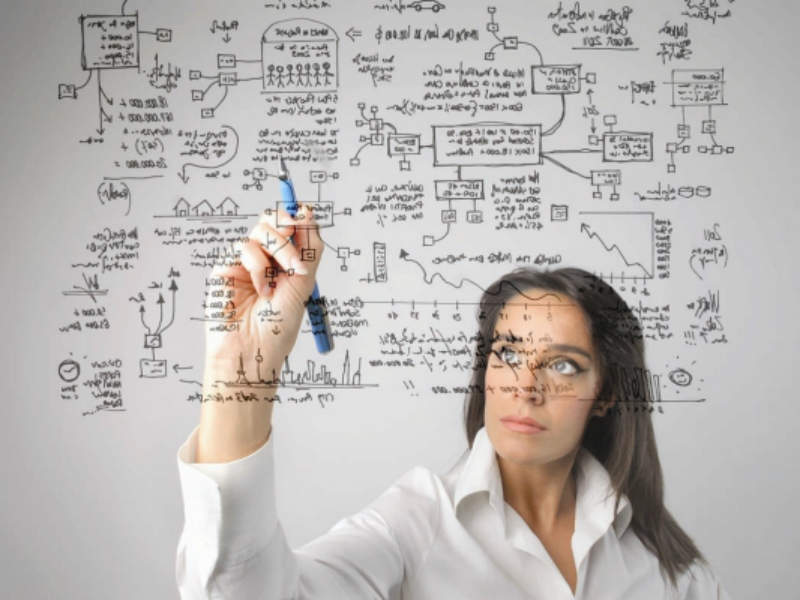

Medical device companies require successful implementation of quality engineering and validation to ensure products consistently meet customer and patient needs. NSF’s strategic, tactical and technical expertise will help you with programme management, quality assurance (QA), and regulatory compliance.
The company assists with product design and development processes, risk management, manufacturing process development, validation, and control. Its services span the product lifecycle, supporting commercialisation and sustainability, as well as addressing product issues and remedial actions to ensure continued safety and effectiveness.
NSF’s comprehensive operations and risk-based services approach focus activities and resources on the deliverables that matter most to your specific requirements. It delivers results by applying efficient and effective best practices in:
Planning and project management
- Prioritise risk factors, business needs, and opportunities
- Develop multi-function integrated plans
- Outline project / programme objectives, requirements, and constraints
- Establish operating mechanisms to drive deliverables, mitigate project risk, and define value
- Deliver consistent communication appropriate to various levels of the organisation
Design control and product change management
- Create design, development, and change management plans
- Perform design verification and validation
- Assist and lead the software development lifecycle
- Ensure a robust engineering change management process
- Address risk management (EN ISO 14971:2012) through planning, analyses, evaluations, and controls
- Develop or remediate risk management files
- Ensure post-market risk re-evaluation
Design transfer
- Develop device history records (DHR) and device master records (DMR)
- Document and implement change control
- Provide process and test method characterisation
- Develop and implement validation programmes including validation master plans, process validation, test method validation, and software and automated systems validation
- Provide pre-qualification, qualification, and validation of supplier programmes
- Develop supplier evaluations / scorecards
Production and process controls
- Ensure production controls consistently deliver products that meet design specifications
- Develop and implement processes, and help address complaint and failure investigations, nonconformities and corrective and preventative action (CAPA)
- Establish and deliver on key performance indicators and quality metrics