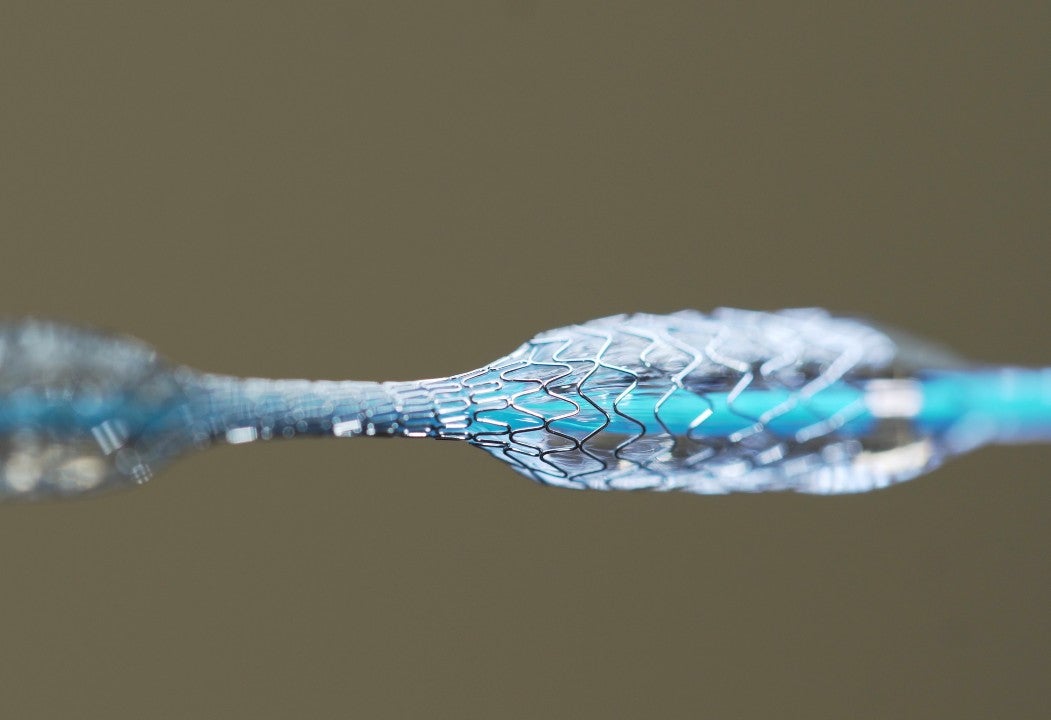
Combining metals with other elements to make an alloy with increased strength and corrosion resistance is a known practice that dates right back to the Bronze Age. Despite this long history, metallurgical discoveries are ongoing. In the mid-1960s, a team of scientists stationed at the US Naval Ordnance Laboratory discovered something new: nitinol.
By composing an alloy using roughly 55.8% nickel and 44.3% titanium, Nickel Titanium, better known as nitinol and sometimes shortened to NiTi, was born. Its unique superelastic properties and biocompatability have since made it an essential material for the medical device manufacturing industry, used in guidewires, core wires, orthopaedic wires, and a variety of other speciality devices.
Medical Device Network spoke to John Corsten, head of sales at expert medical wire company Custom Wire Technologies, to find out why.
Elasticity
“Nitinol can take up to 8% strain without plastic deformation,” he starts. “In comparison, if you imagine a stainless-steel wire, it can only take about 0.5% strain – beyond that it will stay bent.”
Imagine a guidewire application, which deals with a tortuous path within the body, and nitinol’s ability to take that strain without deforming has obvious performance benefits – avoiding kinks and ensuring the proper placement and passage of the device being inserted.
This also provides end-users with greater flexibility. During orthopaedic surgeries, doctors can bend the material in ways that will not impact the wire’s performance when compared to other alloys like stainless steel, which doesn’t have anywhere near the flexibility or strain-resistance of nitinol.
Shape setting
The other unique property of nitinol is its ability to ‘remember’ the shape it was set in with a change in temperature. “Each given grade of nitinol has a transformation temperature above which the alloy is in an ordered cubic structure known as austenite,” explains Corsten. “When you go below that transformation temperature, the alloy changes to a monoclinic crystal phase called martensite.”
Transformation temperatures for superelastic grades of nitinol are between -20°C and 22°C. This has a huge potential for medical devices. When delivering a stent, for example, the shape will collapse under the transformation temperature, making it easier to insert into a catheter for delivery. Once inside the body, the natural body temperature means it will go right back to whatever shape it was set in.
The CWT expertise
Custom Wire Technologies (CWT) has been working with nitinol for more than a decade, right from the beginning of the material’s boom in the medical device industry. “In 2010, we had a customer request a nitinol suture threader,” explains Corsten. “The threader device required the use of nitinol so it could return to the original shape after passing through the small hole in the instrument. This allowed personnel to easily load the suture through the device.
“It all just grew from there! In the past five years, it’s really gained traction to where we’re processing a tremendous amount of nitinol on a daily basis. I don’t think it will ever take over stainless steel, but I see the demand increasing and I see innovative devices being developed centred around nitinol.”
Over the years, the CWT team has built up a vast amount of expertise when it comes to shape setting and grinding nitinol. The latter can be particularly challenging due to the material’s abrasive nature and increased flexibility. The company possesses a variety of customised tools to address concerns, all manufactured in-house.
Custom Wire Technologies also has a longstanding relationship with one of the premier suppliers of nitinol in the world, putting it in a unique position to offer the latest cutting-edge advancements to customers while supporting both small start-ups and larger OEMs with the manufacture of their innovative medical devices.
To find out more about nitinol and why it might be the perfect material for your next design, download the whitepaper below.