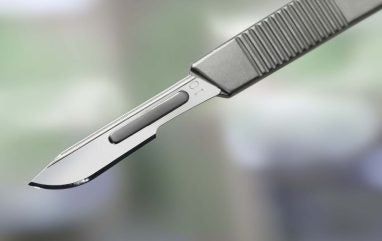
More than 310 million surgeries are performed worldwide each year, and this number is expected to continue growing due to the increasing prevalence of disease and the burden of age-related health problems. Many chronic diseases, including diabetes, cardiovascular, cancer and age-related osteoarthritis and eye conditions, like cataracts, will at some point require surgical intervention.
Investment in surgical robotics is also driving growth in surgical procedures, particularly for minimally invasive operations. This is because robotic surgical technology allows surgeons to operate with greater precision, reduce the potential for complications and result in faster recovery periods for patients. According to market intelligence firm GlobalData, the total surgical robotics market was worth US $4.6 billion in 2020 globally. By 2030, the firm projects that the market will have grown at a compound annual growth rate (CAGR) of 8.5% to US $10.3 billion.
Cutting edge
More operations means robust demand for the tools required for successful patient outcomes, but surgical blade and scalpel manufacturers looking to carve out a slice of this market must appreciate the delicate balance between protecting the quality of the product while also offering it at a price point that will be in the range of cash-strapped healthcare systems.
Aditya Dispomed, a family business that has manufactured disposable surgical blades and scalpels from its factory on the outskirts of New Delhi since 1970, has seen many of its competitors struggle to achieve this. In fact, B Braun is the latest major brand to exit this market, but Aditya, which currently has an estimated 15% of global production capacity, only sees opportunity over the coming years. It bought B Braun’s surgical blade unit in 2023 in a landmark purchase that managing director Rajiv Kehr said will allow the firm to double production once operations have been integrated, expected by April 2024.
“Government-funded healthcare systems are under increasing amounts of pressure to deliver cost-effective solutions, but compromises can’t be made when it comes to patient safety,” says Kehr. “When it comes to surgical blades, reliability and consistent high performance are crucial. The blade must have a tremendous amount of sharpness to achieve the precision necessary for successful surgery. This comes down to the quality of the material.”
Quality steel combined with robust manufacturing process
Aditya Dispomed products have been at the forefront of some of the critical medical interventions in European hospitals, aiding doctors to perform surgical procedures more effectively.
Upon partnering with Alleima, the company sought a strip steel provider willing to engage in close collaboration to create a bespoke and stringent specification. “A key performance parameter for a surgical blade is consistent sharpness and edge durability. For this to take place, you need a robust manufacturing process, which we have, and the right steel input. Together, that’s the perfect marriage,” says Kehr.
“There are local companies in India that offer quality steel grades, but Alleima’s long history and exemplary credentials in metallurgical innovation and research puts it in a different league – and it was important for us to work with a company of such heritage to build trust quickly in a global market. Apart from that, we needed a partner whom we could rely on. Ultimately, without the steel input, our production stops. We can’t make anything.”
“The prudent thing to have done would have been to have a backup. But we never did. We are confident that Alleima will always be there for us for all our needs and that shows the strength of our belief in them.”
‘Alleima offered price stability, even during the Covid-19 pandemic’
Kehr also highlights the product innovation they have benefited from over the years through Alleima’s commitment to R&D. “We are well aware that has been a huge benefit of having Alleima as a partner.”
He says he has also been grateful for the price stability Alleima has offered, even during the Covid-19 crisis, steadfastly supporting Aditya Dispomed’s product line, which has allowed the company to build its brand KIATO and grow its reputation. “We were delighted to learn on a recent visit that Alleima now plans to prioritise the medical sector and it will be exciting to see developments in this space in the future and how they will continue to help us achieve our goals.”
Alleima will support Aditya Dispomed launch a number of specialist products in 2024, for different types of blades and as well as a range of microblades. “The core competency of edge, facilitated by Alleima, facilitates our ability to expand into new areas.”
Shailesh Sardesai, Regional Sales Director from Alleima says: “We have been producing strip steel in Sandviken, Sweden for more than 100 years. Our strip steel provides optimal toughness, edge retention, corrosion resistance, a fine-grain microstructure and precision well suited for the challenging, intricate and delicate requirements of medical procedures, like bone cutting, ocular and cardiovascular incisions. “With a fully integrated supply chain from melt to final strip product, the company has an excellent system for controlling process parameters and material properties from coil to coil.”