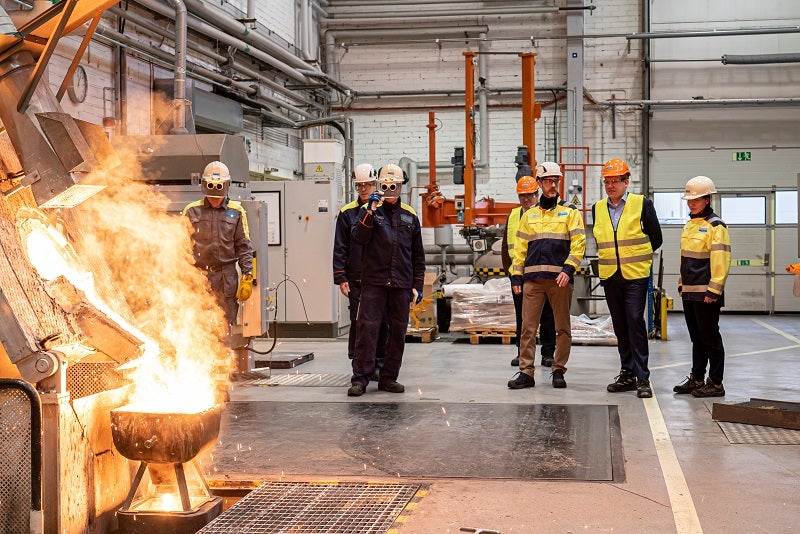
Sandvik’s entrance into the medical devices field was an organic transition after the company was approached by a large medical device OEM that was unhappy with the quality of wire it was receiving elsewhere. With a reputation for manufacturing high-quality ultra-fine wire, the EXERA® brand products and Sandvik’s expert consultancy in wire component development continues to evolve to this day.
When it comes to medical devices, there a number of strict requirements for materials: fatigue resistance, excellent conductivity and non-toxic properties, to name a few. Metallurgy, the science that examines the physical behaviour of metals and mixed alloys, is an essential element of choosing the appropriate materials for the application. Understanding the properties of materials ensures that the safest and most effective combination of metals and surface treatments are selected. Sandvik is no novice when it comes to alloys and steel. Since 1862, the company has been invested in research and development of metal components and developing a relationship with customers.
According to Tom Eriksson, head of Strategic Research at Sandvik Materials Technology: “Cyclic fatigue properties are really important in the medical field, as well as working with the right surface conditions. We can use 150 years of knowledge on the metallurgical side, so customers get the right configurations for their device.
“Our products are designed to last for as long as possible and there are many reasons for that. One is that you don’t want the device to fail or for the patient to need to return for surgery.”
Sandvik’s research and development team works closely with OEM’s and universities, as well as carrying out extensive prototyping of wire components. Working with more than 200 alloys and a number of configurations, EXERA® wire-based components have been used for a variety of applications, such as vascular therapy, biosensing and neurostimulation. Expert metallurgy consultancy has led to the manufacturing of devices including cochlear implants, pacemaker leads, and deep brain stimulation.
“Many of the materials that we use are standard materials that we have adapted to the medical wires, and in some cases, we do modifications to them,” Eriksson explains. “It is about forming partnerships and recommending the best alloys and customisations for what the customer wants to achieve.”
Sandvik’s range of metal materials includes stainless steels (notably, the Sandvik 12R10 medical wire), precious metals (platinum, pure gold and silver), carbon steel (including Sandvik 20AP medical wire),cobalt-chromium-molybdenum alloys (such as Sandvik F562 medical wire), constantan and copper sensor alloys, and Kanthal® resistance alloys (including Nikrothal® 80 and Cuprothal® 49).
Like any field of science, metallurgy is still evolving and seeking ways to build even more effective medical device components in the future.
“Everything is getting smaller,” Eriksson says. “Of course, if you can improve the fatigue properties with a smaller device, then that is more than welcome. In the medical field, we are finding more and more ways that diseases can be treated using medical technology, and as that research is ongoing we will continue to find ways to meet those needs.
For more information about EXERA ® fine medical wire-components, including a full list of materials or to contact Sandvik about developing a medical field device, visit their website.