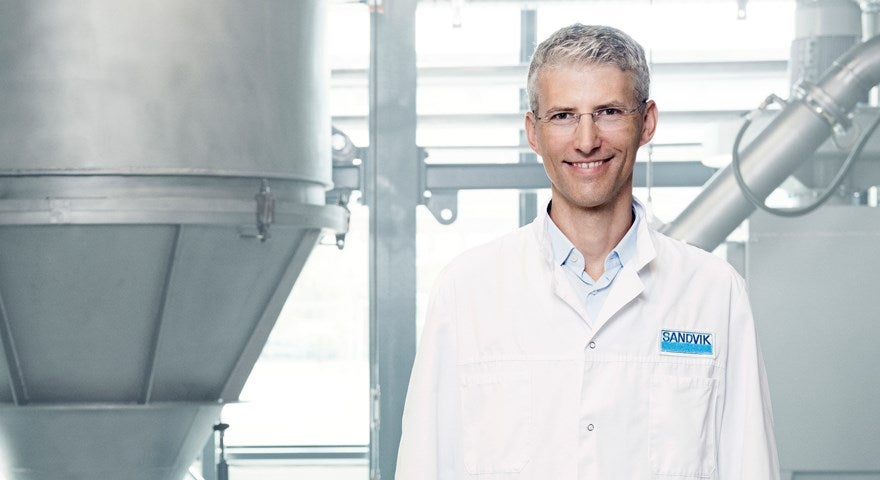
Additive manufacturing, also known as 3D printing, is an exciting step for material engineering and manufacturing processes in Industry 4.0. Utilising computer-aided-design (CAD) software, layers of material are deposited into a precise shape to make a product, reducing lead time and material waste, and creating designs that are impossible to achieve with conventional manufacturing.
In one episode of the podcast series Meet Sandvik, we are introduced to Harald Kissel, Manager of the Technical Team at Sandvik´s Additive Manufacturing division.
“We have the job of transforming the metal powder into printed components,” Kissel explains. “I first came across additive manufacturing in 2010, when we used it for the repair method of a first-stage gas turbine. This worked well, and a few years later I was in charge of a programme that was dealing with technology development, design development and the industrialisation of additive manufacturing for gas turbine power plants.
“When I was doing an executive MBA, I moved into product management, and I was responsible for the development and commercial introduction of the first additively powered turbine upgrade.”
In 2018, Harald moved from Switzerland to Sweden to join Sandvik Additive Manufacturing.
“I was attracted by Sandvik´s perfect set up to be successful in additive manufacturing. To master this technology, you need to have a really deep materials know-how, which Sandvik really has.”
Sandvik has 160 years of leading expertise in materials technology and has been supplying metal powder for additive manufacturing for decades. Its extensive experience in machining methods means that Sandvik also has a greater understanding of post processing than most other companies, as well as an extensive customer-base and a good reputation in manufacturing areas that additive manufacturing may disrupt in the future.
According to Kissel, additive manufacturing will not replace traditional manufacturing entirely. Instead, it has a very attractive “niche” in the manufacturing of high-performance and very complex components. These are components that are facing limitations with traditional methods because of complexity in design, long lead times, or high costs.
Kissel uses the example of medical implants, such as hip or knee replacements. Using current traditional manufacturing techniques, patients and surgeons have a limited choice of off-the-shelve replacement components. These solutions can be uncomfortable for the patient, especially as they are often quite heavy and of course need to fit perfectly.
With computer tomography, additive manufacturing can remake a hip to perfectly match the one that it is replacing in as little as a few hours. These components are custom, lightweight, and much more comfortable for the patient.
To find out more about Sandvik medical materials and alloys download the whitepaper below. To learn more about its additive manufacturing capabilities, listen to the full podcast here – or visit Sandvik Additive Manufacturing’s website There is also special information available on additive manufacturing for medical applications.