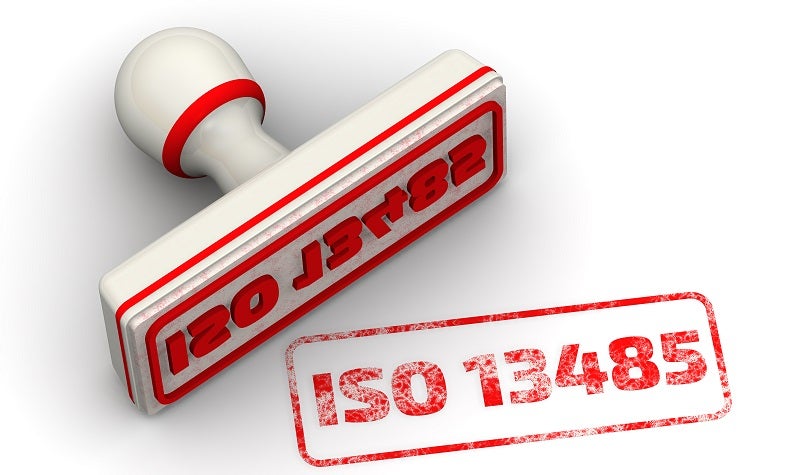
When it comes to healthcare, regulatory requirements are consistently stringent at every step of a medical device’s life cycle. ISO 13485 certification demonstrates that an organisation’s quality management system meets the requirements of the industry and ensures that services and products are maintained up to standard.
EXERA ® wire-based components from Sandvik are used for a variety of applications, including vascular therapy, biosensing and neurostimulation. Working with more than 200 alloys, and specialising in choosing the best materials and configurations, the company works with customers to design, develop and produce medical wire components specifically tailored to the application, including cochlear implants, pacemaker leads and continuous glucose monitors.
Medical Device Technology spoke with Lori Scorpio, QEHS Manager at Sandvik Palm Coast, about the ISO certification that Sandvik has qualified for and what that means for customers.
“ISO 13485 standards go up and above that of ISO 9001,” Scorpio explains. “Obviously all medical devices are FDA approved, so there are more stringent requirements in the ISO 13485 standards than ISO 9001, including documentation, procedures and record keeping.”
ISO 9001 specifies requirements for a quality management system when an organisation can demonstrate consistency and customer satisfaction. The requirements of ISO 9001 are generic and are intended to be applicable to any organisation, regardless of the products and services it provides.
ISO 13485 includes additional requirements for the medical device industry, such as controls in the work environment to ensure product safety, risk management and design control during product development, specific requirements for traceability of implantable devices, and specific requirements for documentation and validation of processes. The certification Sandvik has assures customers that all relevant requirements for medical-wire components are met as approval has been subject to the firm maintaining its system to the desired standard, which is monitored by American Global Standards.
According to Scorpio: “A medical device customer that comes to us knows that we have a quality management system in place that meets their requirements beyond ISO 9001. Being 13485 certified, we meet all of those industry-specific requirements right off the bat.”
Certification also ensures consistency. The required regular audits keep organisations such as Sandvik up-to-date and demonstrates that strict standards are maintained.
“There is more initial work to implement ISO 13485 than ISO 9001, as there are more required procedures and documentation, but once it is in place it is simple to follow and maintain. We do our internal audits on an annual basis, that is a requirement of the standard. We also have a registrar that does an annual audit. Additionally, we have customers that come on site to do a quality systems audit. Sometimes this is annual, sometimes this is
every three years depending on the cycle they developed internally. When customers come on site, being certified to this standard makes it a lot easier for them to complete their audit, because we have all the requirements in place.” Scorpio explains.
ISO 13485 certification is also a precursor to meeting other standards, such as European regulatory requirements, which often require official certification from registrars before sale is permitted. In fact, medical device manufacturing standards across the globe are aligned in part with ISO 13485 and ISO 9001.
For more information about EXERA® fine medical wire-components or to contact Sandvik about developing a medical field device, visit their website.