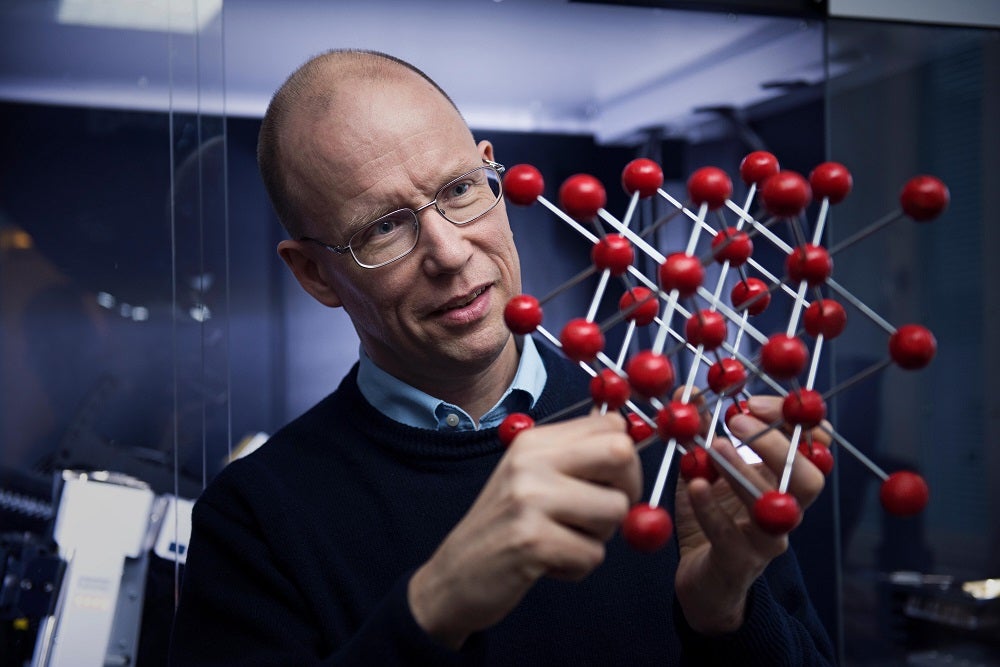
With a long track record as experts in metallurgy, Sandvik has become world-renowned for its stainless steel, especially in the mining industry. Over the course of its 160-year history, the company has expanded its capabilities and acquired other manufacturers to broaden its scope. In fact, when a small company in Florida, USA became part of Sandvik Group in 1997, it brought with its expertise in the production of ultra-fine wire and facilitated new business ventures that the company’s founders couldn’t have dreamt of.
Back then coils for electronic disks, which was the company’s flagship product, were losing popularity to new streaming devices, so what was next for Sandvik’s high-quality fine wire?
According to Lena Wiig Boström, marketing communications manager for Sandvik’s business unit medical Medical: “We were contacted by a pacemaker lead manufacturer who asked us to try to manufacture the wire component for that, and the rest is history.”
“When we saw the demand from customers to get support to make more difficult configurations, and with our teams’ technical skills in building machines, we saw a future in rising up the development ladder.”
Sandvik’s ability to support customers with these configurations is key, as many OEMs struggle to find in-house expertise that covers every aspect of a medical device component, especially when it comes to choosing coatings. From cochlear implants to pacemaker leads, continuous glucose monitors, catheters and guidewires, medical wire is the essential element for transmitting, sensing, or stimulating signals within the body.
Not only do these components need to be biocompatible but depending on the application they will need to offer a variety of other features, such as lubricity, conductivity, or fatigue resistance. Metallurgy, process development, and other configurations, such as thickness or coiling, all contribute to how medical wire functions in the body, so where do OEMs begin when it comes to the design of their medical wire?
In 2016, Sandvik launched its EXERA® brand, which provides custom-designed medical wire components that are expertly configured for medical devices. From custom alloys to a broad range of surface treatments and coating methods, EXERA® components have been used for a variety of applications, including vascular therapy, biosensing, and neurostimulation.
“When it comes to metallurgy, we have more than 160 years of experience, so we have the knowledge to support customers and make custom alloys,” Wiig Boström explains. As well as the materials themselves, we have other configurations to consider, and coatings are one of our key strengths. Our design engineers have developed coating methods that really give high-quality surfaces that are even and consistent.”
“For an individual customer, we can support them to set up an automated process for the operations that are typical for their product; we have a lot of different process operations that we support customers with and produce tailor-made solutions.”
For more information about Sandvik Materials Technology and the EXERA® brand or to contact them about forming a development partnership, download the whitepaper below.
You can also meet Lena Wiig Boström and the Team from Sandvik at Compamed. Hall 13, booth C45. We are happy to tell you more about our wide range of materials and coatings, now also including extruded coating capabilities