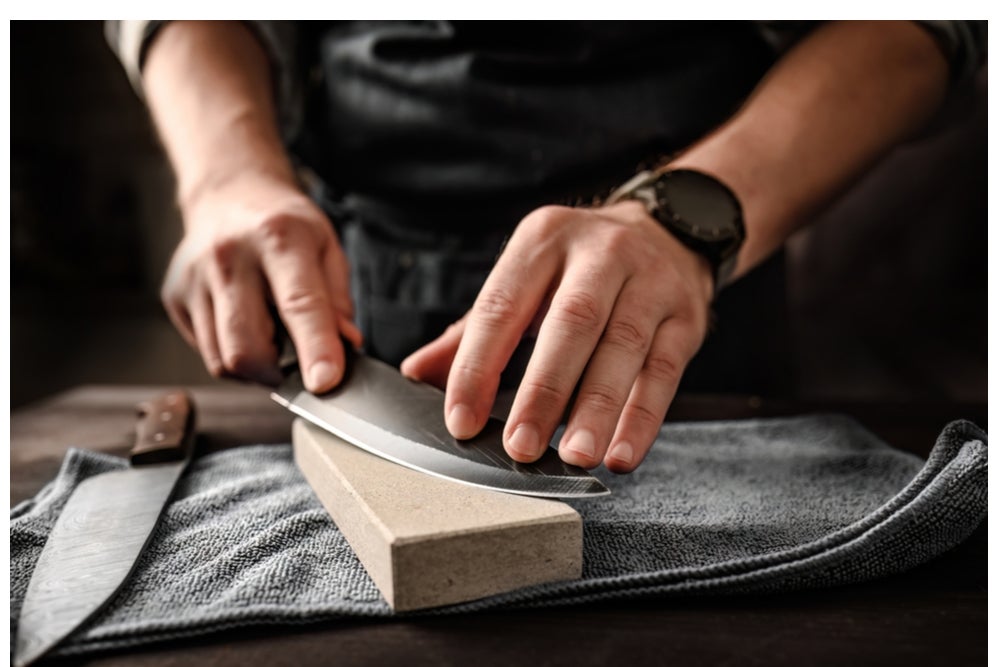
The foundation of high-quality knife steel lies mainly in its microstructure, where complex carbides are present. These microscopic components play a crucial role in shaping the performance characteristics essential for knife applications, for example, the presence of carbides enhances wear resistance in knives, leading to improved edge retention.
More carbides, higher edge retention
The amount of carbides present in the knife steel affects toughness: the more carbides and the larger they are, the lower the toughness. In terms of increasing toughness, the specific type of carbide is less critical, as this has more of an impact on carbide size.
Carbides can impact the knife edge by enhancing or detracting from its retention and sharpness. “A knife edge retention is very much dependent upon the geometry of the edge,” explains Anette Sjöberg, research and development senior engineer at leading producer of stainless steels Alleima. “But carbide content and hardness can have either a direct or indirect impact on the knife edge. In general, more carbides mean lower toughness but higher edge retention.”
As carbides have a higher hardness than the steel matrix, which bonds the carbides together, they directly impact the wear resistance of the steel. “In stainless steel, the carbides predominantly consist of chromium carbide that has a higher hardness than cementite, (a type of carbide found in carbon steels)” says Sjöberg. “Therefore, stainless steels in general have better prerequisites for a good edge retention than low alloyed steel grades.”
The amount of carbides that are dissolved during the hardening process will affect the hardness of the material and the edge retention. “The carbon needs to be in a solution and not locked up in the carbides to contribute to the general hardness of the matrix. For a good wear resistance of the edge, high hardness of both the matrix and the carbides are key,” she explains.
The importance of carbide size
But it’s not just the amount of carbides that are important for the knife steel properties; the size of the carbides also matters.
According to Sjöberg, small and well-dispersed carbides are usually preferred when producing a knife, as this makes it possible to grind a sharp edge. “Higher toughness allows thinner edges in fine slicing knives and better resistance to fracture in heavy-use knives,” says Sjöberg. “They are also easy to re-sharpen”.
“Alleima has a wide range portfolio of steel grades with fine carbide structure, such as Alleima® 10C28Mo2, Alleima® 12C27, Alleima® 12C27M, Alleima® 13C26 and Alleima® 14C28N,” says Sjöberg.
They typically have a maximum carbide size of two microns, while other commercially available knife steels might have large primary carbides that are ten times larger.
When large primary carbides are present, they might reduce edge retention by causing breakouts on the sharp knife edge. “Despite this, the carbides may contribute to increasing wear resistance, so in certain applications, they can be acceptable or even advantageous,” states Sjöberg. One example is Alleima® 19C27, a grade with primary carbides present that can be used in applications with high requirements on wear resistance.
The influence of carbides on corrosion resistance
Carbides themselves do not contribute to a knife’s ability to resist corrosion, but they are still important as they tie up the chromium, (the main alloying element to make the material stainless). When enough of the carbides are dissolved during hardening the chromium (and molybdenum when applicable) is released into the matrix so it can form a protective passive film on the surface.
In terms of corrosion resistance, the size of the carbides counts, as large primary carbides will not be dissolved to the same degree during hardening as small carbides. As a result of this, most of the chromium will still be locked in the carbides, and therefore will not contribute to corrosion resistance.
The homogeneity of the knife steel
The microstructure is the bedrock of a knife’s consistency and reliability. The homogeneity of the knife steel plays a role in providing consistent and reliable properties of a finished blade. A homogenous microstructure is crucial for a consistent hardening result within the knife blade, and to ensure repeatability between different production lots.
Alleima is an integrated manufacturer across the entire production chain of knife steel material. While the process of creating the final strip product is rather complex – from melting, casting and hot rolling to annealing and finishing – it ensures good control of the microstructure. During each stage of production, attention to detail is vital as this minimises variations and ensures a consistent final product for the end-user.
Download this free paper to discover how to source high-quality strip steel for next-level precision.