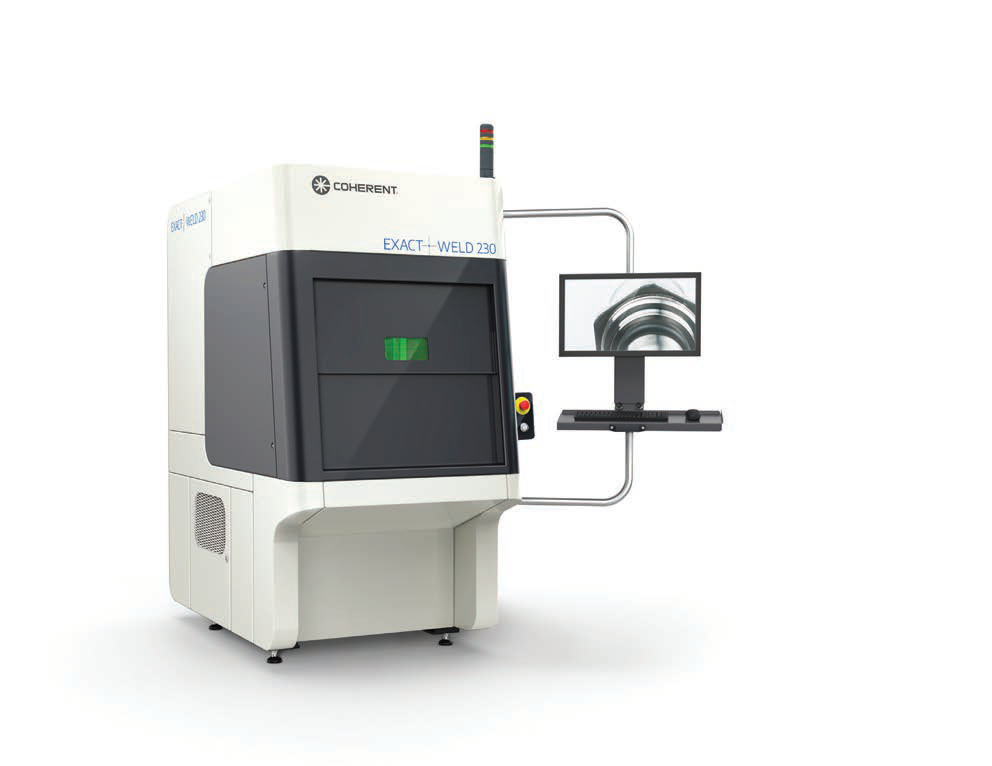
Laser welding machines from Coherent help to cost-optimize the production of endoscopes and other reusable medical instruments – for single unit prototypes under simple manual control, all the way to fully automated CNC production
The Advantages of Laser Welding
Welding of small medical devices with pulsed lasers is now well-established – for both spot welds using isolated pulses, and gas-tight seams using overlapping pulses. It produces superior results and yields compared to traditional methods, which simply cannot match the laser’s ability to provide controlled, localized heating, resulting in a minimized heat affected zone (HAZ). For instance, often no post-processing is required. In addition, laser welding has the advantage of being a reliable method with a relatively large process window that minimizes the hurdles to regulatory approval by the FDA and other regulatory authorities.
Figure 1. MicroWeld enables welding spot diameters as small as 0.1 mm supporting fine welds with minimal peripheral thermal loading.
Today the endoscope welding market is supported by three types of laser-based machines that provide cost-optimized functionality for various levels of the device life cycle. These are economical manual systems, semi-automated tools with motion control, and fully automated CNC-type tools. These enable the welding process to be handled in several different ways:
- Manual welding for very small batch production and high complexity
- Joystick-controlled welding for small batch production and high-precision requirements
- Repeated joystick-controlled welding for medium size production
- Automated, CNC-controlled welding using workpiece fixtures for large batch production, which is supported by process monitoring and image processing.
Economical Manual Welding
Examples of manual welding machines include the Performance series from Coherent. These emphasize simplicity and low cost, because three important functions are all provided by the user. The motion system to move the part is the operator’s hands, the tool’s vision system consists of the operator’s eyes (augmented by a through lens magnified binocular viewing optics), and the operator’s judgement provides the tool’s controller. Laser action is controlled via a simple foot pedal. This combination makes the manual tool ideal for repair, prototypes, low volume production, and R&D applications, and is perfect for complex 3D contours in single unit or low volumes.
While these machines are compact, a simple but extremely important feature is the use of slotted access holes in both the sides and base of the working area. This enables even long (e.g. > 500 mm) endoscopes to be welded inside the compact laser safe working area. With the option of 150 W laser power, these machines can complete single pulse welds on steel parts over 1.5 mm in thickness. Just as important, the focused laser spot diameter can be varied from 0.2 to 2 mm, with an option called MicroWeld™ that enables focus to 0.1 mm for the highest precision and smallest workpieces – see figure 1.
Semi-Automated Machines Bridge the Manual and CNC Manufacturing Domains
A recent development has been the advent of flexible and smart laser welding tools that bridge the manual and CNC-controlled domains. These are very popular with endoscope manufacturers since they are well-suited to the limited batch quantities that characterize the endoscope market, while offering the flexibility for both larger production runs as well as individualized tasks such as endoscope repair. An example is the Select series from Coherent.
Figure 2. Tools such as the Coherent Select series can be operated in three different modes: manual, semi-automated using a joystick to control part motion, and CNC-programmable control via a touchscreen.
These machines incorporate motorized part motion using four precision motion axes, all driven under servo motor control. The tool can then can be operated in three levels of increased automation – see figure 2. In manual operation, the parts are handheld with no setup, learning, or programming required. Under joystick operation, the parts are positioned and moved remotely using the 4-axes motion system; the welding path can be learned (recorded and replayed) to ensure repeatable accuracy. Alternatively, the entire welding operation can be automated using touchscreen programing, teach-in learning based on manual inputs using the joystick control, or data import using CAD/CAM files.
Figure 3. SynchroWeld and LookAhead functions ensure constant pulse-to-pulse overlap around curves and corners, irrespective of motion speed.
These next generation flexible systems are thus ideal for users who want a single system that can support all product stages from R&D through prototyping and then production.
Automated Welding Machines with Enhanced Functions
Fully automated machines are often preferred for volume production of endoscopes and other medical devices. An example is the ExactWeld 230 from Coherent – see figure 4 – which uses the latest 200 W (or 400 W) fiber laser technology, (optional) automatic part clamping, and four axes (x, y, z, C) positioning, user friendly software, and an optional integrated vision system for pattern recognition and alignment. This vision system allows welding with very high precision. And the use of custom, pneumatically actuated, precision part fixturing (including sensors) simplifies ease of use.
This type of high production throughput tool delivers a complete end-to-end production solution, including factory automation/integration capabilities (Industry 4.0/IoT ready).
Figure 4. The ExactWeld 230 from Coherent is a semi-automated machine for welding stainless steel endoscopes and other medical device instruments and implants.
This particular machine also incorporates the Coherent SmartWeld technology which enables bridging larger gap widths by using complex “beam wobble” patterns. This technology also improves weld quality.
Summary
Laser welding dates back decades to the early years of the laser itself. However, it is the advent of tools that package the laser welding technology in an applications-specific format that is really spurring the current growth of laser welding in the medical devices industry.