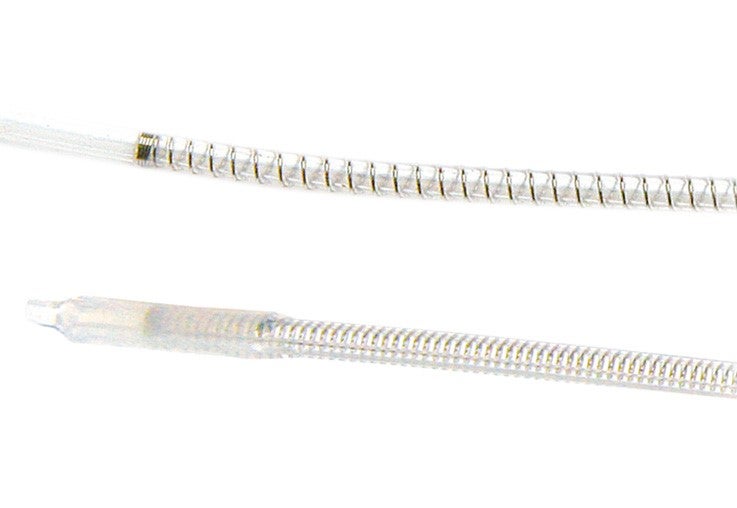
Catheter tubes have many uses in healthcare. They can be inserted into the body intravenously to deliver fluids and medication, are used during surgery, and can act as a conduit to drain a patient’s bladder. Catheters must be flexible enough to navigate the human body and firm enough to resist kinking or collapsing during use. How do manufacturers address these design challenges?
The key to making catheters both flexible and firm is to use a reinforcement coil within the tube, as a method of providing ‘flexible rigidity.’ The catheter shaft remains flexible but can resist collapsing. Soft medical-grade plastic is used for the tube while reinforcement is provided by a helical coil spring. These coils are also an essential component during the manufacturing of guidewires, which are used to guide catheters within the body.
While various metals are used to manufacture the coils, such as stainless steel, platinum iridium, platinum tungsten, tungsten, and the alloy nickel titanium (known as nitinol); the coils are typically coated with polytetrafluoroethylene (PTFE) to decrease friction and enhance guidewire movement and even device tracking.
The trend for miniaturisation is driving development across all areas of healthcare. Replacing invasive surgery with guidewire implantation has a range of benefits, including fewer clinical visits for patients, shorter hospital stays, and reduced post-surgery risk. The challenge is to provide extremely fine wire coils. For minimally invasive catheters and guidewires, coils as small as 0.001” are used.
Catheter components
As well as coiled wire, other options for catheter components include:
Hypotubes – metal tubes used for minimally invasive surgery catheters in conjunction with balloons and stents but can also carry fibre-optic cable connected to pressure sensors on guidewires. Hypotubes provide a rigid over-structure to protect key components and must be able to resist kinking without compromising ‘glide’ ability to allow it to be manoeuvred through the body. Hypotubes need to be small and flexible, enabling them to steer catheters through arteries that typically have an internal diameter of just 4mm (0.16”).
Braiding – For applications that require increased torque transmission, burst strength, or column strength, extremely fine round or flat stainless-steel wire is used to braid-reinforce the tubing material.
Helical Hollow Strand (HHS) – This is a strand with an open centre working channel, most often used to transmit torque or pushing forces due to its whip free characteristics and high resistance to kinks. Manufactured in single, double, or triple layers to provide varying levels of flexibility and control.
Designing custom catheters
Leading wire component supplier Custom Wire Technologies (CWT) is an experienced producer of medical coils for catheters and guidewires, and indeed, their very first customer was for custom catheter reinforcement coils. Still a large part of its business 20 years later, CWT still produces coils in a wide range of sizes, lengths, and materials; customised to the stringent design needs of some of the top medical device original equipment manufacturers (OEMs).
“Everything that we manufacture at CWT is customised,” says John Corsten, technical sales manager at CWT. “If you can supply us with a print and specification (or even a sketch), more times than not we will be able to help. After the initial engineering review process, if we see potential issues with manufacturability and repeatability, we will offer suggestions. Our customers appreciate our willingness to collaborate with them.”
Unfortunately, many of our current supply chains are suffering from problems brought about by the Covid 19 pandemic and current geo-political instabilities. For the R&D departments of OEMs wanting to do rapid prototyping, this can be a problem.
CWT is tackling this issue with its revolutionary QuikCoil programme, designed to help its customers navigate some of the current problems arising from vulnerabilities in the supply chain, such as delays and component scarcity. QuikCoil provides fast turnarounds on orders, aiming to provide custom-made coils within a week.
“Time is of the essence at the R&D level and CWT’s ability to manufacture up to 20 custom coils (either round or flat wire) in a week has been well received by the medical device industry,” says Corsten.
CWT’s fully equipped laboratories enable its technicians to work with OEMs through every step of the design engineering process, ensuring high-quality, finished products, including its signature helical coils for catheters.