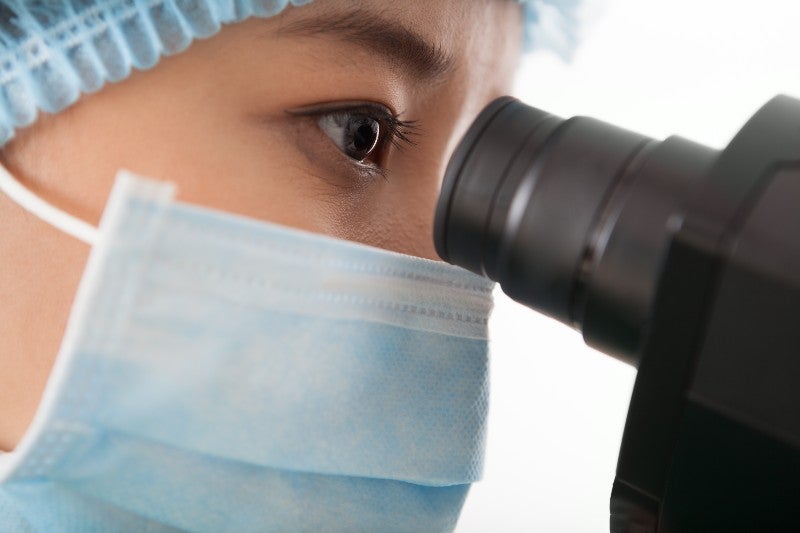
Due to a growing and ageing population, demand for medical devices is ever-increasing. By 2030, GlobalData forecasts the medical devices market to reach a value of $700bn. As the industry grows, there is an increasing focus on quality management across the manufacturing and use of its products.
This is where regulatory bodies such as the International Organization for Standardization (ISO) come in. To ensure all medical devices meet the proper regulatory compliance laws, ISO developed ISO 13485, an internationally agreed standard that sets out the requirements for a quality management system (QMS) specific to medical device manufacturing.
Due to the high risks that a faulty medical device could pose to patients and doctors, it’s obvious why quality is a top priority for this sector. But for medical device companies, there’s a cost element at play too. Multiple reports have shown that, in the event of major recalls and other quality-related issues, medical device manufacturers risk losing a significant portion of their market share.
Quality assurance and quality control
Adhering to an ISO 13485-compliant QMS centred around two important concepts – quality assurance and quality control – can help manufacturers avoid this possibility. Quality assurance involves incorporating quality into every stage of a device’s production, while quality control involves testing product samples against their specification to guarantee consistent, high-quality output.
Both are essential requirements of the medical device manufacturing line, but how can companies ensure that components they source from external suppliers follow similar standards? Let’s consider medical wire used in devices such as guidewires and catheters.
Original equipment manufacturers (OEMs) often source custom-made medical wire solutions due to specific requirements for length, diameter, and other parameters. According to Dheeraj Verma, quality technician at Custom Wire Technologies (CWT), the physical dimensions, mechanical properties, and appearance of the medical wire component can all affect a product’s fit, form and function. This means the quality of the whole medical device, and ultimately the safety of the patient, is at risk.
“Failure to meet the quality requirements of a component or device could cause a failure in the intended application, affecting patient safety,” Verma explains. “At CWT, we take pride in manufacturing our highest quality products by following all customer requirements. We pay attention to every detail. Our experienced engineering and quality team determine specific manufacturing processes by following all quality requirements for product conformity.”
A quality process for quality wire
Manufacturing a quality medical wire component starts, of course, with top-notch raw material. “At CWT, not only do we purchase from industry leading suppliers, but all raw material also goes through a very detailed incoming inspection process to ensure conformity of the material,” says Verma.
Because product quality depends on close attention to detail, CWT works directly with its customers to understand the end-product’s functionality, use, and requirements before developing in-depth instructions, manufacturing processes, and inspection plans.
“We have multiple layers of inspection during our manufacturing process to assure we manufacture top-quality products,” says Verma. “Quality inspection of all products is performed both during production and before shipping products to our customers. In addition, the quality department perform daily audits on manufacturing process steps to assure that the correct manufacturing processes are being followed and customer requirements met.”
This dedication ensures the US-based supplier meets its internal quality standards (certified to ISO 13485) as well as customer-defined requirements. Precise inspection equipment is used by the quality team to check parameters such as diameter, length, pitch, surface finish, radii, angles, and pull strength, among many others.
“These product dimensions are defined by the customer and put into inspection plans by the quality department. To verify product conformity or nonconformity, we use vision systems by Micro-Vu and Keyence, laser profilers, micrometers, digital micrometers, microscopes, calipers, strain gauges, multi-meters and other hand equipment,” explains Verma.
When manufacturing products intended for implantation inside a patient’s body, there is no room for error. Custom Wire Technologies has been a trusted partner to the medical device industry for the past 20 years. Its dedicated team of experienced engineers continue to serve the industry with world-class medical device components and assemblies that satisfy customers’ bespoke requirements and need for quality.
To find out more, download the whitepaper below.