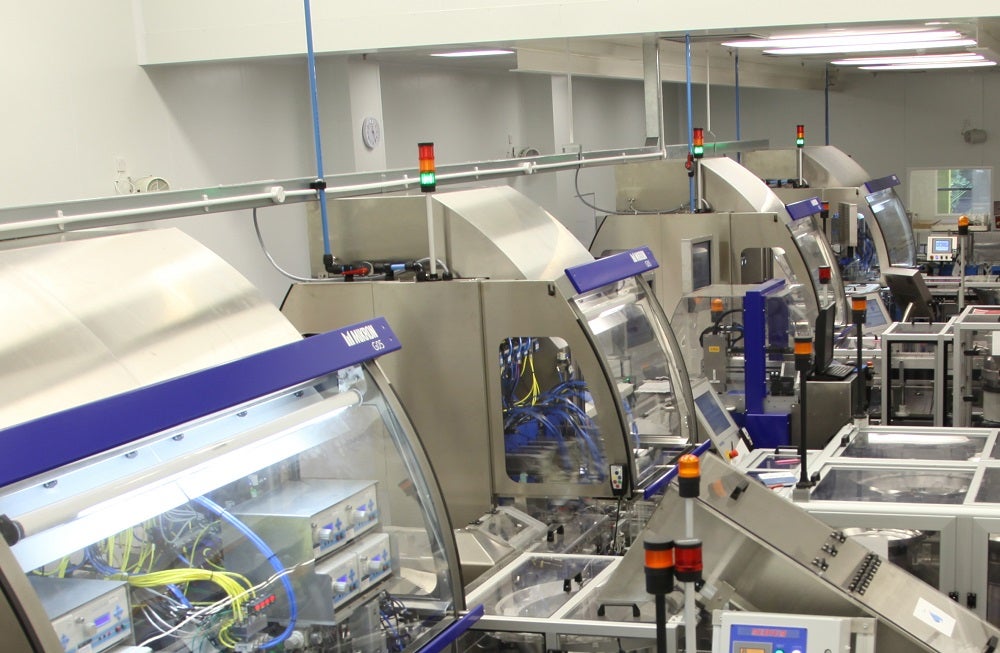
On-body injectors are used in the treatment of diabetes and other chronic diseases. These small injection devices positioned directly on the skin require manufacturers to address several assembly challenges, including the handling and manipulation of the highly miniaturised parts that make up the device, as well as the ability to do simultaneous engineering with customers when the product is still undergoing design changes.
Extreme miniaturisation
Medical device manufacturers design on-body drug delivery devices to be as small as possible. This technology is pushing the boundaries of miniaturisation so the patient can benefit from the device without it impacting their daily life.
Particularly innovative and the subject of numerous patents, this type of device is very complex in its assembly, requiring many parts, some of which are no larger than a few tenths of a millimeter. For example, some silicone seals have an external diameter of less than 1 mm. In addition to their soft and sticky material, their small size makes all gripping, placement and control operations during the assembly process very challenging. The drug delivery needles used in the delivery devices are also extremely thin with an external diameter of 0.3mm. During the assembly process, they have to be bent while ensuring the passage of the fluid. The challenge for manufacturers is to develop a system that can assemble various miniature components that are not all visible to the naked eye.
Pushing the limits
One manufacturer well-versed in the market is Mikron Automation. A leading partner for scalable and customised assembly systems, Mikron has an excellent track record in the pharmaceutical industry, particularly in the complex assembly of delivery devices.. Like auto-injectors, which have undergone lengthy development periods before experiencing a boom in demand in recent years, on-body injectors are still an emerging technology.
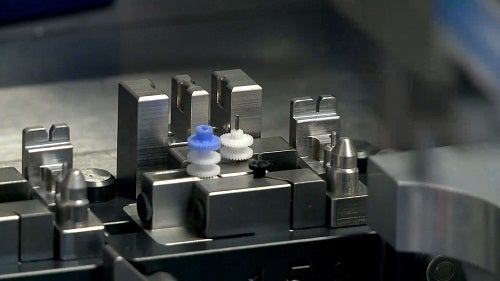
“We began receiving the first customer requests for this type of device in 2013-2014,” recalls Flavio Pointet, key accounts manager at Mikron Corporation Denver, Colorado (USA). “Mikron is known in the pharmaceutical market for the precision of its machines, the quality of its systems and its expertise in complex assemblies. This reputation allowed us to be approached for the first on-body delivery device projects.”
Although Mikron’s expertise was already well established, embarking on the assembly of a new type of highly innovative device is always a challenge. “It required us to go even further in our capabilities to implement miniature part assembly processes in order to be able to achieve these previously unattainable high-precision systems,” acknowledges Jean-François Bauer, head of marketing and business development at Mikron Automation.
“Originally, our automation systems were not deployed to assemble intricate assemblies of this size and precision,” continues Pointet. ” We had to had to perform micro-assembly and micro-adjustment operations that we had never done before.”
Thus, for the design and adjustment of these systems requiring the highest precision, the Swiss company’s engineers and technicians had to use higher resolution cameras and large screens that allowed them to zoom in on certain areas of intervention during the assembly process and make extremely fine adjustments and specific alignments. In the end, the technology deployed was exceptional in terms of precision and assembly efficiency.
Simultaneous engineering
Another challenge for Mikron in the implementation of automation in this field is that it is a rapidly developing market. Few products are currently available and many are still under development. “With this type of device, our support is provided at a very early stage of the project, with products whose development is not yet finalised and which do not yet work in practice,” notes Pointet.
“For the past five years, clients have been asking us for help well before the clinical testing phase. They have a clear idea, prototypes of parts made in 3D printing, but they are still very far from the final product stage.” For this reason, Mikron has expanded its pre-production services to meet some of these specific needs. To demonstrate its ability to perform certain complex operations and assemblies, Mikron provides Proof of Principles (PoP) of certain assembly processes and key operations that can later be integrated into the overall assembly system.
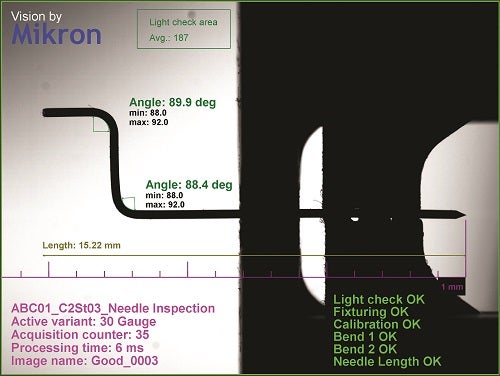
Similarly, Mikron will engage with its partners during their product development phase to suggest design improvements. When performing a DFMA (Design for Manufacturing and Assembly) analysis, Mikron will use its experience to suggest design changes that may improve the assembly process. For some projects, Mikron also provides use of its ISO13485 certification and qualified Class 7 clean room in which device-level tests can be carried out. As a result, the customer’s device is developed simultaneously with Mikron’s assembly system.
A partnership built on trust
For a supplier such as Mikron, being involved in a customer’s project at a very early stage means that a relationship based upon trust must be established between the two parties. “For devices like on-body injectors, on which we are working at a very early stage of the project, it is essential to establish a real partnership with the customer in regard to the technological challenges involved and the financial investments,” says Bauer. “This implies that there is an open communication and a real collaboration between the two partners.
“Very often, clients are developing new products that have a lot of intellectual property. Confidentiality and trust are essential to the success of the program.” Mikron Automation has proven to be the partner of choice, enabling the best risk mitigation for a customer, thanks to the security offered by its process expertise, its corporate culture based on customer success, and its global scale, which enables it to support the challenges of such projects financially.
To find out more, download the whitepaper below.