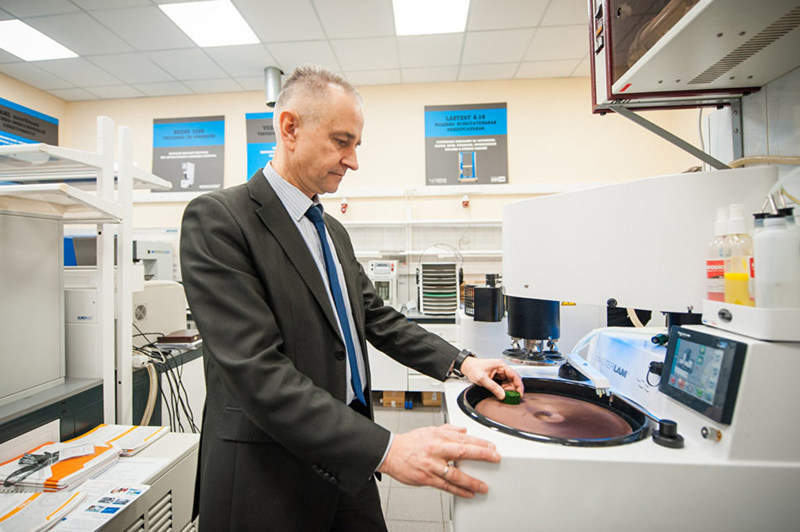
Researchers from the Engineering Center for Industrial Technologies at the National University of Science and Technology (NUST) MISiS in Russia have developed a new technology to produce magnetic materials and permanent magnets at a reduced cost.
The technology is intended to aid in the production of affordable and efficient domestic magnetic resonance imaging (MRI) devices that would potentially decrease analysis cost by 50%.
Described as an effective diagnostic method in modern medicine, MRI is used for the diagnosis of cancer, multiple sclerosis, and musculoskeletal diseases during early stages.
The MRI machines are available with various technical features, and those that could generate high-resolution images are considered ‘difficult to make’ and ‘expensive to operate’.
Based on magnetic materials and components manufactured in the country, NUST MISiS scientists and their industrial partners from the Magneton association created a prototype of an economical and eco-friendly low field MRI.
NUST MISiS Engineering Center for Industrial Technologies deputy director Evgeny Gorelikov said: “We have developed an innovative technology for the production of low-cost hard-magnetic materials and permanent magnets manufactured from alloys of rare, domestic earth metals and their compounds, including the ones obtained in the processing of industrial waste magnetic production.
How well do you really know your competitors?
Access the most comprehensive Company Profiles on the market, powered by GlobalData. Save hours of research. Gain competitive edge.
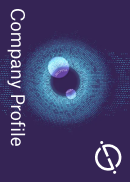
Thank you!
Your download email will arrive shortly
Not ready to buy yet? Download a free sample
We are confident about the unique quality of our Company Profiles. However, we want you to make the most beneficial decision for your business, so we offer a free sample that you can download by submitting the below form
By GlobalData“During the production of raw materials for permanent magnets, we have managed to reduce their cost by 1.5 times through the use of industrial waste magnetic production and cheap alloys of rare earth metals.”
Gorelikov added that the new soft magnetic materials enabled development of magnetic conductors for a magnetic system of the scanner with low loss and high values of magnetisation saturation, resulting in a minimised cost of the devices.