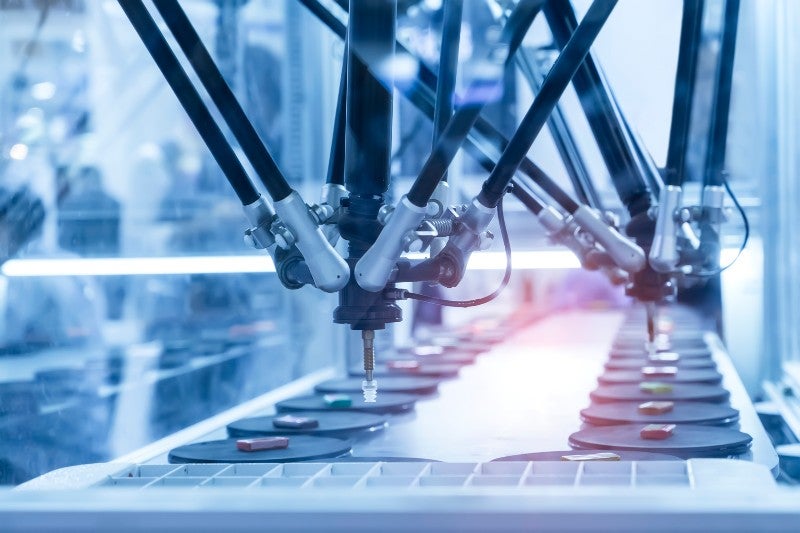
From laptops to mobile phones, almost all of us has a portable device that can remotely send and access data. While these technologies have changed the way that people live their lives, perhaps the most transformational innovation in miniaturised smart technology is in medical devices.
Miniaturised medical devices means minimally invasive, whether this entails replacing invasive surgery with guidewire implantation or switching from manual glucose level tests to continuous monitoring. With this new technology comes a range of benefits, including fewer clinical visits for patients, shorter hospital stays, and a reduced risk post-surgery.
Making medical devices smaller and smarter demands several key qualities from the components used to produce them; size must be reduced without compromising quality, application-specific qualities (such as flexible guidewire) must be reliable, and biocompatibility must comply to stringent medical industry requirements.
Bigger challenges for medical wire manufacturing
Medical wire is one component that is difficult to get right, so much so that medical device manufacturers are increasingly outsourcing. These wires not only need to be configured with the right qualities for the application (such as choosing the right metal for conductivity or flexibility), but smaller, finer wire requires greater precision and accuracy. Medical wire manufacturers need to have it all; expertise in metallurgy, process development and compliance, all whilst being able to work flexibly and quickly to avoid supply chain delays.
Custom Wire Technologies (CWT) prides itself on its ability to work closely with customers to meet their needs while offering a competitive lead time. Its extensive in-house expertise means that customers are working with a single manufacturer throughout the entire process – from design to final product, providing a simpler and more transparent supply chain.
CWT’s core capabilities include coiling, grinding and wire forming, in addition to a portfolio of value-added finish processes such as laser marking, welding and assembly. The company also works with a wide range of materials, including stainless steel, nitinol, titanium, cobalt chrome, precious metals among others
Grinding medical wire for miniaturised devices is no easy task and requires extreme precision. CWT can adjust diameters to 0.00025mm using unique machines capable of both centreless and profile grinding but is continuously looking to improve and adopt processes as demands for tighter specifications test the limits of machines and materials.
It is this striving for continuous improvement built on more than 50 years of industry experience that makes CWT the perfect partner for manufacturers looking to design and produce miniaturised medical devices. As devices in the future are projected to get smaller, CWT works to rise to the challenge.