within the framework of the Collaborative Research Centre 599 ‘Biomedical Technology’.
These structures have to stabilise biological patch material after the reconstruction of the heart wall or the aorta in the high pressure system for a certain time and then be degraded by the body (Figure 2a). They differ from so-called cardiovascular stents, which are placed in the vessels and fulfil a static support, while these structures have to be elastic to fulfil dynamic movements with the patch material at the circumference of the graft.
The requirement for such an implant is sufficient fatigue resistance, to prevent graft damage and to obtain graft support. The abrasive waterjet has been identified as an adequate machining system to cut the structures without burrs and the heat-affected zone, which would influence the degradation process. However, the geometries are limited by the cutting width of the traditional abrasive waterjet system (Figure 2b).
The minimisation of the cutting beam diameter leads to a positive effect of the support function and decrease the risk of extrusion of the thin aorta graft through the structure. Further, the finer jet can generate more load-bearing meander shapes without changing the total dimensions of the geometry, which is specified by the biological conditions. As a result the total load and the displacement can be divided into more segments, which increase the fatigue resistance of the implants.
Biological screws made of bone
Biomaterials may be an important application where abrasive waterjet technology offers interesting advantages. Commonly used screws for orthopaedic purposes are usually made of metals like titanium or stainless steel. However, these distort the diagnostics, stay in the body and often need to be removed after the healing process.
Screws made of biological material like cortical bone have less strength compared with steel, but for moderate stresses they can be used, for example, as an interference screw in the cruciate ligament reconstruction.
A project funded by the German Research Foundation between the Institute of Materials Science and the University of Veterinary Medicine Hannover proved that these screws will be resorbed by the body and replaced by new bone tissue.
The biomechanical and osteoinductive properties of bone can be harmed easily by exceeding a critical temperature for a certain time (such as 57°C for 10s). It was shown that the abrasive waterjet is capable of manufacturing a whole screw geometry in the brittle bone with one tool. The turning, threading and the cutting process of an inner contour (width across flat of 2.5mm in a length of 25mm) can be done by this multifunctional tool without any heat introduction. By using a smaller abrasive waterjet diameter it will be possible to minimise the screw’s geometry significantly so that applications in the areas of the oral and maxillofacial surgery or in the foot surgery will be possible.
FAW outlook
The FAW is the first step towards miniaturisation of the versatile abrasive waterjet process, enabling it to enter the micro-manufacturing segment. Finer jets are being developed, and in the near future abrasive waterjets operating at 0.05mm beam diameters are likely.
Another process development underway is the use of the cutting beam for creating more complex shapes by chucking the work material in a spindle, which could be used for cutting stents and other rotational parts. Further, the beam can also remove material while passing over a surface to produce patterns, pockets or trenches.
Already the early development of a machine tool like abrasive waterjet machining centres, are capable of cutting, milling and turning. However, these advanced operations still need a skilled operator until improved software supports these methods.