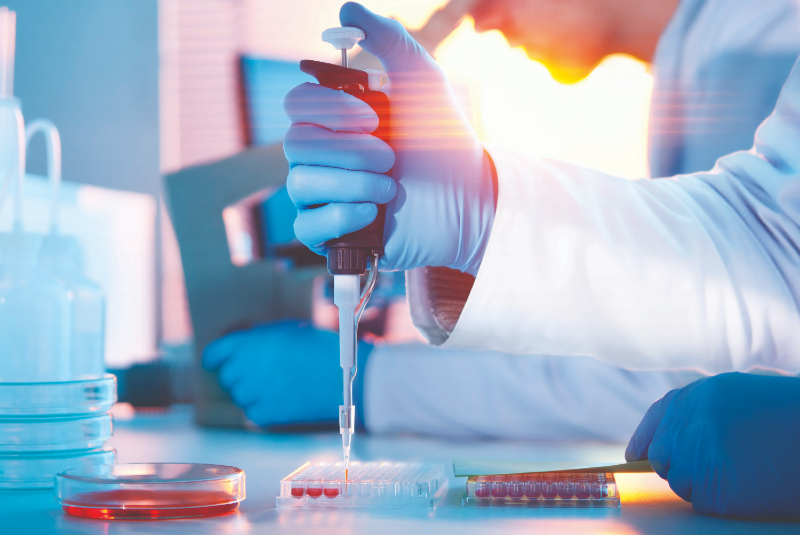
Since 1922, Watlow® provides leading medical device and clinical diagnostic equipment OEMs with proven solutions that enable exceptional thermal control. The company accomplishes this with rapid prototypes and leading thermal technologies that meet the most demanding product specifications. Watlow has developed a broad product offering, including heaters, sensors and controllers, all the components in an integrated thermal system, for medical and clinical equipment where uniform operating temperatures are required for effective performance.
Andy Selvy is Watlow’s chief system designer focused on layered heater technology and the medical, clinical and analytical business segment. He holds an MBA and a bachelor’s degree in ceramic engineering and has worked at Watlow for 16 years.
Which future developments do you expect to see in the medical and clinical diagnostics market?
There are several trends we see in this market, which create unique thermal challenges. A few examples include the miniaturisation of devices, increased throughput for diagnostic equipment and a shift towards point-of-care diagnostics focused on preventative care and faster medical decisions. From the OEM customer perspective, we also see increased globalisation efforts such as leveraging a single device in all regions of the world. This creates challenges with different global voltage requirements and increasingly stringent device safety standards.
Which applications in medical and clinical diagnostics use Watlow’s thermal solutions?
Watlow supports the world’s leading companies across a very broad set of applications in this market. Some of our top application areas for medical devices include kidney dialysis, contrast media warming, sterilisation and respiratory therapy equipment. In clinical diagnostics, we participate both in central lab applications such as immunoassay and clinical chemistry equipment as well as smaller device applications such as molecular diagnostics and genomics.
How can Watlow products help in medical and clinical diagnostics equipment?
I will give you an example by speaking about enabling miniaturisation and high performance. Our ULTRAMIC® advanced ceramic heater product enables incredible thermal performance up to 155 watts per square centimetre in a package size as small as 8 x 8 mm square and includes onboard sensing for closed-loop temperature control. So advanced ceramic heaters allow equipment designers to free up room for new components, reduce the machine’s overall footprint, increase performance as well as simplify the manufacturing and assembly process.
What are the benefits of Watlow‘s heaters, sensors and controllers in medical and clinical diagnostics and what are a few of your reference projects?
There are three main areas that differentiate us.
- Our broad experience spans across many applications and allows us to solve challenging thermal problems. We leverage our past experience to solve new challenges and we also have a broad standard product offering to enable rapid prototyping and fast cycles of learning.
- We take a systems view versus trying to optimise just one component. Customers come to Watlow because we understand the regulatory environment they must operate in. For example, when talking to a new customer, we do not ask what type of heater, sensor, or controller they are interested in. Instead, we first explore their strategy for dealing with challenges at the device level such as the electrical safety standard EN 60601-1. This type of collaboration at the system level very often leads to new solutions that would not have been possible focusing only on Watlow component design. One specific example of this was working with a medical device company that wanted to use cartridge heaters in a metal block as a heat source but needed very low electrical leakage current to meet that safety standard. They were planning to use an expensive, bulky isolation transformer to reduce the voltage supplied to the heater. By understanding the system architecture we were able to recommend a different heater technology, which could easily meet the low leakage requirements at all global line voltages. Not only did this eliminate the cost of the isolation transformer from the system, but it also helped significantly shrink the device footprint.
- Watlow is a global company with almost 100 years of experience solving the toughest thermal challenges. With long design and product life cycles in this market and increasing decentralisation of design and manufacturing activities, customers must be confident suppliers can support them now and in the future – wherever they need it. A recent example of how Watlow supported a leading medical device company was through a global technology summit to share our advanced capabilities and jointly discuss technology roadmaps. This event happened simultaneously across two locations in Europe, two in the U.S. and one in Asia. Watlow had in-person representation to answer technical questions as well as product demonstrations in all five locations. Our global footprint and sales channel allow us to support our customers wherever they may be – now and in the future.
What effects did you experience from the Covid-19 pandemic?
During the pandemic, we have all experienced an unprecedented and challenging time. Most of our team members are still working remotely, and for our production staff, we have established the highest safety standards. In addition, several Watlow products have been used to help during the pandemic. For example, a medical device manufacturer is using our ULTRAMIC advanced ceramic heaters in a product that treats Covid-19 patients. This treatment is proving effective to keep people off of mechanical ventilators and helping them recover faster. Also, Watlow’s foam-in-place silicone rubber heaters are being used by a medical components company for Covid-19 vaccine testing. Additionally, Watlow EZ-ZONE PM controllers are being used by a company to control airflow and negative vacuum conditions in makeshift hospital tent systems.
Not only are we helping people affected by the virus, but this project has also inspired Watlow team members as well. Some of our engineers have been using 3D printers to make face shields for production team members. Also, a team of engineers from various locations virtually came together to create infrared temperature taking systems for our facilities. Even in these challenging times, we are proud of the innovation and commitment shown by our team and the support we have been able to show to our valued customers.