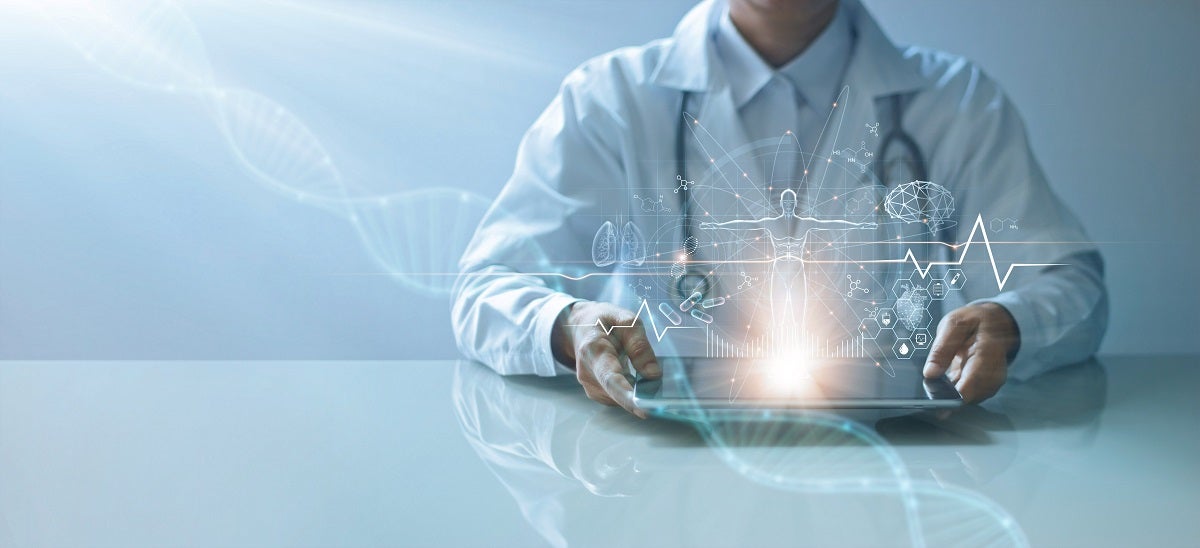
All medical device manufacturers share a common goal; protecting the lives of patients and ensuring quality of life, something that is reflected in the exciting innovations that the industry has seen in recent decades. Medical devices are getting smaller, less invasive, more efficient, and part of our digital age, and manufacturing methods have developed to meet demand.
As devices get smaller and smarter, manufacturers need much finer wire that still has the appropriate strength and fatigue resistance, as well as requiring much more advanced sensing and transmitting capabilities. Medical wire component manufacturer Sandvik works continuously with OEMs and universities to make the future of medical devices possible, from improving polymer coating methods to expanding our knowledge of metallurgy. But what are the future trends that we should be looking out for?
Traceability with RFID tagging
“A lot of the devices that are now being used have some kind of RFID included so that information can be transmitted easily, and the location of a medical device can be tracked,” explains Gary Davies, head of Sandvik Business Unit Medical.
By 2022, the value of the global RFID in healthcare market is expected to be worth $4.9 billion. RFID is already being used for inventory management, and for medical devices this means that they can be tracked from the manufacturing stage. This way, information such as lifecycle, sterilisation and maintenance requirements can be monitored. RFID tagging can also allow physicians to access important patient medical records with a scan, preventing the risk of records getting mixed up or incorrect treatments being administered.
Going remote
Remote monitoring enables patients and healthcare workers to monitor their health efficiently without the need for unnecessary hospital and clinical visits or invasive tests. Remote devices send data to a computer or mobile device where it can be checked, and healthy reading parameters can be set for automated alerts if the patient becomes ill.
A key example of a common remote monitoring device is a glucose monitor, which have changed the lives of patients with diabetes across the globe. Patients no longer need to perform prick tests throughout the day, and they can be immediately alerted should their glucose level fall outside of healthy parameters.
This technology is lifesaving as it enables much faster intervention than manual checks. For people with conditions such as diabetes or heart problems, remote monitoring not only gives them more freedom, it gives them peace of mind by enabling preventative, not reactive, healthcare.
Automated manufacturing
“We adapt our equipment to automate processes wherever we can. The main reason for this is creating much more repeatable processes and therefore a reproducible product, which is key for medical device manufacturing,” Davies explains. “In some cases, in order to hit the tolerances that we need for certain applications, it’s simply too precise for a human to do manually.”
Smaller devices require fine wire with extreme precision, and automated processes enable complete uniformity. More than ever before, finer wire does not mean sacrificing strength or fatigue resistance.
3D printing and prototyping
Unlike many other medical wire manufacturers, Sandvik offers small batch prototyping to help OEMs find the best component for their device without producing waste. Its prototyping capabilities have been further expanded with the acquisition of Polyfil, enabling 3D visualisations that can later be injection moulded, as well as 3D printed prototypes.
Overall, more efficient design and manufacturing processes produce a superior product quicker and more sustainably. For more information about Sandvik Materials Technology’s medical alloys and the EXERA® brand or to contact them about forming a development partnership, download the whitepaper below.