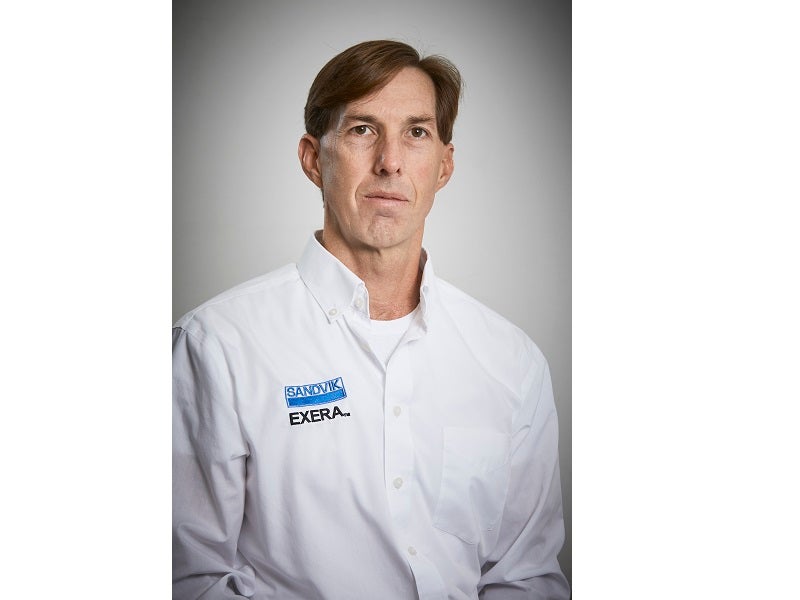
Medical Device Network spoke with Sandvik’s medical business unit manager, Gary Davies, about the company’s natural evolution into precision medical wires and what the future holds for the industry.
What sector do you specialise in?
Gary Davies: The products that we manufacture are used to sense or provide a specific therapy via stimulation inside the body. These products are used in the cardiovascular or nervous system in general, but can also be used in other parts of the body as well.
For instance, these devices can be used to determine the severity of a blockage in the cardiovascular system and then help correct the problem or stimulate tremors from Parkinson’s disease or epilepsy.
They can also be incorporated to do sensing inside the body such as temperature, blood pressure or chemical sensing, which helps provide a physician with information as to what follow-on procedures may be necessary to correct a problem.
When did the company move into the medical wire industry?
GD: Our first foray into the medical device industry was in 1999 with wires that are used in cardiovascular pacemaker leads. This was only two years after Sandvik purchased the manufacturing site in Palm Coast, which had been a privately held company prior to 1997.
When Sandvik purchased this division, it allowed us to become more involved in the medical sector, giving us better systems and the backing of a larger company that was willing to go into this risk-adverse sector.
The development was organic in nature. A large medical device OEM approached us looking for another supplier of this type of wire because they weren’t happy with the quality they were getting from their existing supply base.
We had a good reputation in the industry for high quality in ultra-fine wire sizes so we worked with them to develop the product and the systems necessary. They were very happy with the outcome and we were even able to take the majority of the market share for that particular product.
What are the main issues that your customers have and how does Sandvik help to solve them?
GD: Some of these products – because of their intricate nature – are still subject to manual processing. Therefore, one of the challenges from our customers is to build products that helps them move away from manual processes to more robust and higher capacity automated manufacturing whilst maintaining high quality.
Customers are also trying to bundle more capability into these wires than ever before. In the past, multiple materials were generally joined together to perform a certain function.
For instance, a guide wire is typically used to access and place a therapy or sensing in a specific location inside the body. In many devices, the other active parts would be made from several different materials/components that are added to the guide wire. Today, many manufacturers are trying to integrate the guiding and sensing functions in the same platform.
The advantage to this approach is that the designers can not only save space but the design is more conducive to achieving automation requirements.
This approach presents its own challenges. It becomes a much more technical material; one that has a lot of different parts that have to be joined together in a very specific and uniform way.
Where does the ability to customise or co-design medical equipment come into Sandvik’s offering?
GD: That is actually one of the keys to our business. We have a lot of different wire processing capabilities; we size the wire here and conduct any kind of thermal treatments so that they have the right mechanical and electrical properties. We can also modify the surface with different electro-plating or other techniques to change the characteristics of the surface of the material.
The range of coating capabilities that we offer not only provides electrical insulation but can be used to join materials together. We actually have a lot of different process capabilities that allow designers on the medical device OEM side to use their imagination to come up with the right solution for them.
In interactions with designers we try to provide information about what’s possible but also ensure they understand what is manufacturable from a cost perspective so that they can make the best decision for their particular product.
What resources do you have in terms of research and development?
GD: We do almost all of our own research and development onsite, working closely with customers to come up with these multifunctional composite wire solutions.
We also conduct a lot of prototyping here and have facilities set up to do that as rapidly as we can in an effort to increase the speed to market.
If needed, we can also reach out to Sandvik group’s extensive R&D team which has a fantastic knowledge bank related to materials development.
What sets you apart from your competitors?
GD: I think part of the key to our success is that we build the majority of our process equipment here onsite, allowing us an additional degree of flexibility to do things outside of the box.
And we’re not constrained to just the equipment that we have currently in-house. Once we understand what’s really required of the product, we can customise and build process equipment to meet that need. This sets us apart.
What do you think the future holds for the both Sandvik and the broader industry?
GD: The sky is the limit. This industry is going to continue to evolve and some fantastic things have already happened over the last 20 years with making these products minimally invasive, increasing patient comfort, and reducing hospital time, and I think that will continue.
The products that we are making are perfectly suited to meet those challenges and what we’ll see over time is even more novel devices that help improve people’s lives.
And we’re not just staying within our comfort zone; we’re also looking at what the next wave in technology is and trying to stay current. Sandvik will be part of that evolution as it happens, just as we have been for the past 160 years.