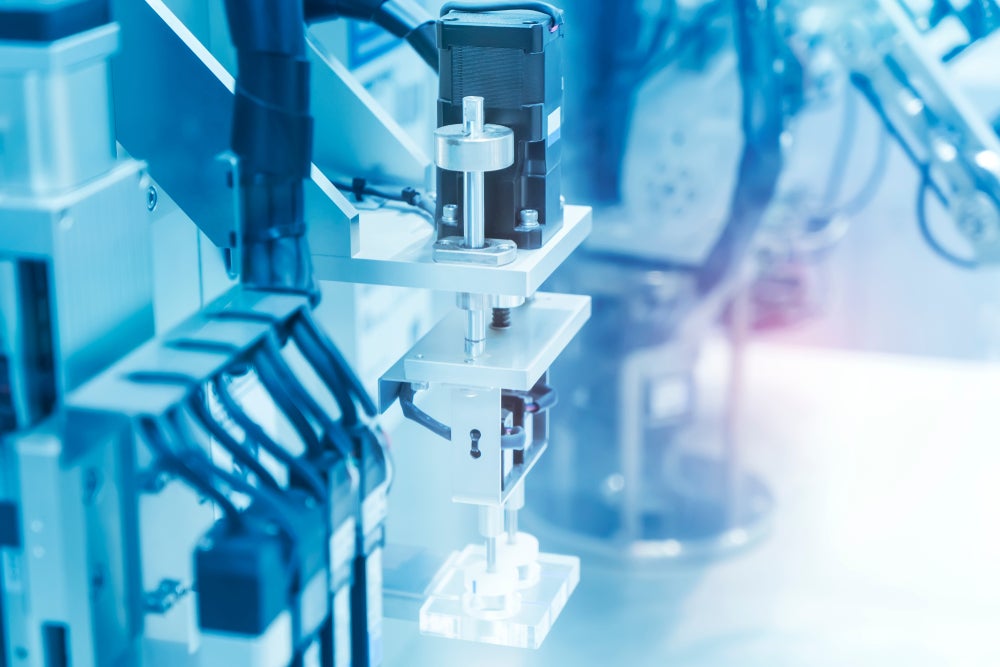
In the era of rapid medtech innovation, the demand for smarter and more resilient medical devices requires more advanced types of coatings. In a report by GlobalData, Thematic Intelligence Predictions 2023, in-vitro diagnostics and cardiovascular devices are projected to be the biggest medical device markets by 2023.
To keep up with the fast-developing field of smart medical devices, US-based company Formacoat is leading the way. The specialists in medical device coatings have a simple mantra: There are no bad coatings. You just have to find the one that works best for your business.
“Over the last 20 years, that’s why we’ve developed relationships with all these different coating vendors. We learnt how their coatings work, and how they can function. Can you do different things with them? Can you take a hydrophilic coating and combine it with an antibacterial additive to give you something that’s slippery and also helps fight infection? And the answer is ‘yes’. That’s why experimentation with coatings is so important. It’s in Formacoat’s DNA,” says Todd Paulsen, vice president of Formacoat.
The willingness to explore all the possibilities in the world of medical coatings sets Formacoat apart from its contemporaries. “Ours is an experimental platform through which you can build your device kit to its ultimate level of functionality. However, for a lot of people, that is a scary investment because experimentation takes time. Most people are not pushing the envelope and are just trying to sell what they have in order to maintain what they’ve got,” adds Paulsen.
How the Formacoat Formula speeds up coatings innovations
Building robust R&D processes is crucial to support continuous experimentation in this field. Exploring advanced chemistries and tailoring medical coatings that enable devices to function more efficiently requires collaborations across departments.
According to Paulsen, the ‘Formacoat Formula’ involves having a deep understanding of the client’s needs by asking two simple questions to them: ‘What do you want? And why?’
“We’re not doing the same thing over time. Our experimental teams work together to resolve crazy problems. Whether it be through chemical experimentation in science, laboratory work or whether it be through engineering and application design and fixture creation. It allows us really to be a very creative force when it comes to that,” says Paulsen.
“We’ve got a full staff of people that can push through this experimental processing to get people the answers they need in a very short amount of time by focusing on their problem and borrowing from our 20 years of experience. The customers appreciate that. We’re still we’re not a big company. We’re not a small company. But we’re very nimble in that we can bounce back and forth and keep all of our customers happy while doing the fun experiments.”
Despite its reputation for taking on complex coating projects, Formacoat believes in being honest with its clients. If an application design presents problems the company cannot provide a solution for, they will let the client know upfront to save time and build trust.
Building coatings quality and increasing market entry speed
To facilitate a vibrant research culture and serve its growing customer base, the company has scaled up operations in a new facility devoted to commercial-scale contract coating operations. This move has allowed the brand to expand and utilise its in-house technology such as Formacoat’s new roll-coat machine, built by the R&D and engineering departments to increase production capacity and speed.
Most of the applications are custom-built using the company’s vast expertise in offering an array of specialised coatings. These revolutionary application methods to develop coatings for devices not only ensure the optimum solution but are also effective in lowering costs for customers.
Formacoat recently completed designing the Gen-3 coater, which is not only faster than their previous setup but can also control different aspects of quality assurance, like the amount of coating needed for the devices, with the help of a camera system.
“It can verify that the device has been coated according to the required specifications. This machine coats it, checks it, and takes care of everything for the customer,” adds Paulsen.
With a range of 3D printers, a variety of biocompatible applications, and other machines, Formacoat can meet its customers’ requirements in-house in a cost-effective and time-efficient manner. A quick turnaround and time savings can be a significant factor for medical device manufacturers.
“We’ve discovered lately that our breakthroughs are saving time for our customers,” says Paulsen. “We’ll be able to get them that much quicker in full-scale production and financial solvability just by utilising our methods, techniques, and the equipment that we have available to us. So, we’re constantly on the edge of trying something new and pushing the boundaries when it comes to coatings.”
To learn how Formacoat can assist manufacturers to find the most suitable medical device coating download the whitepaper below.