
Californian firm DJO Global is one of a burgeoning number of medical device manufacturers now using robotic automation in its manufacturing processes.
A US designer and provider of orthopaedic braces, implants and pain management products, the company operates a ‘mobile robotic warehouse system’ that uses 50 robots developed by Massachusetts-based Kiva Systems to shuttle 500 inventory ‘pods’ between storage areas and fulfilment stations.
Although this technological transition has led to some fundamental changes in how the company is structured and operates, the investment made in this cutting-edge machinery has, just as importantly, already paid for itself within two years of implementation. Scroll back two years to 2009 and DJO had a warehouse operation in Indianapolis employing around 130 people who were manually taking orders and picking products.
"Staff were having to go through the warehouse, pick items off the shelf and scan them into the computer, pack them into a box and then send them to the shipping station," explains DJO Global’s senior vice-president of lean and enterprise excellence Jerry Wright. "We were also paying for a lot of overtime and we had around 45-50 temporary staff working in addition to the full-time employees – and this was all because of the amount of time they were having to spend picking orders.
"We have about 10,000 different parts in the warehouse, which can be pretty time-consuming when you are picking up 1,500-2,000 orders a day. A lot of people were going round and round the warehouse getting orders completed," he says.
The solution was to turn to Kiva Systems’ Mobile-robotic Fulfillment System: small robots that are able to move around a warehouse floor responding to and picking up orders as soon as they come in, and working with much more accuracy and efficiency than human staff.
How well do you really know your competitors?
Access the most comprehensive Company Profiles on the market, powered by GlobalData. Save hours of research. Gain competitive edge.
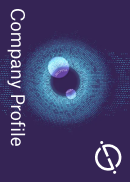
Thank you!
Your download email will arrive shortly
Not ready to buy yet? Download a free sample
We are confident about the unique quality of our Company Profiles. However, we want you to make the most beneficial decision for your business, so we offer a free sample that you can download by submitting the below form
By GlobalDataThe technology is already being implemented in many warehousing environments, with online retailers and names such as Staples and Walgreen Drug using such technology extensively. Because medical device manufacture orders need to be absolutely accurate when picked and are not normally large in terms of the product or device’s physical size (one area where robotic systems can fall down), robotic automation is a viable picking option for the industry.
"With the new Kiva system, the product picking is all handled by the robots, which can bring the order to the operator based on what it is," explains Wright. "The robot will bring the order to the shipping station, laser mark which area to pull the product from, and the operator scans it to confirm it is the correct number and configuration. Then, while the operator is packing the order, the robot can go off and get the next items. By switching to this new system, we have been able to reduce all of our temporary employees and go back to normal overtime.
"Moreover, although it involved a $2 million investment to implement it, we have calculated that we are saving about $1 million a year. So, given that we changed over to robotic technology in 2009, it has already paid for itself," he says.
Automation implementation
When getting started and choosing the right product, Wright advises, it was very much a case of researching thoroughly in advance. "We talked to Kiva and went to see the system in action at a Staples store in Washington DC to see how it worked for them. Instantly we recognised that, whereas they had 80-90% of orders being picked up by the system – with the remainder simply being too big for the robots to pick up – in a facility such as ours those sorts of unmanageable volumes were going to be fairly small," he points out.
However, the transition to the new system has also thrown up some interesting challenges, not least around whether the same headcount numbers will now be needed and, if not, how the trimming process will be effectively managed so as to avoid damaging productivity or morale.
"Now we are at the point where, having had a total headcount of 120-130, we are aiming at more like 70-75. It is never easy to say you no longer need people and any change like that must be carefully managed, but we have tried to be upfront and transparent in all discussions we have had," says Wright.
This challenge aside, the company has seen significant improvements in order fulfilment and accuracy, as well as a 50% increase in warehouse productivity. "Now it is all completely computer-controlled, we have a better handle on what is going out and what is currently in the system. We have been able to expand our order volume and warehousing, which has more than justified the investment," he says.
"It is also easier to prevent miscounting because everything is automatically scanned in by the robots. This has given warehouse staff the opportunity to transfer their skills to other areas – for instance, they used to spend a lot of time using RF scanning guns, but now their role is more PC-based and involves maintenance work to make sure the robots are functioning properly. "Of course, there are several drive units in place to provide back-up; you do need to have a means of back-up," he adds.
Is the future robotic?
"I think you will see more and more medical device companies moving in this sort of direction over the course of the next five to ten years," Wright declares. "There is a much lower risk of grabbing the wrong thing off a shelf and it is a lot easier to ensure that the inventory is correct."
Wright’s advice for others interested in implementing a robotic system is simple. "The thing to do, as with anything like this, is to go and speak to someone who is already running it and see how it works for them. It is never going to be perfect, but any opportunity to automate something and make a process more efficient is usually worthwhile and more consistent than employing humans to do it," he says.
As for whether this is another, inexorable step towards the inevitable domination of the world by robots, Wright laughs. "The robots are designed to work only inside a specified perimeter, but if they did bump into something unexpectedly – and there would have to be a serious issue with their guidance systems for this to happen – then they would simply stop," he points out.
The upshot for medical device manufacturers is that this sort of cutting-edge technology is now clearly becoming a viable, cost-effective option; one that can make a significant difference to an organisation’s warehousing capability.
Inevitably, a big change such as this will always be viewed as risky and shifting company mindset away from the old to give the new a chance can be a challenge; however, for Wright, it has been a gamble worth taking. "If you’re into technological advances, this is up there on the leading edge. This is new, it involves taking a leap of faith, but for us it has definitely been worthwhile. There is very much a risk/reward scale," he declares.
"For the first four to six months we spent very long days troubleshooting, resolving issues and making sure the system was generally bedding down, but now that we are on the other side we are very relieved to be here."
Advantages of robotic automation
– Increased order picking productivity
– Significant reduction in order cycle times
– Reduction in use of peak-time agency workers
– Increased ability to react to changes in product or demand
– Increased accuracy and flexibility of picking
– Single orders can be picked in their entirety or multiple orders picked simultaneously
– Existing workers are freed up to focus on more value-added tasks.
Disadvantages of robotic automation
– Potential redundancies
– Possible re-examination of working practices and audit of workflow
– Extra training of remaining workers may be required
– Need for back-up processes and procedures to protect the business should the new automated technology fail.