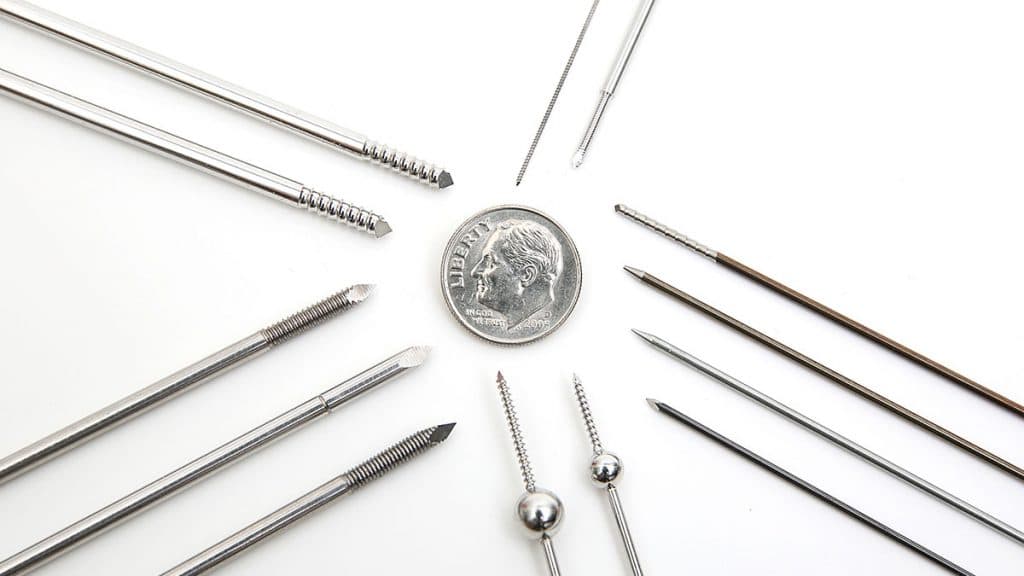
A surgical technique in use for over a hundred years, using wires and pins to hold fractured bones in place while they heal is effective and safe. Now, the latest generation of custom-designed orthopaedic wires are not only extremely precise with high tolerance, they also feature a wealth of added value finishes, from laser welding to electropolishing.
Wires, or pins, have an important role in mitigating orthopaedic trauma injuries and are also used in orthopaedic correction procedures. Stiff and straight, with a sharpened tip on one or both ends, the wires are drilled through the bone to hold fragments in place. Although primarily designed to hold fractures while they heal, wires are sometimes left in place as a definitive implant.
One of the most widely used designs is the Kirschner wire or ‘K-wire.’ A sharp, smooth wire, usually made from stainless steel, it is designed for ease of percutaneous placement, so the bone can be reached without a surgical incision. Reducing the number of incisions improves healing time and lessens the risk of infection. K-wires are often thinner than a human hair, starting at just 0.13mm diameter, and are also available in a threaded form, for extra security in holding the bones in place without withdrawing.
For fractures of large bones, or for veterinary use, Steinmann pins are more commonly used. Although used in a similar fashion, Steinmann pins are larger than K-wires, with diameters starting at 1mm.
Olive wires are used to treat fractures that have very small fragments or are near joints, such as feet. Widely used in corrective treatments such as post-trauma residual misalignment, and limb deformities, olive wires use tensioning, and sometimes circular rings, to stabilise the bone fragments.
According to global market studies, the medical wire market is predicted to expand at a CAGR of more than 6% between 2020-2030, and medical wire is being used more frequently to provide less invasive surgeries. This trend is expected to be further enhanced by the latest innovative technologies.
Custom-designed orthopaedic wires
Medical interventions sometimes require more specialised wires with customised tips and finishes. As a leading medical component manufacturer, Custom Wire Technologies (CWT) has over 50 years of industry experience and provides a customisation service that includes some of the latest technological advancements.
Micro-grinding – For wires, tolerance is achieved through superior micro-grinding capabilities, requiring a combination of meticulous attention to detail and high efficiency, to produce accurate components at a rapid rate. CWT specialises in core wire centreless grinding and has also perfected the process of micro-grinding nitinol (nickel titanium), which requires highly specialised grinding wheels and coolants.
Laser welding – For ultra-fine wires, laser welding is used. Most used on projects such as hypotubes, guidewires, cannulas, and needles. Specialised laser welding can reduce lead times and supply chain issues on complex devices.
Laser and ink pad marking – Lasers are used to add unique identifiers or depth bands to K-wires and pins to give feedback to how far a component may be inserted. Medical-class black ink can also be used for depth marking pins or for product number identifiers.
Passivation – A light coating, such as metal oxide, creates a protective shell around the wire, protecting against corrosion. This process also removes any free iron from the surface of stainless steel while creating the passive chromium oxide layer.
Electropolishing – Metal is removed from the surface producing a unidirectional pattern that is both stress and occlusion free.
Nitinol K-wire
Another example of innovation is Nitinol K-wire, the ‘super-elastic’ metal that remembers its shape. “The demand has increased dramatically over the last five years,” says John Corsten, technical sales manager at CWT. “This is due to its memory properties and ability to take much more strain versus stainless steel. We have also developed a robust process to thread Nitinol.”
CWT prides itself on its ability to work closely with customers to meet their needs. “Everything we produce is custom. We simply require a sketch or print for our engineering team to review,” says Corsten. “Companies tend to gravitate towards Custom Wire due to our customer service and overall responsiveness.”
CWT is continuing to lead the way forward with the latest technological advancements for orthopaedic wires, ensuring precision, accuracy, and high tolerances. After all, they must provide patients with a lifetime of service.