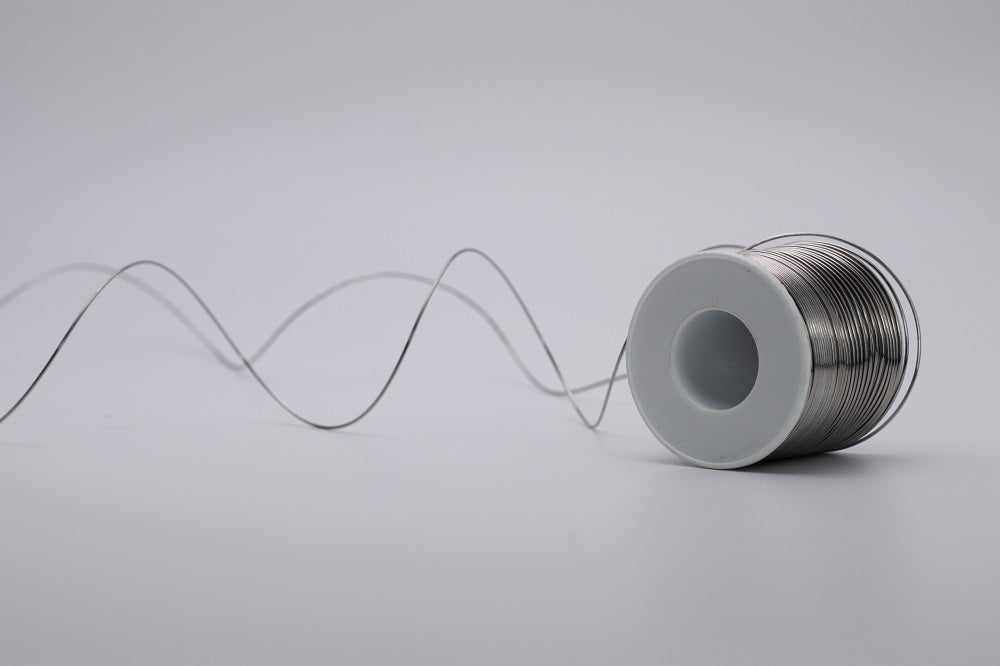
Metals, with their strength and durability, are still regarded as the go-to material for many medical devices. Advantages of using metals include strength, a sterile surface, fracture toughness, electrical conductivity and the combination of both elasticity and rigidity. This is particularly important for metals used in stents (used in blood vessels for dilatation) as they require some elasticity for expansion while also remaining rigid when dilated. Most important is safety, and metals implanted in tissues must not show any toxicity or metal ion dissolution by corrosion or wear.
Types of metals used
Due to their non-oxidisation properties, stainless steel and cobalt chrome alloys are the optimum choice of metal for medical devices, along with titanium. Nitinol, a metal alloy of nickel and titanium, is popular due to its superelastic and ‘shape memory’ properties. Additionally, coil springs used in catheters use platinum iridium, platinum tungsten, and tungsten for radiopacity.
Stainless steel
Stainless steel is the most versatile metal used in medical devices due to its strength and corrosion resistance properties. The most common alloys used for medical device applications are 302, 304V, 304LV and 316LVM. These alloys are made up of between 17 to 20% chromium and between 8 to 15% nickel. The presence of chromium provides corrosion resistance by forming a chromium oxide film on the surface of the alloy.
Typical applications include stylets, catheters, guidewires, springs, needles, orthodontics, bone pins, skin closure staples and orthopedic cables.
Titanium
Titanium is stronger, lighter and more corrosion resistant than standard grades of stainless steel. Pure titanium promotes osseointegration, meaning that bone can grow into the material, further helping to anchor implants in the body.
For pure titanium, typical end uses include pacing leads, needles, sutures, ligature clips and orthopedic applications.
For alloyed titanium, applications often include springs, surgical staples, ligature clips, orthopedic cables, orthopedic pins and screws and orthodontic appliances.
Nitinol
Nitinol is a family of alloys consisting of nickel and titanium. It is extremely corrosion resistant and demonstrates excellent biocompatibility. Nitinol exhibits superelasticity and/or shaped memory effect due to the crystalline structure of the material. The ability to remember and return to a specified shape after deformation when exposed to a predetermined temperature has been a gamechanger in the medical device industry. If surgeons need to navigate in particularly tight areas, nitinol has both flexibility to change shape as needed and the durability to endure considerable amounts of strain (8%).
Common applications of nitinol include guidewires, stents, forming mandrels, stone retrieval baskets, orthodontic files, and arch wires.
Superalloys
The most common superalloys being used in the medical device industry are cobalt-chromium based. These high-performance materials offer strength, fatigue resistance, ductility, good biocompatibility, and corrosion resistance. The most commons alloys are MP35N®, L-605, Elgiloy® and FWM™ 1537
Typical end uses for superalloys include stents, pacing leads, surgical clips, vena cava filters, orthopedic cables and spinal rods and screws.
Metals in medical devices
Custom Wire Technologies (CWT) is a US-based manufacturer of medical wire solutions with over 50 years of industry experience, implementation of the very latest technologies, and works with all the above-mentioned alloys. From custom core wires and coils to K-wires, Steinmann pins to fixation devices, CWT provides its customers with custom manufactured medical components using a range of certified materials. The main alloys that CWT works with are stainless steel 304V and 316LVM, and Nitinol.
Find out more by downloading the whitepaper below.