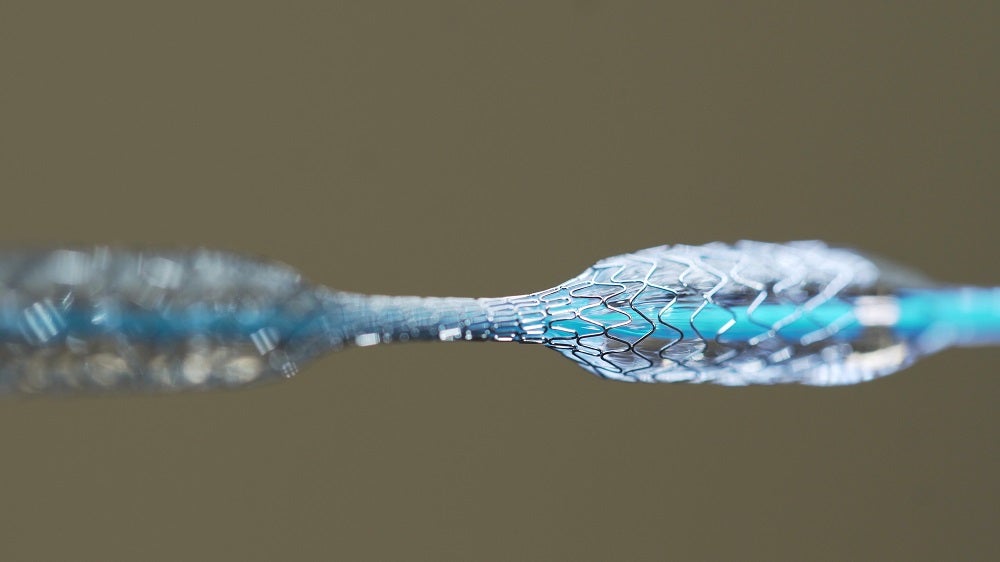
Metallurgy can be a complicated balancing act in the medical technology field, with device manufacturers needing to find the right combination of properties for their application, in addition to requiring biocompatibility.
From stainless steel to copper-based alloys and gold plating, the list of metal materials used in medical devices is an extensive one, so what makes nitinol so special? Offering unique properties such as shape memory, super elasticity, biocompatibility and fatigue resistance, nitinol has consistently been the answer where cheaper options (such as stainless steel), have failed.
Biocompatibility for instruments and long-time implants
Nitinol is a combination of approximately 50% nickel and 50% titanium, although this differs and each alloy is named according to the weight percentage of nickel. Despite nickel being toxic, nitinol is highly biocompatible due to the titanium oxide layer.
“Biocompatibility is extremely important for implants, but also instruments,” says Bernd Vogel, founder of leading manufacturer of nitinol components, Endosmart, which was acquired by Alleima at the end of 2022. “If you do the right service finishing, you will increase that further, so it’s no problem to have nitinol as a long-term implant.”
The company designs and develops nitinol components, as well as complete finished products. This was one of the reasons why Alleima and Endosmart agreed to merge and continue developing advanced components for the medical devices of the future together.
Shape memory
Nitinol’s shape memory allows it to undergo deformation at one temperature, stay in its deformed shape, and recover its original shape after being heated above its transformation temperature.
According to Vogel: “Nitinol can be used for medical instruments that have to be shaped to the anatomy of the patient. Normally, when you have a stainless-steel instrument, you need to have maybe ten different angled instruments, but with nitinol you only need one instrument bent to the angle needed for the operations. Afterwards, during the sterilisation process, it goes back to the straight instrument ready for the next surgery.”
Super elasticity
Above its transformation temperature, nitinol will behave super-elastically. This means that it can undergo significant deformations and immediately return to its original shape once the external load is removed.
“The super elastic properties don’t need heat. You constrain, you crimp, you pull through a tube. Then you push it into the body,” Vogel explains. “The system of tubes in the body is very complicated and very long, and we don’t want to cut open the body until we get to the point of interest. We want to go endoscopically. That’s why endoscopic instruments are getting small in diameter, longer, more flexible, and softer.”
Crimping is an effective joining technique for nitinol wire, meaning it can be connected to other nitinol components or different materials (such as stainless steel).
“The next generation will work with soft endoscopic robotics, which go deeper in the body, and there you have to use flexible instruments,” Vogel adds. “This is our field, we can crimp our devices and apply them to these robotics and then they open in the point of need. This is where you need super elastic properties – stainless steel can’t do that since it is too rigid, and the elastic properties are far too low in order to fulfil these needs.
“It’s the same with implants. You want to apply them through a very small catheter; a very small in diameter application system. Then they should open up 20, 30 times bigger when you apply it, therefore, you need extremely high super elastic properties, as well as a stable and stiff implant. These are exactly the properties nitinol offers.”
For more information about nitinol or medical materials, visit Alleima’s webpage Fine medical wire in a wide range of alloys — Alleima