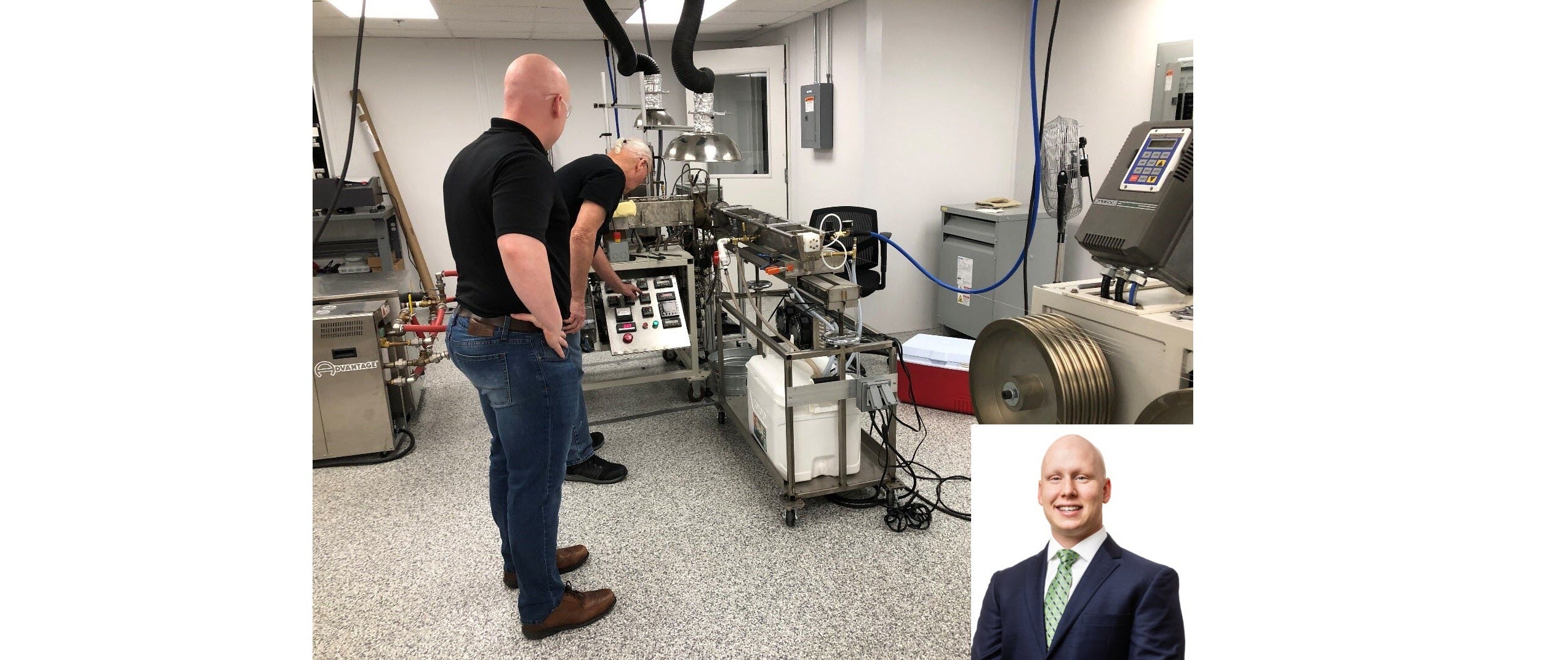
For its development partnerships in the medical device industry, Sandvik brings a lot to the table. Along with its extensive range of materials and metal alloys, Sandvik offers insulation and bonding coatings that are expertly chosen and applied to meet the needs of the customer.
As well as choosing the right coating material, the appropriate coating technique is essential for achieving precise, economic and uniform insulation application. Coating applied by an extrusion processing route has been recently added to Business Unit Medical’s capability to complement its already wide range of polymer possibilities. Sandvik Materials Technology’s EXERA brand of medical wire and wire-based components are manufactured in both BU Medical’s Palm Coast, Florida and Tucson Arizona facilities in the US.
Medical-device technology spoke with Robert Naber, an engineer developing extruded coatings about his involvement in the process/product development method and how extruded coating provides fine wire benefits costumers in the medical field.
“The product development process requires quite a bit of planning and can be time-consuming to ensure the best possible outcome.
“We get our day started very early because it takes time to heat all of the different thermal components of the coating system. For example, it might take a couple of hours to make sure all temperatures stabilise to a precise level including the chilling system which will maintain temperature throughout the run.
“The coating resin needs to be carefully prepared the night before a new extrusion run to prevent water vapour and other impurities from being incorporated into the coating. Also, the machine and tooling needs to be carefully selected and cleaned to prevent any cross-contamination, flow restriction or charring that could cause defects in the deposited film. Similar to the coating resin, input wire is manufactured to precise tolerances and temper and split onto a defined number of spools for the actual coating run.
“And then we start the process. Key process parameters such as temperature and pressure are adjusted and monitored when the correct coating thickness and concentricity are achieved. Other machine tooling parameters and settings help contribute to the dimensional control, as well as the surface quality of a wire. With our very good concentricity and dimensional control, we can offer an extruded product with capability tolerances and wall thicknesses that exceed global standards. We can do wall thicknesses as thin as 0.02mm (0.0008in) and even thinner on request. Of course, standard thicknesses are also possible.
“I find that qualitatively looking at the wire, feeling the wire, evaluating strip ability in addition to quantitative dimensional measurements from the laser gauge, help us evaluate our performance. However, there is a considerable amount of math that needs to be applied when establishing toolsets and process parameters too. The combination of math and art is where the magic happens with the extrusion process.
Overall, extrusion is a cool operation because although it can be complicated and involved during the product development phase it provides great capabilities and platform for a wide variety of applications. No doubt, it’s detailed work and takes patience.”
Various coating techniques and processes are used for achieving insulation and bondable coatings of fine wire, such as continuous flood coating, which guarantees a complete coating over the wire surface that is both consistent and firmly adhered. So what are the benefits of using extruded wire coating as an alternative?
“The advantages for the medical field are threefold,” Naber explains. “For us, one advantage is that you can coat very quickly. It’s a much faster process compared to flood coating operations and only a single pass is required for most products.
“The other advantage is that we’re able to coat a wider variety of materials because flood coatings mandate that the resin can be dissolved in a safe solvent. Not all materials can be dissolved easily.
“The third advantage is that you can achieve a more precise coating where the quality of the coating is critical especially as thicker coating is required. EXERA products are known for very high-quality surface treatments in general, but the extrusion capability can take one step further in supporting our customers with improved performance of their products.”