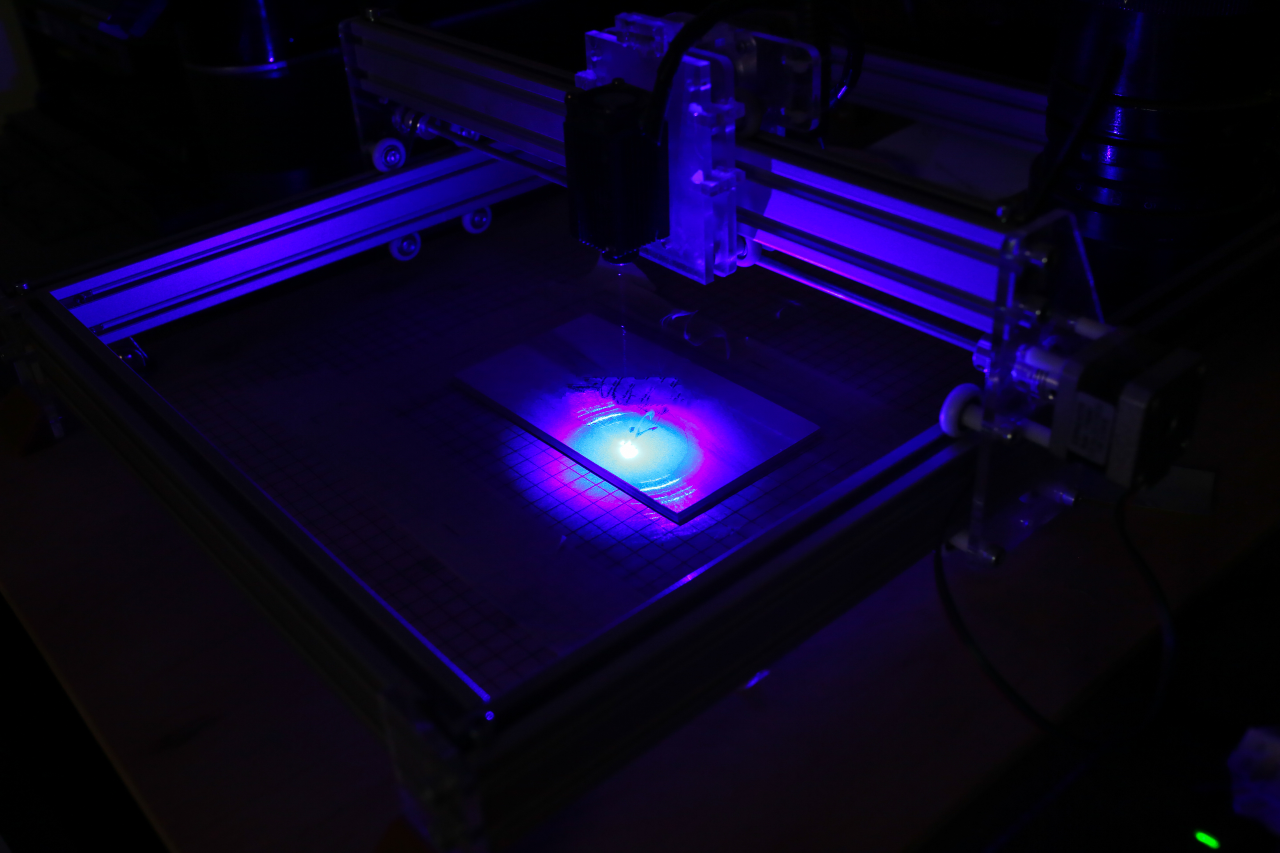
With applications across a huge range of industries, the demands of the laser cutting, welding and marking market are constantly evolving. How does a market leader with over 50 years of experience navigate this sector to provide its clients with exactly what they need? Coherent brings together expertise with the broadest product portfolio and global scope to deliver full solutions to its clients. Thorsten Ferbach, Business Development and Product Line Manager, tells the Coherent story.
Moving with the market
In recent years, the industrial laser market has been moving away from component-based suppliers and towards companies offering complete solutions. Coherent has kept abreast of this trend; in particular, its acquisition of ROFIN in 2016 has allowed it to transform its offering. “That means providing processing solutions for end customers that need more than just a laser source,” says Ferbach. What had previously been the role of independent integrators has become part of Coherent’s core service. “We contribute full solutions which accomplish the process, the quality and the throughput for the customer,” Ferbach adds. Today Coherent offers it all, he says: “We have competence as a developer and researcher and a very broad, complex portfolio of all kinds of laser technologies, combined with the knowledge of putting these things together to make a customer-oriented process solution.”
The company’s Munich-based business unit takes care of the main industrial markets, which are diverse. “It’s the medical device industry, the automotive sector, electronics industry, consumer goods, semiconductors, and so on,” says Ferbach. In particular, the company provides micro processing and marking capabilities in these sectors. “We utilise picosecond, femtosecond, and high-power UV lasers and make very attractive, applicable solutions,” he adds.
In the medical device industry, Coherent products have a range of crucial applications. For example, laser cutting is used in the production of devices such as stents, implants, or hypotube. Also track and traceability is vital in this industry. “Due to passivation, sterilisation and autoclaving, there’s always a harsh environment applied to metal surgical instruments, explains Ferbach.”
This makes it extremely challenging to find a marking technology that will resist corrosion, especially for expensive pieces of kit such as endoscopes. This is where Coherent’s picosecond laser marking technology comes in. “We challenge ourselves every day to make what customers need more beneficial for them and more efficient,” Ferbach concludes.
A laser for any application
One thing that sets Coherent apart from competitors is the sheer breadth of its product portfolio, which includes laser technologies of different power levels, different technology levels, wavelengths, platforms, attributes and beam properties.
“We work with the largest portfolio in terms of laser technologies,” says Ferbach. This allows Coherent to act as an “open-minded consultant”, taking the whole variety of possible solutions into account when serving its customers. “This is usually a guarantee for the customer that the most applicable and suitable solution will be selected,” he adds.
Beginning with the end user
The precise deployment of products revolves around the needs of the client. Much of this is done through Coherent’s application labs. A customer can come to Coherent with goals for quality, locations, throughput and speed, but without a specific understanding of what they need. “The lab is equipped with all the laser solutions we have in our portfolio for marking, cutting and welding,” explains Ferbach. “Customers can expect a report back with an overview of the parameters, highlighting what is important and what can be tuned.” The result is a recommendation for the solution that will work best.
Crucially, this solution is more than a single component or hardware. It encompasses the laser source, including considerations such as power, wavelength, colour and pulse length, through to the workstation and includes automation, internal moving parts, software and user interface as well as any mechanical handling and quality checks. Simplifying recipe generation is often a major part, Ferbach explains, since “today sometimes production changes are pretty complex and cause a lot of downtime and need a lot of specialised people”. An intuitive, easy-to-use HMI that allows quick programming is of great importance.
Today’s customers are demanding, but Coherent has the strengths to rise to this challenge. “With our global spread we have better access to customers and continuous operation, and we are closer to them in terms of warehouses. It ensures their production flow and reduces downtime significantly,” says Ferbach. As well as this, “due to the size of the company, we are qualified to support and serve very big global players”.
What comes next?
“This is our aim – to make a customer process more efficient, more reliable and higher quality at higher throughput and lower operational cost,” Ferbach summarises. As well as focusing on the customer level, this requires Coherent to have its finger on the pulse of? the market as a whole.
“We are seeing a clear trend towards simplicity, innovative operation and process monitoring,” observes Ferbach. In the medical device industry in particular, Coherent intends to strengthen its offering of dedicated tools for marking, as well as running a new software HMI concept.