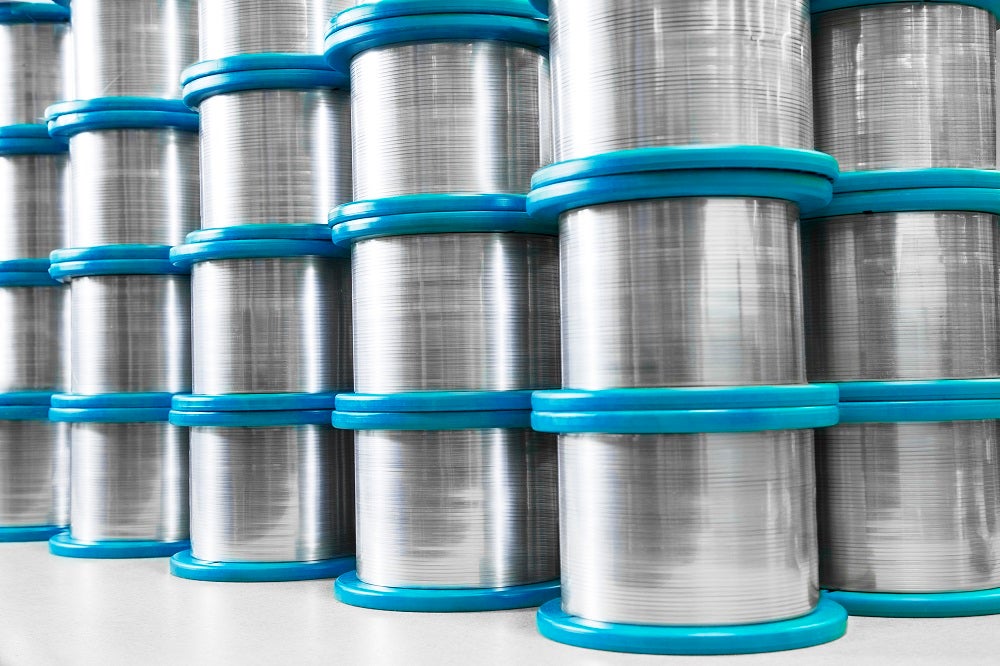
Medical wire has come a long way, with knowledge of metallurgy growing, new processes being developed for precision and even coatings, and advancements in technology calling for smaller and more multifunctional wire components. As such, manufacturers like Sandvik are staying ahead of the curve by continually looking for ways to improve developmental processes and build on their knowledge to work with customers to custom design medical wire components that are perfectly calibrated for the application.
Sandvik medical wire branded EXERA® is packaged and shipped out to countries across the globe. If this is not done correctly, all the hard work put into the wire can be undone. Damage during transit, exposure to corrosion, or wire being too tense on a spool can all contribute to the wire no longer being usable or reducing its effectiveness.
At Sandvik, precision wires are supplied on spools that are enclosed in plastic containers. This is done to protect the wire against mechanical damage and contact with harmful substances in the air.
Spools are typically stored with their axis in a horizontal position. This is because the loose turns on a partially used spool may fall and cause tangles when stood on its end. According to Sandvik, wherever possible, it is also advisable to avoid handling wire on a spool with bare hands, since body acids can cause breakage of wire due to corrosion.
Some wire compositions require specialised care when it comes to packaging. For instance, in the manufacture of wire-wound potentiometers it is essential that the resistance wire should be truly round and have a very clean surface to avoid “noise” at the contact point. It should also have a uniform resistance along its length to give a linear change in resistance with movement of the contact. Both during manufacturing and packaging, every precaution is taken to ensure that the surface is kept clean. Not only does this avoid excessive “noise” but it also reduces contact wear in the potentiometer.
The exact parameters of the packaging and spooling method are something that is discussed with the customer early, and should never be an afterthought. If a braided flat or round wire for applications such as catheters is being ordered, they may need the wire to be fitted on a bobbin that is suitable for the machine that they are using. Sandvik supplies these wires on Steeger bobbins, available in various sizes.
Sandvik provides wire in various forms, including single strand, ribbon wire, multi-filar cables, cored wire, and coiled wire. Each form requires different packaging techniques to ensure that it can be used correctly. One example is coiling wire, which will typically require a larger spool that can hold more and handle the added tension that small wires will place on the drum and flange.
Sandvik offers its wire components on a variety of spool types and sizes, including American standard (with various flange sizes and Anodized Band Spool for bonding wire), metric spools, standard DIN spools, and Steeger bobbins.
Designing and creating a medical wire component that is perfectly tailored to the customer’s needs is the ethos of Sandvik’s business unit medical and EXERA® range. For more information about what Sandvik can do for you, download the whitepaper below or visit their website.