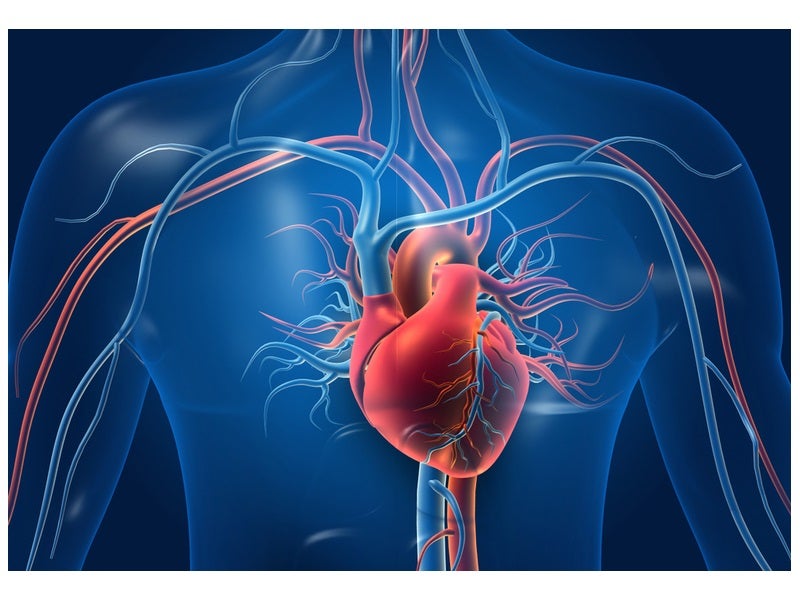
The rising prevalence of cardiovascular disease due to an aging population is boosting demand for surgical procedures. According to the World Health Organization (WHO), 17.9 million people died from cardiovascular disease in 2016, accounting for 31% of all fatalities globally.
For heart surgery, conventional cardiopulmonary bypass (CPB) remains the most common type of bypass, but up to 10% of operations are now using miniaturised CPB (mCPB). Potential advantages include less time in intensive care, lower blood loss and reduced use of transfusions and certain drugs. Minimally invasive mitral valve surgery (MIMVS) has also been shown to offer similar benefits such as enhanced post-operative recovery. This application of minimally invasive techniques in cardiac surgery is being driven, in part, by the development of specialised instrumentation.
Surgery increasing with aging population
Analysis by GlobalData shows that an aging population and associated valvular degeneration is a major driving factor of the prosthetic heart valve market. Globally over 100 million people are affected by valvular heart diseases including valve stenosis and regurgitation.
Valvular stenosis occurs when the heart valve narrows, restricting blood flow and causing the heart to work harder to supply an adequate amount of blood to the body. Degenerative calcification, especially in the elderly, remains a major cause of valve stenosis. Aortic valve stenosis is the most common of the heart valve conditions and mitral valve regurgitation (where blood flows the wrong way in the heart due to the mitral valve not closing properly) affects over 2 million people in the US each year. It is also the second most frequent indication for valve surgery in Europe.
Bioabsorbable stents using polymers
Bioabsorbable stents (BDSs) for cardiovascular applications are becoming more popular, due to the reduction of second interventions. BDSs use biodegradable materials, such as polymers like polylactic acid (PLA) and polycaprolactone (PCL) and magnesium and zinc alloys, to fabricate vascular stents for widening blocked vessels at the early stage.
These stents gradually degrade after implantation into products that can be metabolised by the human body, leaving nothing behind. 3D printing technology has been used to print vascular stents with complex architectures.
New developments for cardiovascular implants
Industry-leading provider of fabrics for medical devices, Sefar AG, is currently involved in the development of several implants that feature medical reinforcement fabrics and meshes. These include Transcatheter Aortic Valve Implantation (TAVI) and an embolic filter to provide high-level protection from adverse events during TAVI procedures. Sefar are also co-developing a valve prothesis and transcatheter solution to treat tricuspid valve regurgitation.
Marcel Rutz, Sefar’s corporate market manager medical, explained the benefits of using high precision monofilament fabrics for implants such as valves and stents: “Sefar’s line of MEDIFAB® products are woven precision fabrics made of synthetic polyester (PET) or Polyamide (PA) yarns. These fabrics offer high throughput rates with an open area starting at 5%, suitable for very low permeability of air, water, and other liquids. Other benefits are its high elasticity, thin material with a thickness of only 50µm, and precision mesh opening of only 11µm.”
“This product line has been specially developed for medical applications and ensures biocompatibility,” continues Rutz, “currently, there are also projects with PEEK (polyetheretherketone) which isn’t yet in the MEDIFAB range. For this purpose, Sefar has the MEDITEX product line, which is based on the process steps of MEDIFAB, but allows for greater process flexibility.”
Challenges of development
“The development of medical solutions takes time, due to admissions procedures and product verification by the customer,” explains Rutz. “It starts with the selection of the correct yarn, and continues to the weaving process where the material can be sent for further converting. The relevant process steps must be qualified and validated to ISO, USP and FDA standards and regulations. Sefar, as a vertically integrated company, offers all of the various process steps from yarn development to the final inspection of the fabric product. This allows our customers to have a custom solution to fit their design and product.”
Checks and safety measures are a huge part of the manufacturing process. “Sefar, as a supplier, must ensure complete process validity and can do so through the ISO 13485 certification. Conformity certificates are enclosed with each delivery, and control is guaranteed for every delivered product, which means the products are traceable,” points out Rutz.
The product line is biocompatible and meets the requirements of USP VI, while the development of the product and the production processes are embedded in a quality system according to ISO 13485, to provide safety and minimise customer risk. “The customer benefits from a simpler approval of their products in the medical market, consequently saving them time and money,” says Rutz.
Miniaturisation accelerating development
Rutz says Sefar’s fabrics are particularly suited to miniaturisation: “With Sefar fabrics, tiny parts can be produced via high-precision laser cutting, for example. High-precision measuring systems check the accuracy.”
Sefar continues to develop new materials and techniques, pushing the sector forward.
Absorbable fabrics are now in development at Sefar, says Rutz: “Sefar is in the beginning of development of absorbable fabrics, this may open new doors for the future in the medical field.”
To find out more, download the whitepaper below.