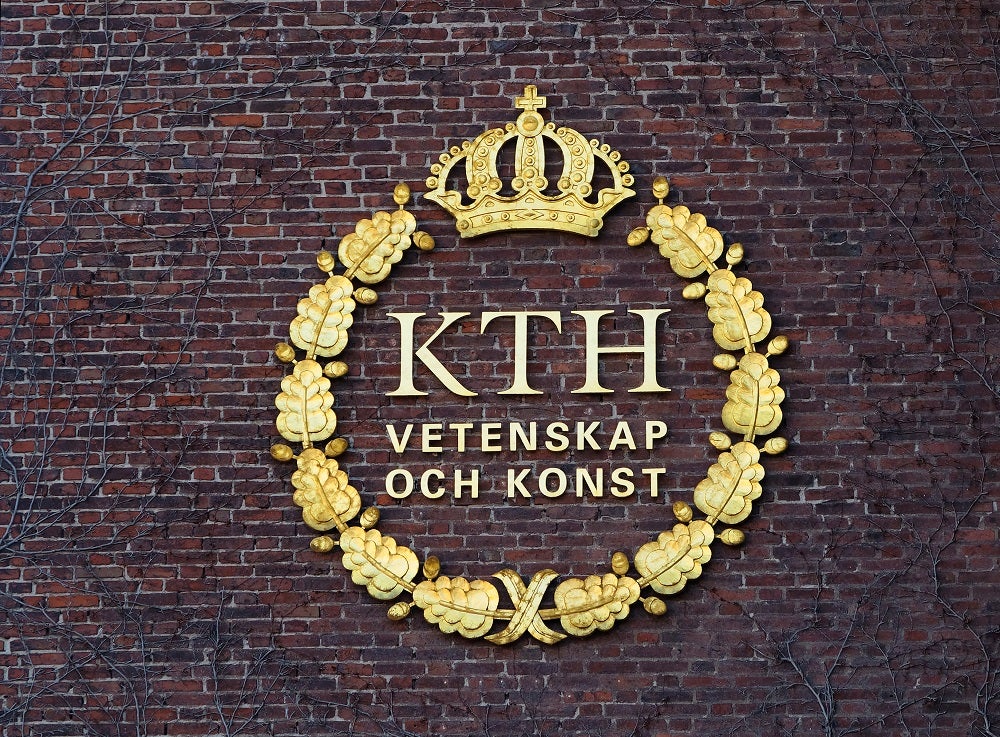
For more than 100 years, Sandvik has been renowned for its stainless steel. To most, the company is best known for its work in the mining and construction industry, but already it is becoming an industry leader with its fine medical wire under the EXERA® brand.
Last year, Sandvik Business Unit Medical began its cooperation with the MedTech Faculty at the Royal Technical University in Sweden (KTH), starting with supporting a master’s student with his thesis regarding “electromagnetic shielding of fine wires for electrophysiological sensing” at the company’s Palm Coast production facility.
Since then, Sandvik has continued its collaboration with MedTech students, including leading a digital booth at this year’s student exhibition. Lena Wiig Boström, marketing communications manager and Katina Whitten, HR manager at BU Medical, hosted the presentation and received excellent feedback from students who had been unaware of Sandvik’s foray into the medical industry.
The Royal Institute of Technology is a public research university based in Stockholm, Sweden, which conducts research and education within engineering and technology. It is currently Sweden’s largest technical university. The MedTech faculty is home to master’s students studying medical engineering, including specialisations in computer science, electronics, or physics, as well as in biomechanics, health systems, or imaging.
Collaborating with students not only supports future engineers with their studies, but it also puts Sandvik at the forefront of future industry professional’s minds. Sandvik builds partnerships with its customers, solving their technical dilemmas that occur when choosing the ideal design for their medical device.
With more than 200 metal alloys to choose from and a specialisation in choosing the best materials and configurations for any given application, EXERA® wire-based components have been used for cochlear implants, pacemaker leads, continuous glucose monitors, tremor control for people with Parkinson’s or epilepsy, catheters, and guidewires. Informing students of Sandvik’s expertise in metallurgy and process development not only welcomes them for support with their current master’s thesis work, but could lead to exciting partnerships for future medical device innovation.
According to Boström: “The main objective of supporting this faculty is to inform them about Sandvik and our medical products and, in particular, our wire-based components, so that when they graduate and get employed at any of the large OEMs they know about Sandvik and our products and can become future customers.”
While the COVID-19 pandemic restricted opportunities to support students in person at their manufacturing facility, Sandvik is gearing up to work with student’s next year.
Sandvik offers made-to-order, build-to-print solutions, which sets them apart from other suppliers, including the capability of producing small batches to be tested during the development phase. Extensive experience in material properties not only allows Sandvik to offer customers expert advice on the most suitable metal materials, coatings, and manufacturing options to reach their end-goal, but also guarantees quality unmatched by the competition.
For more information about EXERA® fine medical wire, including a full list of materials or to contact Sandvik about developing a medical field device, visit their website or download the whitepaper below.