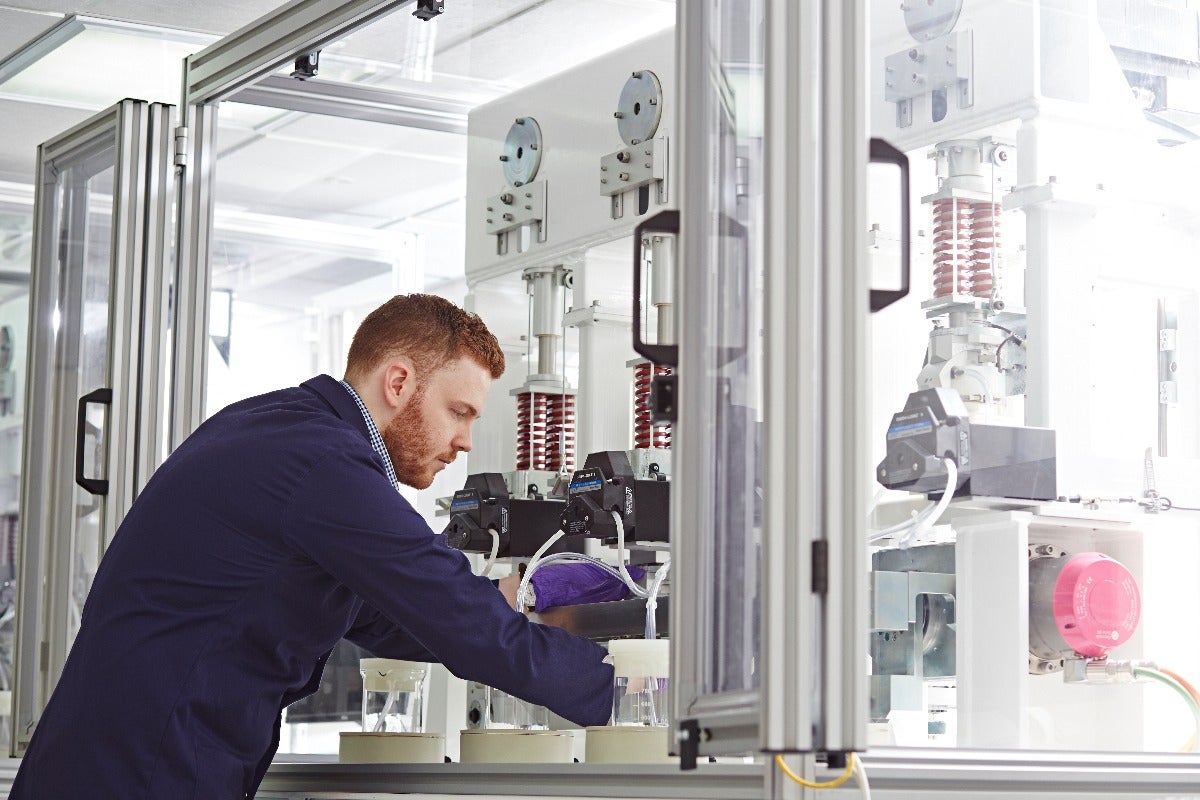
Engineers at the University of Leeds are investigating ways to develop next-generation artificial joints that last longer and produce fewer side effects than existing models.
The £4m project has been funded by the EU’s Horizon 2020 programme.
More than 100,000 artificial joints are fitted annually in the UK, but some implants can lead to pain, become loose or deposit debris into the surrounding tissue, causing severe inflammation.
Failure rates within ten years of joint fitting can range up to 30% for some devices, which engineers believe is due to weaknesses in the wear-and-tear testing of the joints prior to use.
The researchers plan to use advanced computer simulation technology and laboratory tests to capture a more accurate picture of the performance of implants during running, walking, jumping and stumbling.
This will be done using in situ analysis, where the performance of the device is monitored while it is being subject to mechanical testing. Researchers believe this will result in earlier identification and correction of problems.
How well do you really know your competitors?
Access the most comprehensive Company Profiles on the market, powered by GlobalData. Save hours of research. Gain competitive edge.
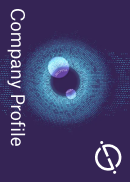
Thank you!
Your download email will arrive shortly
Not ready to buy yet? Download a free sample
We are confident about the unique quality of our Company Profiles. However, we want you to make the most beneficial decision for your business, so we offer a free sample that you can download by submitting the below form
By GlobalDataThe joints will also be designed to be better suited for younger patients.

University of Leeds mechanical engineering professor Richard Hall said: “Surgeons are fitting new hips and knees to patients who are younger, heavier and more active. That means the devices are under even greater stress. They also want to fit artificial joints in ankles and fingers, and they have higher failure rates.
“To overcome these challenges, manufacturers need more accurate testing and better design. We are working with industrial, clinical and academic partners to make that happen, to produce artificial joints that are fit for purpose.”
The international project is being led by the University of Leeds, and the main project partners are ETH Zurich, Uppsala University, Lulea Technical University and Imperial College London.
The project will also train early-career researchers for the medical devices industry.