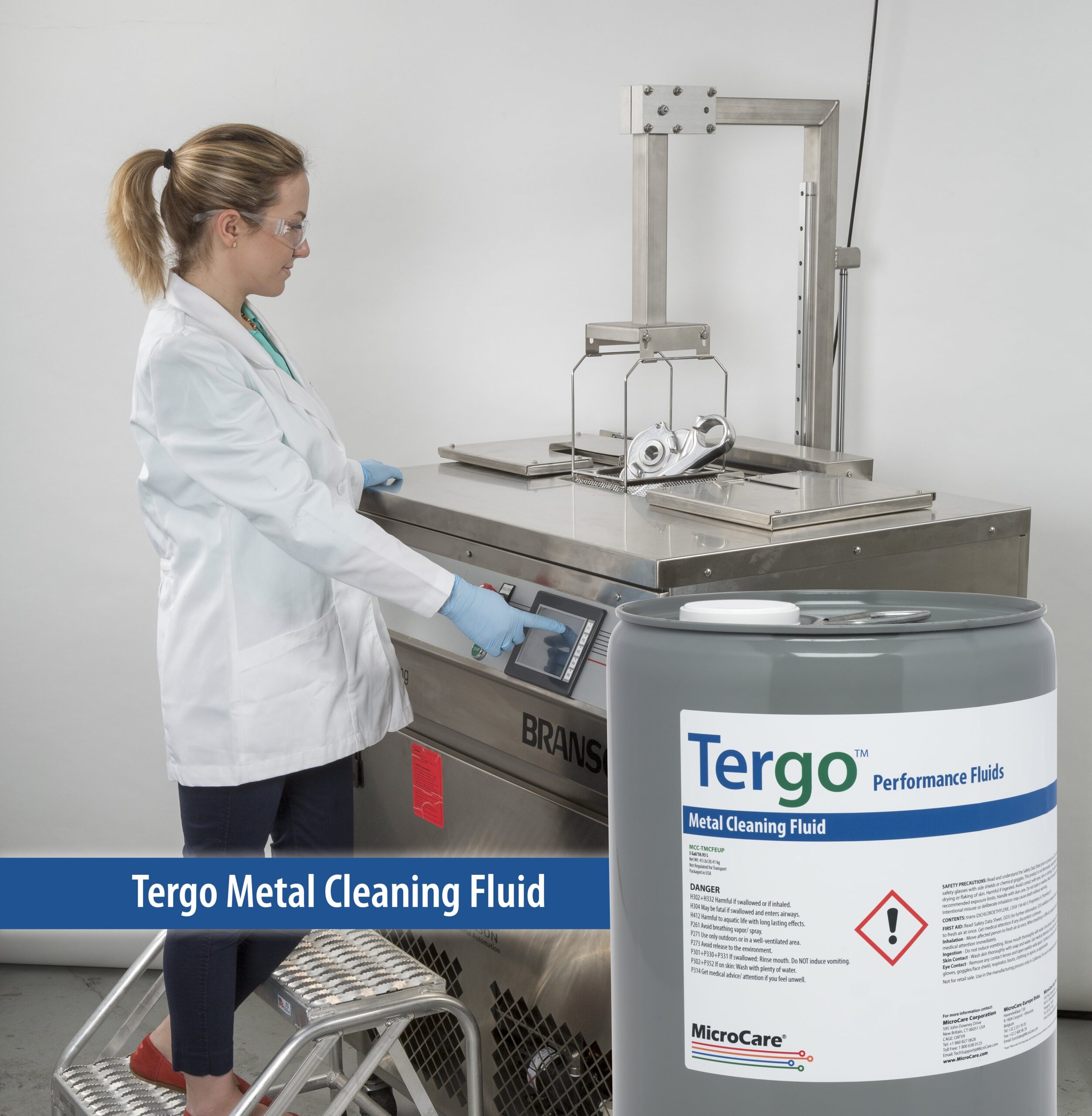
Cleaning is an important step in medical device manufacturing. Whether it is production of high-reliability medical electronics (which often includes dense circuitry within very small, complex packages) or multifaceted assemblies with intricate shapes and delicate parts, all must be cleaned to meet reliability and quality standards.
For many companies, validated cleaning processes are already established. However, more governments and regulatory agencies around the globe are now requiring greener chemistries and manufacturing processes. For some fabricators this means their well-established vapor degreasing cleaning fluids are no-longer suitable. They must seek out new alternatives to ensure they continue to clean effectively, but also meet the new emerging regulatory requirements, for both now and into the future.
What’s Out?
Today, medical device makers must minimize negative environmental impact, conserve energy and protect natural resources. All while still efficiently producing their devices and maintaining the health and well-being of their employees. Finding a cleaning solution that meets all the criteria of sustainability, performance and safety is difficult, particularly as new environmental rules and requirements emerge.
For example, nPB (n-propyl bromide) is widely used as an effective and reliable medical device parts cleaner inside a vapor degreaser. Over the past 30 years, nPB replaced other environmentally-questionable chemistries such as CFC-113, methyl chloroform, hydrochlorofluorocarbons (HCFCs) and perfluorocarbons (PFCs) which are found in many cleaning solutions.
nPB however, is now under review by the U.S. EPA (Environmental Protection Agency), OSHA (Occupational Health and Safety Administration) and ACGIH (American Conference of Governmental Industrial Hygienists). Its use as a parts cleaner is under scrutiny and the restrictions around it continue to grow.
nPB is not the only solvent of concern. Others in question include perchloroethylene (Perc) and trichloroethylene (TCE) which are currently banned or restricted in some countries. In the U.S., the EPA added TCE and Perc to their environmental watch list. This means they will likely need to be replaced with greener alternatives. Device fabricators are now faced with finding replacement fluids that must not only meet regulatory demands, but also provide reliable and consistent cleaning in their existing vapor degreasers. Most significantly, the new cleaning fluids must also be safe for worker health and the environment in which we live.
What’s New?
The use of sustainable cleaning fluids and methods plays an important role in meeting this new sustainability challenge. But what is the alternative to outdated brominated and chlorinated solvents, like nPB and TCE that contribute to ground water and air quality or worker safety problems?
One solution paving the way for sustainable cleaning is modern vapor degreasing cleaning fluids. These new cleaning fluids not only comply with strict new environmental regulations, but are lab-tested and analyzed to ensure the cleaning results are reliable, consistent, and just as good, if not better, than the legacy cleaning fluids.
Outstanding Cleaning Performance
Modern vapor degreasing fluids effectively dissolve contaminants including machining and stamping oils and thick grease. Also waxes, baked-on resins, corrosion protection agents and esters. They also remove soils like drawing compounds, spinning lubricants, buffing compounds and fingerprints from a range of materials including stainless steel, copper, brass, aluminum, nylon, polyester and polyethylene without damage.
These fluids are engineered with the correct characteristics such as high densities, low surface tensions, and low viscosities to wet every surface. This means they penetrate the most complex shapes, including inside blind holes and end holes to completely dissolve contaminants and remove the most stubborn particulate. The new fluids are also low-boiling, so parts come out of a vapor degreaser clean, dry, spot-free, and cool enough for immediate processing or packaging.
Better for the Environment
These game-changing cleaning fluids use HFO (hydrofluoroolefin) chemistries. This means they are environmentally sustainable with a low GWP (Global Warming Potential). The GWP of a cleaning fluid is a measurement of the atmospheric lifetime of the fluid or its gaseous vapors. The longer a trapped gas absorbs infrared radiation in the atmosphere, the more it may contribute to global warming and climate change. The lower the GWP number, the more climate-friendly the substance. The new cleaning fluids typically have a low GWP of 3 or less. By comparison, the older solvents used in cleaning fluids, like HCFCs (hydrofluorocarbons), had average GWP ratings in the thousands. Additionally, the Ozone Depleting Potential (ODP) ratings of many of the new sustainable cleaning fluids is zero, meeting all strict air quality emission regulations.
A Greener Footprint
Many of the sustainable cleaning fluids have a low boiling point and heat of vaporization. This translates to less energy use, resulting in energy cost savings. It also cuts overall fossil fuel consumption resulting in a lower total carbon emission and less greenhouse gas output. Vapor degreasers also use no water, therefore conserving this vital non-renewable resource.
Plus, a vapor degreaser is not only a parts cleaner, but also a continuous recovery and recycling system. The vapor degreaser has two chambers: the boil sump and the rinse sump. In the boil sump, the cleaning fluid is heated and parts are immersed and cleaned in the fluid. Once cleaned, the parts are mechanically transferred to the rinse sump for final bath in a pure, uncontaminated fluid. The cleaning fluid condenses and drips back into the vapor degreaser, from which it can be reused for many hundreds of times before requiring refreshment or replacement. It does not produce wastewater—which must be filtered, distilled, deionized, and osmosis prepped prior to disposal. The vapor degreaser simply concentrates the soils as it works. This reduces waste generation and lowers hazardous waste disposal costs.
What About Worker Safety?
When looking for sustainable long-term cleaning solutions, a top priority is always worker safety. Supporting worker health and safety with greener cleaning is paramount. It is important to eliminate chemistries that could be harmful, or are on the list of those under scrutiny, and replace them with a better alternative.
Next-generation vapor degreasing fluids are both environmentally better and safer for people. The properties of new cleaning fluids ensure they are compositionally stable and non-flammable to improve workplace safety. Furthermore, many of the substitutes for nPB, PERC, or TCE have improved HAP (hazardous air pollutant) and human toxicity profiles and higher, better PELs (Personal Exposure Limits) than legacy solvents.
The OSHA-designated time limit or PEL that workers are exposed to a chemical is far more acceptable for sustainable cleaning fluids than hazardous legacy solvents. The higher the PEL number, the better. The usual PEL for sustainable fluids is 200-250 ppm (parts per million). When compared with TCE which has a 100-ppm PEL or nPB which is rated at just 0.1 ppm by the American Conference of Governmental Industrial Hygienists it is obvious to see the worker safety advantages of modern cleaning fluids.
When to Change
In Europe, both TCE and nPB are banned for industrial cleaning use. Canada has also severely restricted their use and many other countries are likely to follow. In 2020, the US EPA announced nPB and TCE present an unreasonable risk to human health when used as a cleaner inside all vapor degreasers including open-top, in-line, and closed-loop models. Today, it is unknown exactly when a complete nPB and TCE ban will happen in the U.S., but many experts agree an eventual ban is certain and coming soon. So, it’s important that medical device fabricators using these legacy solvents for cleaning start to explore alternative cleaners. By taking action now they can ready themselves to comply with not only current regulations, but also prepare themselves to meet any additional regulations established later.
MicroCare Can Help
Medical device manufacturers must not only meet customer expectations and production requirements, but must also be ethically and environmentally responsible. Fabricators must decrease emissions, improve energy efficiency, protect natural resources, reduce waste, and protect their workers’ health and well-being. The objective is to meet today’s short-term goal of commercial success without overlooking the long-term impact operations might have on the workforce and planet.
MicroCare can help if you are ready to change to a more sustainable cleaning fluid. The MicroCare team of cleaning engineers, chemists and technical experts have hundreds of years of combined critical cleaning fluid and vapor degreasing experience. They can help you convert to safe and compliant cleaning fluid that meets sustainability standards now and well into the future. Schedule a consult to get started today.