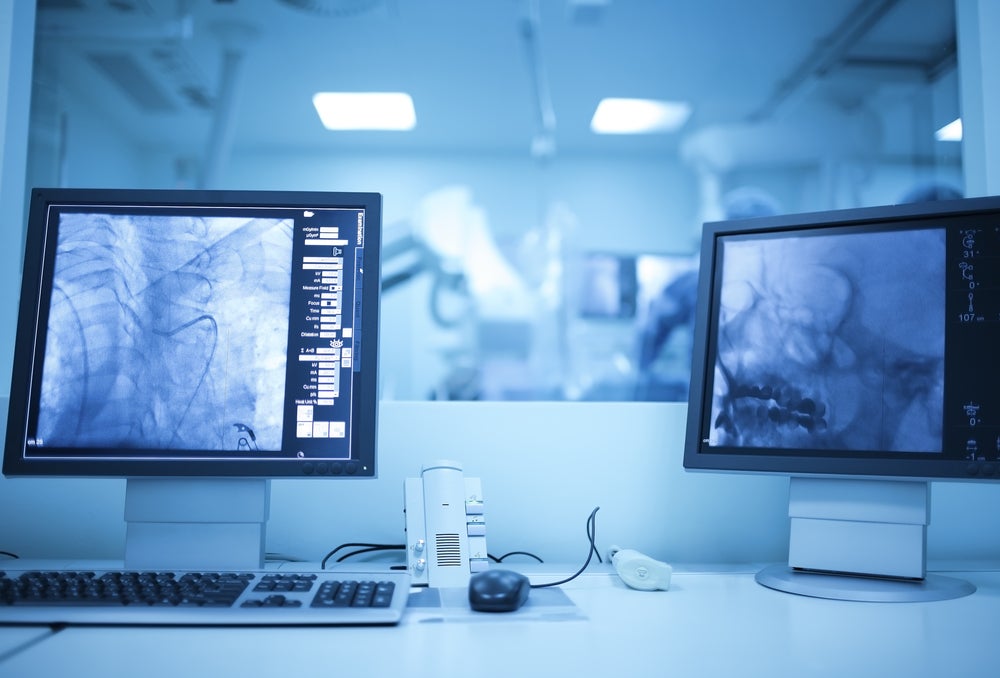
Catheters are important tools in the healthcare sector, with use cases across a variety of interventional cardiology and peripheral vascular procedures.
Diagnostic catheters are used to capture critical information about a patient’s cardiac anatomy through electrophysiological mapping. Dilatation catheters expand small and tight lesions with balloon technology, while other designs are intended for the placement of therapeutic devices such as valves and stents.
According to GlobalData, there are currently 137 cardiac catheters (angiography and guiding devices) in the R&D pipeline, in addition to 86 PTCA (percutaneous transluminal coronary angioplasty) balloon catheters in development.
Design considerations
The creation of a new device is a complex process. During the R&D journey, various key design considerations can have a huge impact on the device’s ability to cross tortuous segments while transmitting torque all the way from the proximal to the distal end.
Each new catheter concept requires a clear indication for use that will drive all design choices and performance considerations, including outer-diameter profile, kink resistance, steerability, flexibility, pushability, lubricity and torque transfer. These are typically driven by the specific anatomy of the vessel the device is intended to navigate.
Once the ideal performance attributes have been decided, it is time to consider how the three core components of a catheter – its shaft, reinforcement layer and outer layer – should be designed to deliver the best results.
While the choice of material used to create the inner layer can have a large impact on steerability, flexibility and kink resistance, the importance of reinforcement should not be overlooked.
Reinforcement layers can offer significant improvements to the torque response and overall column strength of the device. They can also facilitate the development of more complex or advanced designs, including catheters with ultra-thin walls for neurovascular access.
With any new catheter, engineers have an important choice to make between braid reinforcement or coil reinforcement. Both use metal wire, but each option offers different performance benefits and design possibilities.
Braids
With braid-reinforced catheters, the wire is made up of multiple strands, which are interwoven to produce one strong, durable component. There are many ways to customise the design, including tweaking the size and density of the wires, the braid angles and the pitch.
If burst pressure – the pressure that a tube can handle before rupturing – is a particular concern, braid reinforcement can be a great choice. Superior torque control is another advantage of braided designs.
However, while braided tubes often provide a good level of flexibility for the catheter shaft, they can sometimes fail by kinking or twisting during use.
Coils
Coil-reinforced designs, featuring an internal helical-coil spring, are typically chosen for their improved kink resistance, which helps to prevent the catheter from twisting and collapsing as it progresses through tortuous vessels. This enables quicker, easier and more successful procedures.
The beauty of coil reinforcement is that while the helical shape provides strong resistance to kinking, it can still offer sufficient flexibility for navigating sharp-angled bends.
The coil can be adapted in various ways by playing with the diameter, pitch and stiffness. This can improve the device’s ability to resist deformation.
Material choice can have an impact on properties, with the use of nitinol becoming more popular due to its ability to take a high degree of strain before deformation.
In some designs, coil pitch can be varied along the length of the component, offering more flex at the distal end for a less traumatic procedure.
Moreover, to get the best of both worlds and achieve optimal results, some designers have leveraged a component that transitions from a braid into a coil.
A valued partner
Custom Wire Technologies (CWT) is a US-based contract manufacturer of high-quality wire components for medical devices. The company is a valued partner to many original equipment manufacturers working in the R&D stage and beyond.
CWT has been producing catheter-reinforcement coils for 20 years. Recently, it launched an expedited service, QwikCoil, to turn around orders in just one week’s time.
To learn how CWT’s expert coiling capabilities can help you deliver the best catheter for your needs, please download the whitepaper now.