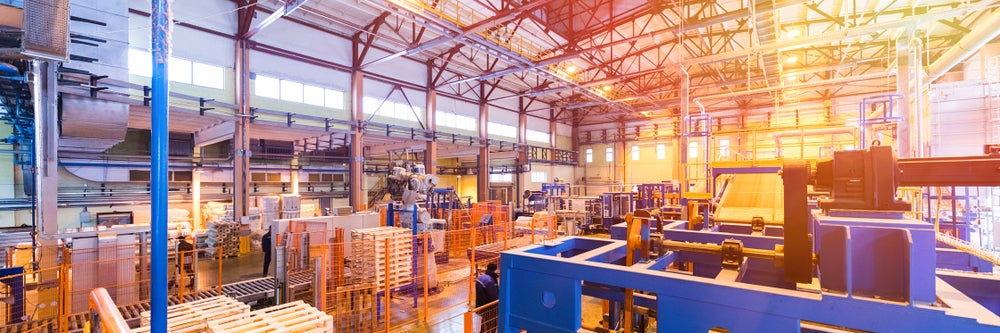
With medical device sales expected to exceed $700 billion by 2030, finding innovative materials to advance device development is a primary focus for all manufacturers. Yet medical device engineers are facing huge challenges – from supply chain disruption to navigating the EU MDR’s regulatory requirements.
Jacqueline Anim is a senior principal materials engineer at Ethicon Inc. and regarded as one of the industry’s leading voices in material science. As principal materials engineer and a consultant for Ethicon, a subsidiary of Johnson & Johnson (JNJ), Anim currently serves as a cross sector subject matter expert for the company and provides direction in the identification and selection of polymer base materials across JNJ.
In 2019, she was voted Professional Engineer of the Year in her field of Engineering and honored as the 2019 Woman of Excellence/Industry Leader in her field of engineering. In an exclusive interview with Medical Device Network, Anim discusses the industry’s regulatory requirements and how material trends are impacting the sector. This interview has been edited for clarity and length.
CL: What do you see as the biggest challenges facing material engineers and suppliers today?
From my perspective, I think that there’s quite a few challenges with changing regulations. One of the key topics, is the introduction of the new EU MDR and how materials engineers are navigating to meet these new regulations. It’s always been a moving target when it comes to standards, regulations, and requirements and while technology continues to be enhanced, the regulation is always ahead of us. So, everyone is working to the requirements.
One of the key discussions point this year at this year’s MD&M conference was EU MDR and maybe, potentially in the very near future, there’s also great concern with the Per-polyfluoroAlkyl Substances (PFAS) which is proposed for ban in Europe. This will drive a shift in base business for all device manufacturers targeting to market products in Europe.
CL: The EU MDR is driving more intense scrutiny around the chemistry of the raw materials. How are material engineers navigating that?
The EU MDR has a two prongs approach to it, a qualitative and quantitative analysis aspect. So the qualitative is very easy to do but when it comes to the quantitative side where we have to quantify if you have up to about 0.1% weight by weight, or CMR and/or EDC’s that is where the challenge is and it’s a lot of time and resources that needs to be put in to do a lot of the extractions and the quantification to determine whether you are within the threshold or under the threshold. It’s a slow process which doesn’t happen overnight, and there’s a lot of time and resources that is put in to provide that quantitative response.
How well do you really know your competitors?
Access the most comprehensive Company Profiles on the market, powered by GlobalData. Save hours of research. Gain competitive edge.
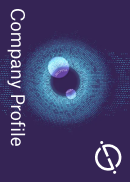
Thank you!
Your download email will arrive shortly
Not ready to buy yet? Download a free sample
We are confident about the unique quality of our Company Profiles. However, we want you to make the most beneficial decision for your business, so we offer a free sample that you can download by submitting the below form
By GlobalDataCL: What about on the supply chain side?
There was a major shift in the global supply chain during the Covid-19 pandemic era and its effects continue to be felt due to slow recovery. Even though there’s been significant recoveries some areas continue to feel the aftermath of severe disruption and turmoil in logistics across trade and other industries. Case in point during the pandemic most of the suppliers shifted their focus to Covid-19 essential materials i.e., textiles and soft medical fabrics, masks technologies and 3D-printable, gloves and other chemistries essential to mitigating the pandemic. As an illustration point, the medical suppliers and supply chain drifted from operating room or scheduled surgery device materials to Covid-19 essential materials e.g., Polypropylene, Polyethylene, ABS etc.
With that, the supply chain after the pandemic has now recentered itself on medtech materials and with that is the regulation challenges.
I think in the post pandemic era, the industry has adapted and is now looking at multiple suppliers instead of having just one main supplier. Companies understand they need a potential backup should the main one run into any manufacturing issues and even the material suppliers themselves have adapted.
If we look at material chemistry, there are some ingredients that are labelled vulnerable ingredients and those are the ingredients that vendors are looking for backup sources. They normally coming from small, sub suppliers with a longer lead time and fall into a category called exotic additives.
Therefore, the industry is looking for alternative suppliers for those type of exotic ingredients and this has been common among most of the suppliers I’ve talked to. On the geopolitical side, from my lens, the industry has not felt an impact because most of the suppliers were not coming from Russia or Ukraine so there’s been minimum disruption on that side.

CL: Has the EU MDR overall been a positive for the industry?
That effect is yet to be measured because the EU MDR is a new requirement, and its sunset date has been adjusted so we are currently in the motion and movement towards compliance. There’s been a lot of revision relative to the required date when it’s going to be in full force. So, the last adjustment was for implantation devices to be ready by December 2027 and the low-risk medical devices have an extension up to December 2028.
But it’s been an area of high concentration when it comes to engineering resource, regulatory resourcing and putting systems in place requires a strategy. You cannot approach it lightly.
Then, if companies didn’t have a department for EU MDR compliance before, they’ve had to put one in place. All these engineers are focusing primarily on getting the information ready and getting the databases and everything in place to meet those requirements. Also, they have to multiply it by the number of devices that they have so if you have 500 devices on the market, and some of them are due for re-registration, you need to accommodate that many devices going through the EU MDR path.
CL: What are the material trends that are emerging, or companies should be looking out for?
The momentum is back to where we were before the pandemic and there’s a lot of work being put into research and development in specific material areas such as plastics and coatings.
In terms of innovation, there are a couple of areas that some suppliers are focusing on in connection with the current connectivity technology that is out there. The cloud, 5G, paintable conductive materials that allows the development of miniaturized devices that are very like micro devices for a third of the size of a pellet and some of the chemistry is so potent, they do allow this type of technology to be executed, something that was not available several years ago.
So, there are a lot of technology enhancements in areas of connectivity and sensory capability and coatings that are very conductive for electricity and other effects. This is an area that I find very interesting, and I am excited about.
There’s also been a lot of talk around sustainability, which can be defined in various angles. We have the biomaterials sustainability, then we have the traditional material sustainability or design for sustainability, sustainability for manufacturing, environmental sustainability, and end of life management sustainability. Also, there is reclaim ability where a device that’s been in the OR can be reclaimed from the OR and used in a lower tier application.
All these type of sustainability options are being discussed and various organisations are handling a little piece of the whole ecosystem. We can see that material sustainability is going to be big moving forward from an environmental conservation and environmental sustainability perspective and where these areas can be coupled together is an area of concentration moving forward.
CL: What are the key milestones for Ethicon this year?
In 2023 we are gearing up and looking forward to organizing our third mini conference on site that is going to be in Cincinnati, MedTech Engineering Centre, focusing on medical materials and guidelines.
We’ve been hosting this for the past couple of years and we’re getting ready to bring all the suppliers back on site to continue the discussion because we’ve seen that it’s been very fruitful for the years that we’ve had it.
For patient care, there’s always been a missing link between the material suppliers and the device manufacturers. In the past, there were no communication at all. There were some suppliers that did not even know that their product were being used in medical devices – there was no connection at all!
This mini conference has helped bridge the gap and even though it’s hosted on a designated JNJ campus, it is not just for the benefit of Ethicon and Johnson and Johnson. The content is always published in the form of a white paper and it’s available for the entire industry to use in making good decisions when it comes to material selections for medtech products.