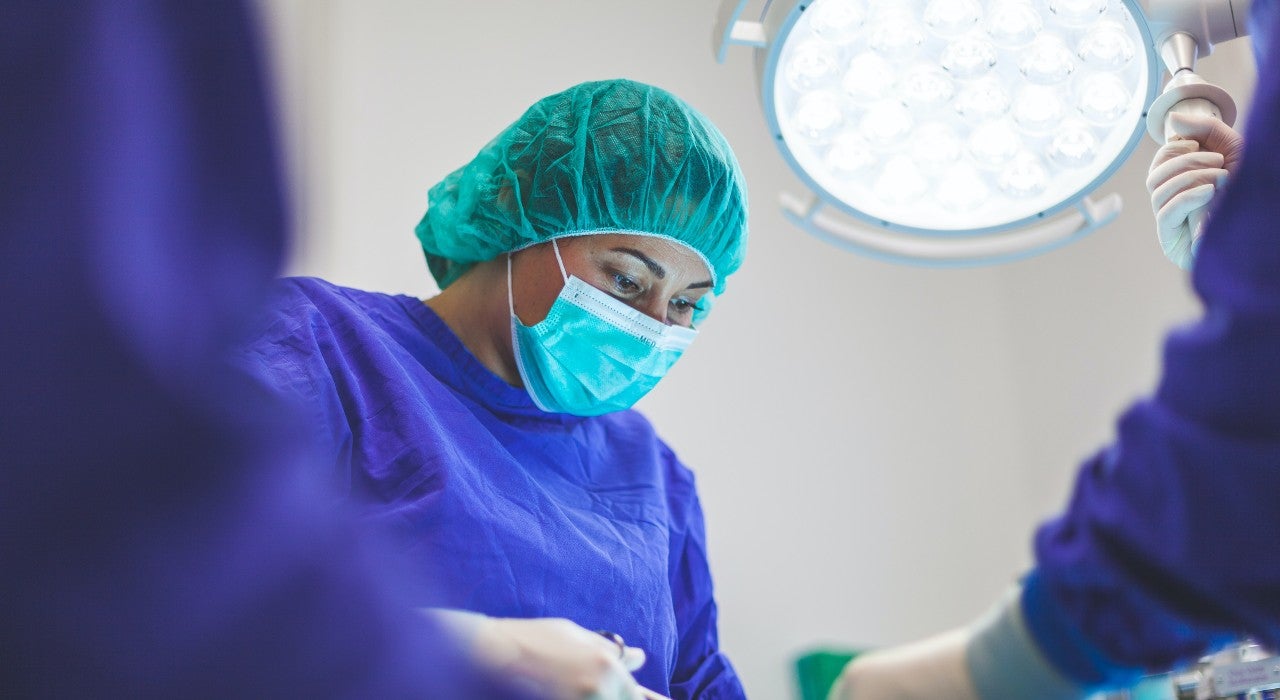
Wire coiling plays a very important role in the manufacturing of catheters – the thin, tubular medical devices used widely in the healthcare industry. Because catheters are inserted into the body either intravenously to deliver fluids and medication into the bloodstream, or via the urethral opening to empty the patients’ bladder, they must be flexible enough to manoeuvre yet firm enough to insert and resist kinking or collapsing during use.
To strike the perfect balance, manufacturers choose a coil-reinforced design whereby a soft medical-grade plastic is used for the catheter’s tube and an internal helical coil spring is added within for reinforcement.
Bob Boldig, president of Custom Wire Technologies (CWT), describes the reinforcement coil’s function as a way of providing “flexible rigidity” to a catheter. “It allows the catheter shaft to be flexible yet resist crushing,” he adds.
Coils also prove essential during the manufacturing of guidewires, which are much smaller devices used to guide catheters to reach a lesion or vessel segment. “Guidewire tip coils provide an atraumatic flexible tip to the wire,” explains Boldig. “Based on material, these can also provide radiopacity if the application calls for it.”
Medical coiling services
Custom Wire Technologies is an experienced producer of medical coils for catheters and guidewires, engineering coils in a range of sizes, lengths, and materials to meet the specific design needs of some of the top medical device OEMs.
According to Boldig, it’s the company’s technical experience that really sets CWT apart in the medical coiling space: “We have been making coils for over 20 years and have seen a multitude of applications using numerous sizes of materials, making thousands of sized and shaped coils. Our manufacturing experience gives us the upfront knowledge as to what works and what doesn’t regarding coil making.”
CWT’s expert team and well-equipped facility enable the Wisconsin-based company to supply OEMs with some of the highest quality medical-grade coils on the market, manufacturing volumes as high as 2,000 units per day.
An ongoing trend in the medical coiling industry is size reduction. Using either CNC point coilers or mandrel winding machines/lathes, the team can manufacture coils as small as 0.001” for the most minimally invasive catheters and guidewire designs.
When it comes to materials, various metals are chosen depending on the final application use and are typically coated with polytetrafluoroethylene (PTFE). In the majority of cases, medical coils are made using 300 series stainless steel (304V). Platinum iridium, platinum tungsten, tungsten, and nickel titanium (known as nitinol) are also used by CWT, with the latter identified as the biggest growth alloy for the company.
Despite the important applications for coils in medical devices, companies trying to source these components are currently plagued by long lead times due to the Covid-related backlogs many large manufacturers are working against. Realising where CWT could help, the company recently leapt into action with its new QwikCoil programme, which promises to deliver quality custom coils within just one week. Even when the coiling industry’s extended lead times return to normal, CWT’s QwikCoil solution will prove highly valuable to the manufacturers that require lightning-fast turnaround on their coiling orders.
To find out more, download the whitepaper below.