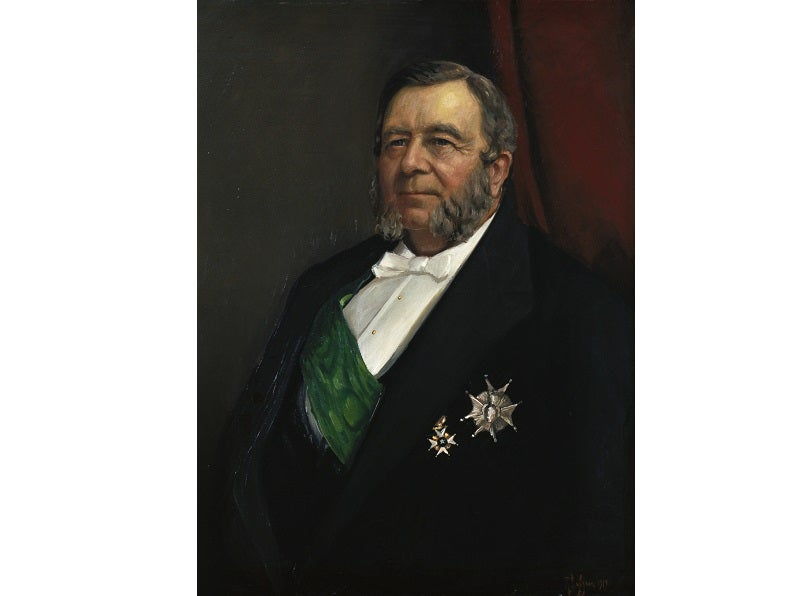
Perfecting its expertise in steel production since establishing in 1862, Sandvik has forayed into the medical devices field in recent years. Harnessing its skills to manufacture high-quality fine wire and wire-based components used in medical devices, Sandvik then launched its EXERA® brand in 2016.
Sandvik has been leading steel innovation from the start. Founded by Göran Fredrik Göransson in 1862, they were the first company to successfully use the Bessemer method for steel production on an industrial scale. Since then, their focus has remained the same: high-quality, investment in research and development, and a close relationship with customers.
Innovators in stainless steel
Today, Sandvik Group encompasses three business areas that conduct operations such as R&D, production and sales for their respective sectors. These are Sandvik Machining Solutions, Sandvik Mining and Rock Technology, and Sandvik Materials Technology. The EXERA® medical wire brand falls under material technology, in which the company also offers micro-tubes and strip steel for other medical applications.
Sandvik Materials Technology is best known for its duplex stainless steels. The manufacturing of stainless steel began in 1921, and since then the business area has worked hard as an innovator to manufacture steel products for a vast array of industries and applications.
Sandvik 3RE60 was developed in the 1960s to combat common issues in steel production. It was one of the first commercially successful duplex stainless steels and is still used today. At the time, austenitic steel was vulnerable to stress corrosion cracking, which was only tackled by adding nickel. Alternatives, such as ferritic steel, are resistant to stress corrosion but are brittle and difficult to weld. Sandvik’s 3RE60 steel combined the best of both worlds.
Since entering the medical devices field, Sandvik’s history and expertise in stainless steel has been invaluable. The EXERA® medical wire is manufactured from stainless steels, precious metals and biocompatible alloys, creating customisable high-quality wire. Sandvik’s ability to develop custom designs to meet customer’s goals is already setting them apart from the competition in the medical devices field.
Where does Sandvik stand in the medical devices industry?
Key figures from 2019 tell us that Sandvik Materials Technology generates the most revenue from the energy sector (44%), followed by engineering (21%), consumer and electronics (12%), automotive (6%), chemicals (6%), aerospace (3%), construction (3%), and other industries (5%).
Sandvik has already grown as a specialist in materials and configurations for medical applications such as vascular therapy, sensing and neurostimulation. They are a member of IVAM (a global association of companies and institutes specialising in microtechnology, nanotechnology and advanced materials for the medical industry) as well as a member of Swedish Medtech.
Working closely with customers, Sandvik forms working partnerships with medical device developers to choose the best materials, drawing on unique expertise in molecular technology and extensive insight into industrial processes to ensure that customers meet their goals.
Social responsibilities
Sandvik are set to be thought leaders in material development. Utilising their expertise in stainless steels, special alloys, titanium and zirconium, their online technical centre offers free access to material datasheets, corrosion tables, and other useful information.
Sandvik is heavily involved in the community, including engagements such as ‘Engineers without Borders’, which improves education quality across government schools in India; the Sandvik India Gender Awards which supports gender equality and inclusion; working with the Swedish Vasa museum to provide more than 5,500 bolts to restore the old wooden warship; and working with programmes to combat HIV/AIDS.
Today it is more important than ever to focus on sustainability, and Sandvik is doing just that. As part of their sustainability goal for 2030, Sandvik aims to achieve 90% circularity, halve their CO2 impact, increase their focus on health and safety, and provide transparency in all of their operations and goals.
In fact, in 2018, Sandvik was recognised as part of the Global 100 Most Sustainable Corporations in the World by Corporate Knights. The Sandvik Sustainability Award in Memory of Sigrid Göransson, the founder’s granddaughter and an advocate for improving housing, welfare, schooling and health care, will be awarded in April 2020.
Sandvik utilises secondary raw material (“scrap” steel), with its overall circularity currently standing at 84%. To boost this to 90%, Sandvik are working with AI experts to better determine the distribution of compositions in internally recycled material to increase how much can be re-used. More information can be found here.
Listen to Sandvik’s podcast about their history and material development or access their technical centre here.
For more information about Sandvik Materials Technology and the EXERA® brand or to contact them about forming a development partnership, visit their website.