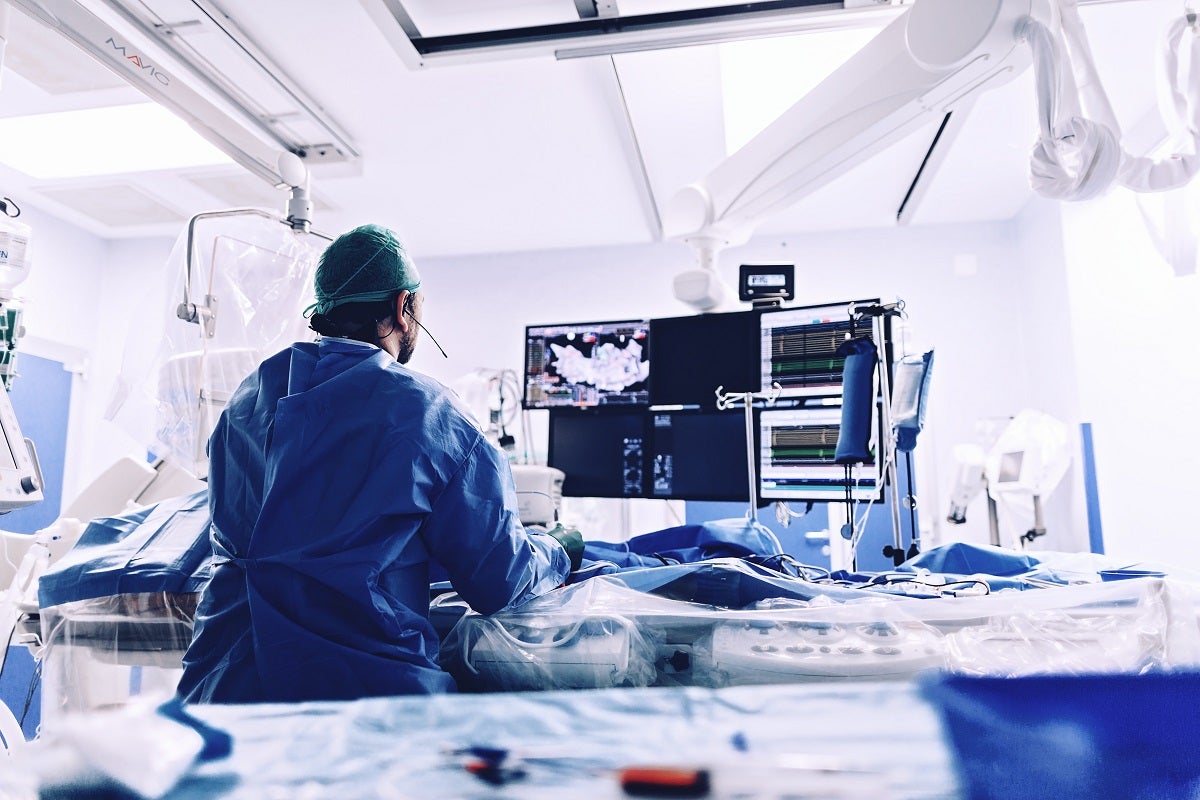
From catheters to home health monitors, more people than ever rely on medical devices. With the elderly population rising, this increase in demand is expected to continue, putting pressure on manufacturers to reduce the cost of ownership for therapeutic devices without compromising life-critical performance.
With the lives and wellbeing of patients at stake, reducing standards to reduce expenditure simply is not an option. Thankfully, the medical device industry is a thriving one, with the development of smarter solutions and smaller devices leading to exciting, cost-saving innovations.
Finding cost-effective solutions without compromising quality applies to all components and materials used in a medical device, but the digital age demands smart solutions, meaning that healthcare providers and patients expect excellent reliability and connectivity. This requires connectors and cable assemblies, RF components and sub-systems to each offer optimal performance without breaking the budget.
Simpler designs, unparalleled performance
Smiths Interconnect understands that reliable, cutting-edge connectivity is critical in the medical sector. The company focuses on smarter engineering without falling into the trap of building connectors that are more complex and sophisticated than the application requires. Instead, optimal reliability and performance are achieved through simplified assembly, design flexibility, and uncompromised quality.
It may sound too good to be true that a simpler, more cost-effective solution can deliver superior performance and reliability, but the proof lies in Smiths Interconnect’s products, which are used across the medical industry.
Durable and reliable connectors
Smiths Interconnect’s HyperGrip® Flex builds on its popular HyperGrip® series of circular plastic connectors, which utilises Hypertac® advanced hyperboloid contact technology with one-hand disconnect. HyperGrip® Flex maintains the performance, ease-of-use, high durability, low power consumption and reliability of its predecessors, meeting rigorous medical industry standards. The HyperGrip® Flex is finger-proofing certified to IEC60601, flammability rated to UL94 V0, and compliance with most sterilisation methods.
Additionally, a simple crimp and poke connector design offers a high-volume and low-cost production process without compromising durability or RoHS (Restriction of Hazardous Substances) III compliance. The frictionless termination design contributes to industry-leading durability by minimising potential damage from repeated insertion/extraction.
Connectors are not a one size fits all solution, but with an advanced keying system, Smiths Interconnect’s customers can build connectors with six different keyed versions of the same standard connector. This means that medical device manufacturers can reduce inventory complexity and lead time but still have an optimised solution for a wide range of applications.
Connector solutions for disposable medical devices
Smiths Interconnect’s EcliptaTM is a PCM edge card connector designed for one-time-use applications.
The innovation lies in the double-ended termination technique, which utilises the printed circuit board (PCB) as the contact on the disposable side of the connector so that there is no need for a contact system. Medical device manufacturers also have the option to add their own PCBs, reducing assembly time, supply chain risk, and inventory costs. Further design flexibility includes the ability to add active surface mount components such as Electrically Erasable and Programmable Read-Only Memory (EEPROM).
Specially designed for medical applications, EcliptaTM connectors are suitable for standard sterilisation protocols (such as Autoclave, EtO, and Sterrad), as well as chemical wipe down. Its design flexibility makes it ideally suited for a range of applications, from ablation catheters to RF generators and at-home health monitoring devices.
Summary
The resulting solutions – one a design evolution, the other a design revolution – draw on Smiths Interconnect’s extensive knowledge and experience to respond to the real-world requirements of medical device manufacturers and service providers.
Key features include:
- Sleek, premium quality ‘look, feel and performance’ Smiths Interconnect’s solutions are trusted for
- Quick, one-handed mating/unmating
- Frictionless termination design that minimises potential damage from repeated insertion/extraction
- Reassuringly reliable contact performance
- Designed for actual application cycle life
- Simplified assembly for cost-efficient mass-production
- Assembly versatility and easy to customise
- Easy to install, use and service in the field
All this adds up to a lower cost-of-ownership, reducing the cost-of-therapy without undermining the quality of care.
To find out more, download the brochure below.