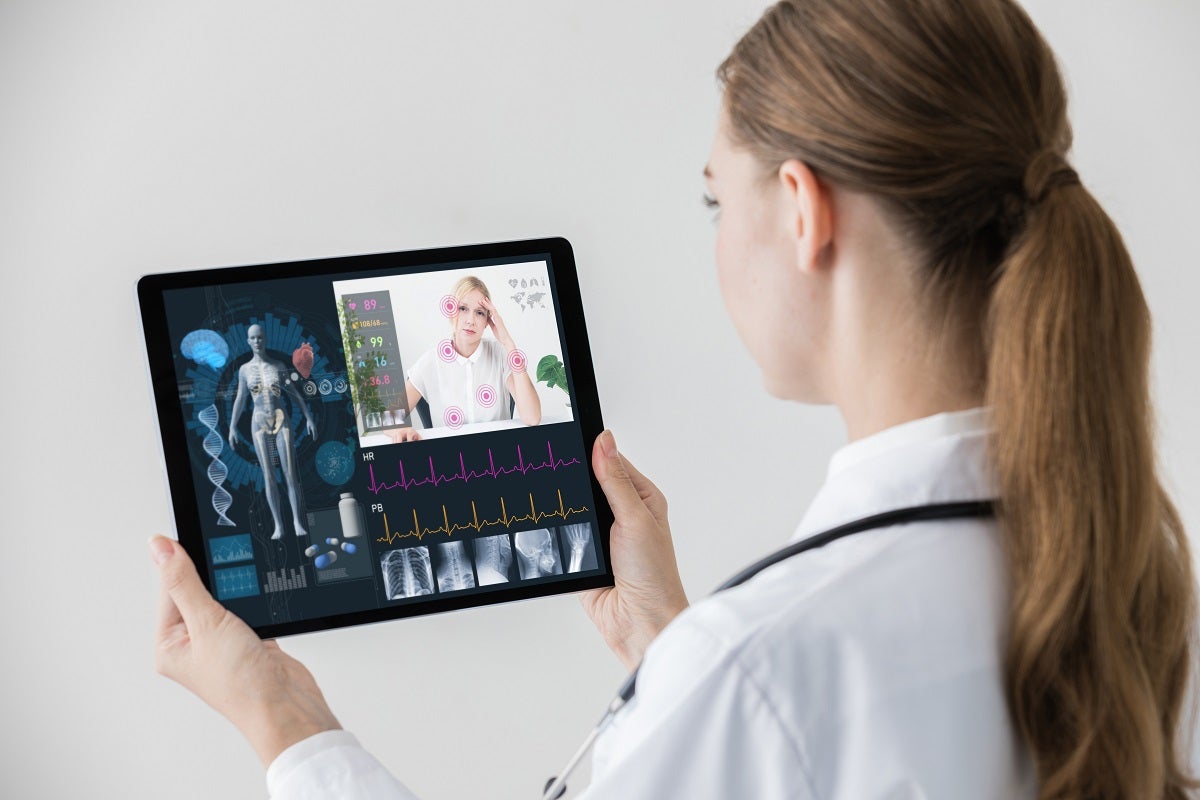
With technology ever-changing, medical devices are getting smaller and more advanced, and manufacturers must stay at the forefront of these innovations to maintain a competitive edge in a saturated market.
But rapid advancements don’t just spell benefits for business. In improving medical devices, patients are given access to products with a host of quality-of-life improving features. For example, certain recent technological advancements mean that a medical device can often replace clinical visits, allowing patients to better manage their health at home through the advent of remote monitoring.
Internal use of glucose monitoring, for instance, allows measurement of glucose levels via a chemical reaction under the skin that turns into a signal sent to a receiver outside the body. Diabetic patients can track their blood glucose levels in real-time on their phones. To make sure they stay on top of their health, a warning will go off if their blood glucose levels are too low or too high.
Patients who suffer from serious health conditions can benefit from this innovative technology, allowing them to live freely while still maintaining their health. This eliminates the hassle of keeping up with appointments.
However, when designing and building these medical devices, manufacturers need to pay close attention to every wire and coating used to ensure the device is as efficient and reliable as possible while keeping costs effective.
Manufacturing challenges
A lot of therapeutic devices rely on medical wire components, from pacemakers to catheters to glucose monitors. In addition to transmitting, sensing, and stimulating signals within the body, these devices must be biocompatible and offer a range of other features, such as lubricity, conductivity, and fatigue resistance. As well as choosing the right metal, manufacturers need to decide what type of coating to use so that the precise coating thickness matches each customer’s needs.
Sandvik, a leading multinational engineering company, recently held a webinar where viewers were asked: what are the most frequent issues in the design phase? 20% of respondents stated that a common issue was meeting deadlines due to lack of resources, while a further 20% suggested a lack of materials and coating knowledge in-house. Notably, 60% of respondents said that the most frequent design issue for them was simply finding the right coatings.
Medical device markets
In the past, biocompatibility and cleanliness ruled the metallurgy of metals used in medical applications, but now physical metallurgy is taking over. The growth of a metal known as nitinol over the last 20 years has been impressive.
Nitinol is what is known as a shape memory metal. This phenomenon, which enables it to remember its original shape, can also result in a metal that shows “super elastic” properties. This is a big deal for medical applications because most metals are far more rigid than body tissue and bone. Usually, metals will bend permanently when you deform them more than 1%, but nitinol can be bent more than 6% and still return to its original form.
What makes both the shape memory effect and super elasticity possible is the change from an austenitic crystal structure to a martensitic one and back again because of applied temperature or strain depending on what temperature the phase transformation from austenite to martensite takes place. Shape memory and super elasticity make nitinol particularly suitable for a variety of medical devices and deployment equipment as well as for some orthopedic implants.
Small-batch prototyping
Sandvik and EXERA®, its flagship brand, offer over 200 alloys, with special alloys made on demand. With its R&D team, Sandvik develops materials that are suitable for any application. When it comes to nitinol, today, the company only coats metal wires in sizes 0.12 mm to 0.20 mm. For their medical devices, the company uses polymer materials like synthetic resin-based coatings, self-bond thermoplastics, and high-performance polymers.
Unlike other medical wire manufacturers, Sandvik also offers small-batch prototyping to help original equipment manufacturers find the best possible components for their devices without wasting parts. The company’s prototyping capabilities have been boosted further with the acquisition of Polyfil, which provides 3D visualisations that can be injection molded, as well as create 3D printed prototypes. To find out more about medical alloys, download the whitepaper below