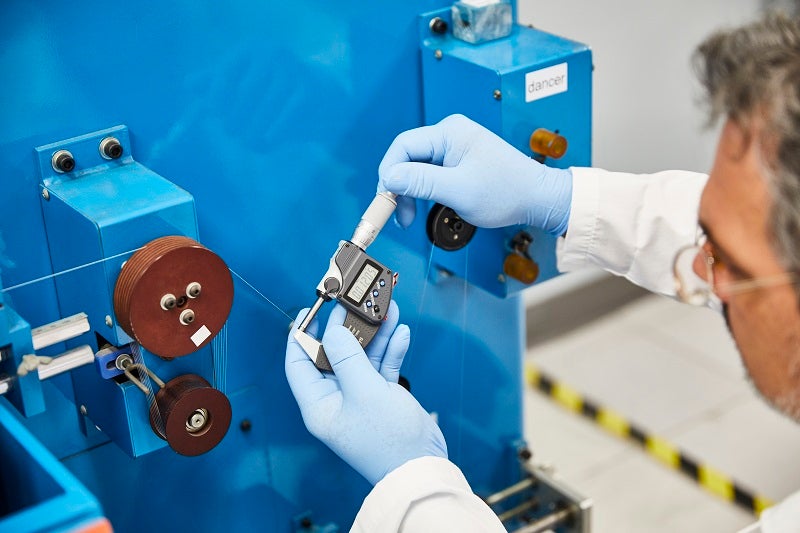
When it comes to medical devices manufacturing, Swedish firm Sandvik has developed specially designed machines to produce its medical-grade, ultra-fine wire promoted under the trademark EXERA®. Medical Device Network spoke with Gary Davies, manager at Sandvik Materials Technology’s business unit for medical wire manufacturing, about how the company is automating processes to ensure precise and uniform products.
“We adapt our equipment to automate processes wherever we can. The main reason for this is creating much more repeatable processes and therefore a reproducible product, which is key for medical device manufacturing,” Davies explains. “In some cases, in order to hit the tolerances that we need for certain applications, the method required is simply too precise for a human to do manually.”
Automating these processes is much more complicated than having robots taking over a human’s job, however. In fact, the team at Sandvik has worked diligently to modify automation and analytics technology as part of its service that offers fully customised medical wire configurations specifically designed for each of the company’s customers and their specific devices – bespoke is the name of the game.
“When it comes to automating manufacturing,” says Davies, “you have to find the right sensors or the right control points to automate the equipment. The challenge with these ultra-fine wires and components that we’re making for the medical device industry is that it sometimes becomes difficult to find sensors or controls to be able to do that.
“One example is our multi-fibre cable. Let’s say it’s a three-strand cable; if you had it in your hands and you looked at it, you would swear it’s only one wire because you cannot discern the colours of the three different wires in that cable, they’re far too thin.
“The people making the devices need to have three different colours and the colour orientation needs to be maintained. For wires such as catheter leads, they need to lie flat, so we have systems to detect and to make sure we’re controlling our equipment to ensure that the orientation always stays the same.”
Far from taking control away from the people operating the machine, automating processes provides the operators with better insight into the progress of the product, allowing them to notice errors or make any necessary adjustments.
Davies adds: “We can monitor it and we can make any adjustments to make sure we’ve got a very controlled product. We’ve done a lot of work with image analysis equipment that we have modified, including lighting and different magnifiers. There’s a lot of work that we do internally to adapt what’s available in the industry to make the product successful.”
Automation can be used at various stages of manufacturing, including precision cutting, forming multi-strand wires and even for applying or removing coatings.
“For selective plating or selective stripping of the polymer coatings on the wire, medical device manufacturers have very tight tolerances on how much gets deposited or gets removed, depending on the application. So in this case, it’s all about motion control to make sure that the deposit or removal is done in a very controlled manner.
“Since we’re contacting a solid wire into a liquid solution, there are some fluid dynamics there that we have to overcome with a different set of sensing techniques so that we get the right result in terms of dimension and thickness. There’s a lot of automated control development that we do internally here to our equipment to accommodate the need to get these tight tolerances.”
For more information about EXERA® fine medical wire-component manufacturing and typical processes, including available materials and surface treatments, download the white paper below.