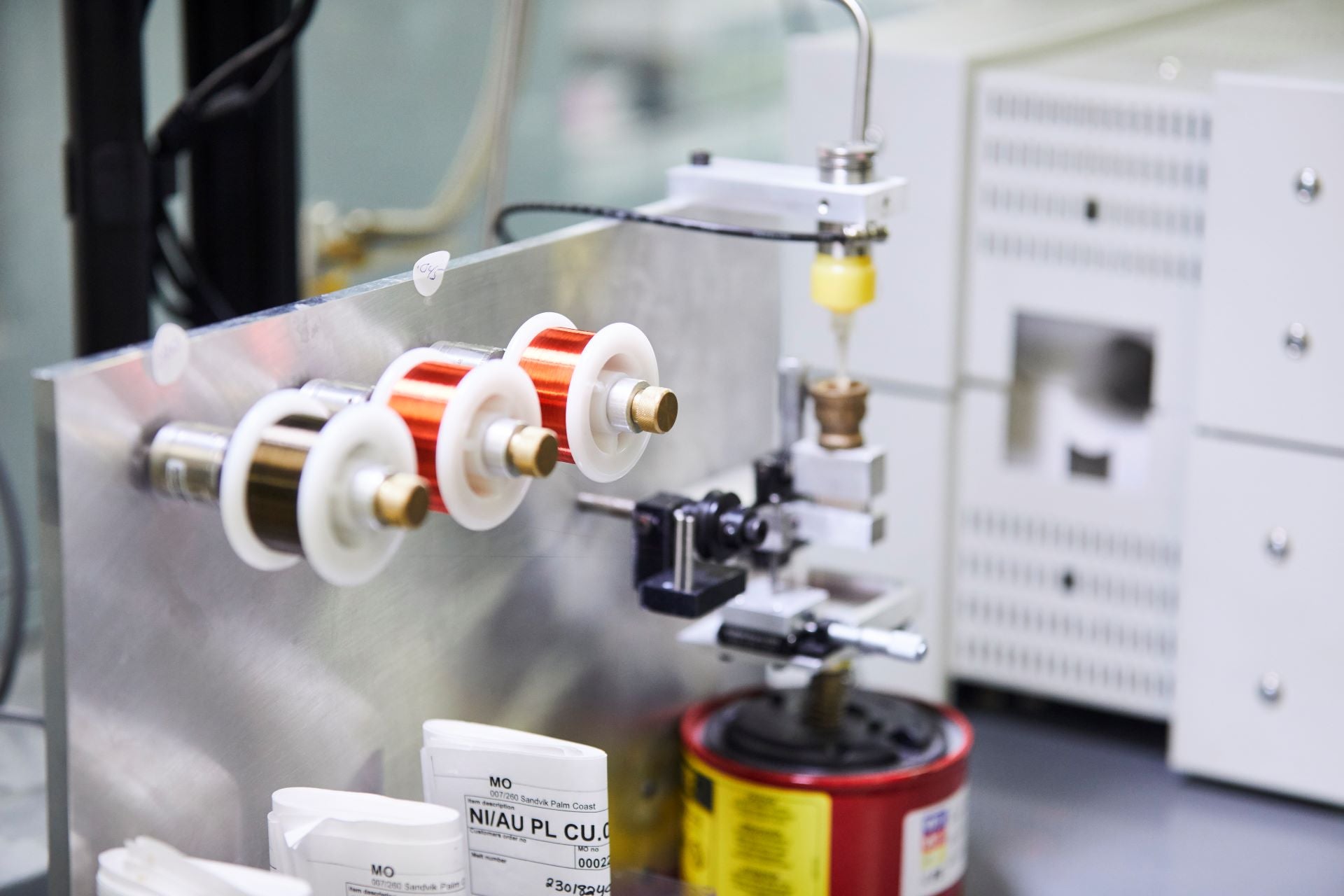
Developing a medical wire component involves a lot of choices, from the metal material itself to various configurations, such as wire thickness or coiling. According to a poll conducted during Sandvik Materials Technology’s webinar, 60% of respondents said that the most frequent design issue for them was “to find the right coatings.”
There are numerous options on the market, and ongoing research and development mean these options are only expanding. Sandvik Materials Technology offers more than forty polymer-based stand-alone dip-coating options, which can be combined to formulate a custom-built solution. Extruded coating capabilities have also been added to the extensive coating programme. Finding the ideal solution will depend on the application and factors such as whether the wire is coiled or stranded.
Polymer coatings are typically applied to wire components for medical devices to provide electrical isolation for signal transmission, a lubricious surface layer for reducing tissue damage, or to enhance biocompatibility. The standard dielectric polymer coatings can be manufactured in accordance with the National Electrical Manufacturers Association (NEMA) standards or be modified to meet customer-specific requirements.
Electroplated coatings can be used to enhance the joinability of the base wire grades, increase conductivity, or create a more noble surface, whereas PTFE is used for dielectric protection or to enhance lubricity. Solvent-based PTFE is used to provide a balance between good adhesion and good lubricity for applications such as catheter guidewires. ETFE has excellent resistance to abrasion and stress cracking.
One of the key benefits of Sandvik Materials Technology’s wire capabilities is the diameter, which can be as small as approximately 0.010mm. The company’s expertise in coating methods ensures that the extremely thin coatings are applied in a uniform and pinhole-free way, using either multiple flood or dip processes to achieve thicknesses between from 0.005 mm to 0.05mm, or an extrusion process. The flood process offers some advantages over traditional electrostatic processes, such better adhesion of PTFE to the wire, cosmetic enhancements and better thickness control. The extrusion process is used when a more precise coating is required, or solvent can’t be used.
With a materials list of more than 200 alloys, as well as a range of coatings and other surface treatments, Sandvik Materials Technology’s wire-based components are used for a variety of applications, such as vascular therapy, biosensing and neurostimulation. They have been used in a range of medical devices, including cochlear implants, pacemaker leads, continuous glucose monitors, catheters and guidewires.
For more information about Sandvik Materials Technology and its EXERA® brand or to contact them about forming a development partnership, visit their website. For more information about medical materials and coatings, download the whitepaper below.